- GD.findiが解決できる課題
- 製品紹介生産活動の現場とサイバー空間をつなぐ 生産シミュレーション
GD.find MS
Modeling & Simulation
ライン設計を強力に支援する完全ノーコード生産シミュレータ - よくあるご質問
- 事例
- ウェビナー
- お役立ち情報
Best For You
工程在庫の最適数を知りたい
- Home
- /
- Best for You
- /
- 工程在庫の最適数を知りたい
1.在庫管理の問題、課題
製造業において、在庫管理は経営に関わる永遠の課題です。在庫管理では常に、過剰在庫と欠品という、相反するリスクが併存します。
ご存じの通り、在庫を保持することはキャッシュフローを悪化させる原因であり、貸借対照表(バランスシート)を崩して資金繰りを圧迫するため、継続的な企業経営を行うためのひとつのポイントとなっています。ですから、経営サイドは生産部門の在庫を圧縮する必要があり、生産部門の皆さんへも在庫削減を強く求められることとなります。
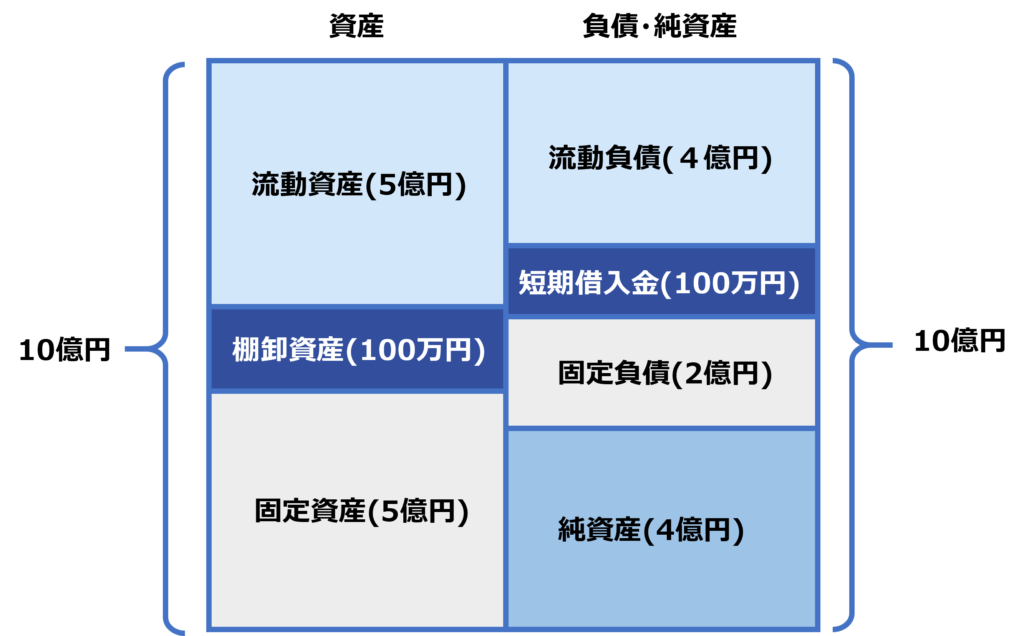
経営側の要求を受けた生産部門、特に生産管理や調達部門では出荷計画に基づいて部材の調達計画を最小化する計画を立てるわけです。ここで、欠品リスクを極度に恐れると過剰在庫につながり、過剰在庫リスクを恐れると欠品を招きます。在庫管理の要はこの相反する要素の関係を継続的に維持することですが、それは決して容易ではありません。
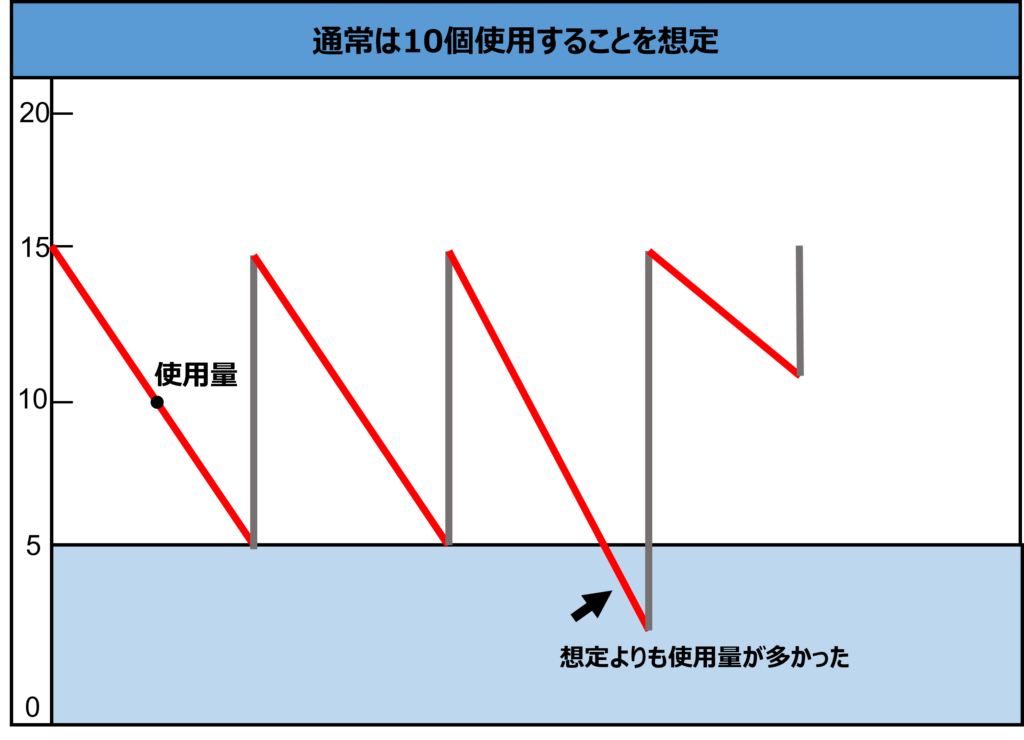
在庫管理において解決すべき課題を具体的に列挙すると、業務の効率性というより、そもそも、今日の変動の時代に対応した在庫管理の方式を求める声をはじめとして多岐にわたるのがわかります(下記)。
- 標準在庫をどうやって設定するのかがわからない
- 市場変動に対応できる適正在庫を実現したい(過剰在庫を削減したい)
- 誰にでもできる在庫管理にしたい(自己流・属人化からの脱却)
- 先代から引き継いだ在庫の多さに危機感がある
では在庫管理にまつわる様々な問題に対して、どのように解決方法を模索するべきなのでしょうか?
2.在庫管理の問題解決に向けたアプローチ
製造業と在庫管理の問題は切っても切れない関係にあります。しかし、「標準在庫の設定」という、在庫管理の問題に対する方式は確立されていないのが現状です。
なぜ、標準在庫を設定することが難しいのか、それは自ら設定したの生産計画をその通りに実行できずに各工程の生産量が変動することと、需要側による出荷計画が変動することの間で、製品在庫や工程間在庫の変動を予測することが「ヒトの勘と経験」では難しくなってきたからです。従来の製品種が少ない場合や、特定のユーザの発注体系や特性がわかっている時代では、現場を知り尽くした生産管理者がこの揺れを察知して、適切な在庫量を押さえていました。しかし、皆さんもご存じの通り、製品種は増え、ユーザも増え、また、ユーザからの出荷要求の傾向も様々に変わってきました。この状況で、欠品リスクを避けるためには、安全側に在庫を積み増ししておくことしか打ち手はありませんから、在庫は増えていく特性を持っているわけです。
そして、在庫はだれの目にも止まるものですから、生産現場の事情がわからない経営層からは「在庫が多い」という指摘を容易に受けがちになります。仮にそれが本当に最低必要な在庫であっても、「なぜ、ここでこの程度の在庫が必要なのか」を定量的に説明することは難しいのはご存じの通りです。
これに対する問題解決のアプローチは唯一、在庫の変動を予測する、ということに尽きます。
ここで提案したいのが、シミュレーションを活用した仮想実験です。適切な標準在庫とは、すなわち、どうすれば過剰在庫や欠品のリスクを最小限にし、効率よく在庫を回せるか…考えても分からなければ、シミュレーションを使って「やってみる」のがこれからの時代での有効な対応方式です。
ちなみに、「引き取りカンバン」を活用して在庫を低減する方法もありますが、組織内部の管理範囲に留まることと、製品種が多い場合にカンバンを利用すると、適切なカンバン選択が示されないため、返って在庫を増やしてしまう結果になってしまいます。
生産計画に対する製造部門の各工程の揺れと、需要変動の仮説を組み込んだ出荷計画の揺れを仮定して、どのような条件下で欠品や過剰在庫がどこに発生するかを確認し、実験を繰り返す…シミュレーションを活用すれば、最適な在庫管理の実現に向けて大きな一歩を踏み出すことができます。つまり、変動を想定した計画で自社が採るべき行動を設計することこそが、根本的な問題解決に繋がります。
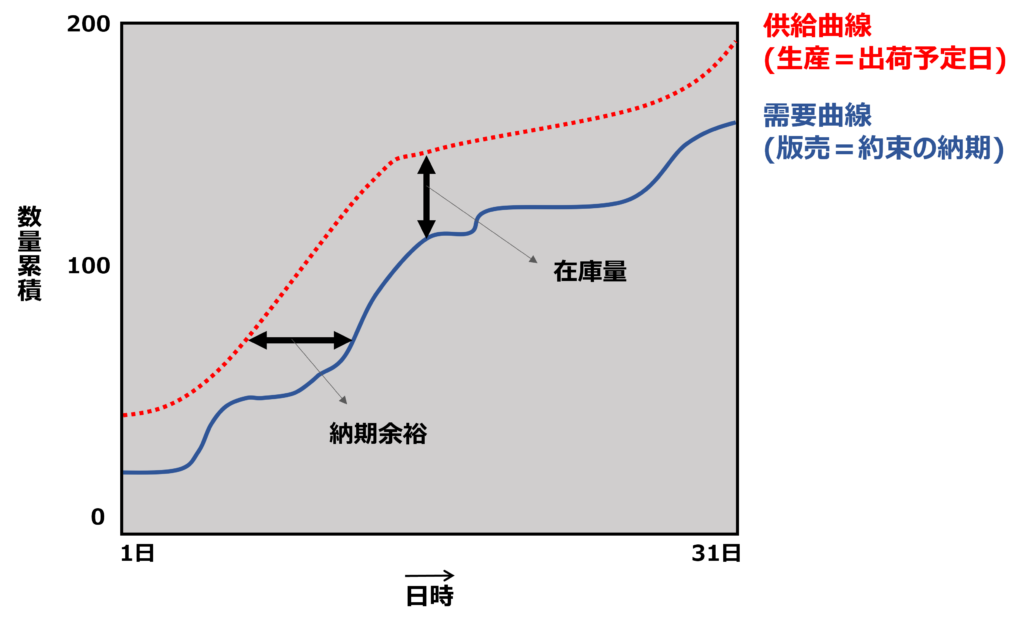
3.GD.findiで「見える」中間在庫量
在庫変動は生産計画と出荷計画、また、各工程での生産進捗の関係で決まりますそして、「在庫不足→手待ち・欠品のリスク大」、あるいは「過剰在庫→資金繰りの悪化」という関係にあります。つまり、在庫量は少なすぎでもなく多すぎでもない、最適な量で維持する必要があります。最適な在庫量としての安全在庫や適正在庫を見極めるためには、様々な状況下における在庫状況の変化を注視する必要があります。
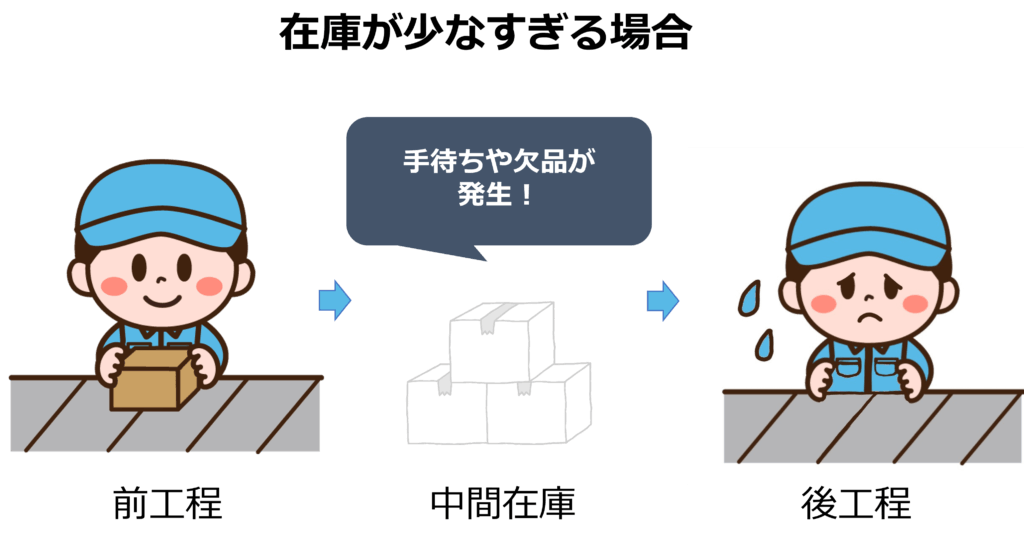
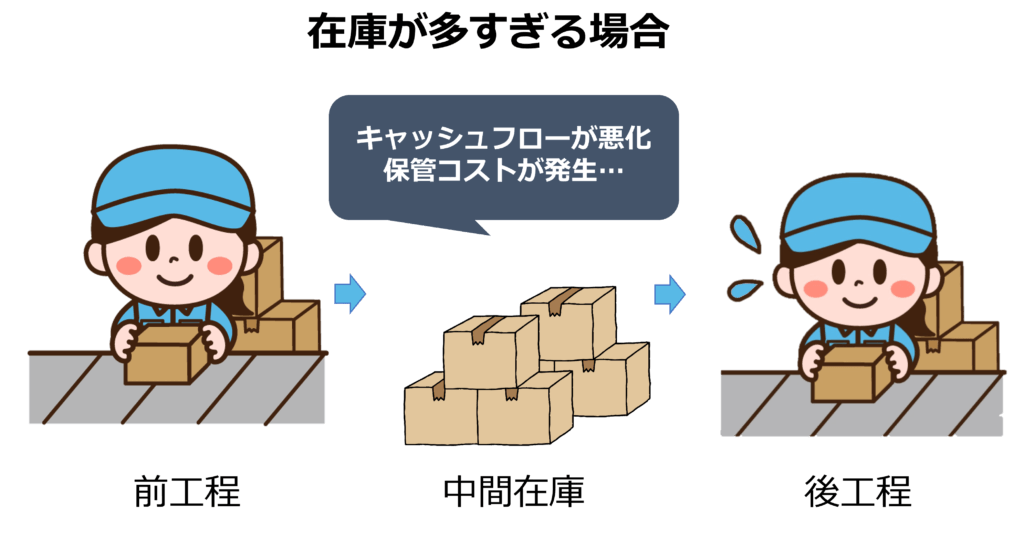
GD.findiは生産活動のみならず、生産計画をシミュレーションすることができるので、在庫状況の変化を「見える化」することができます。生産途中で生成される「中間在庫量(仕掛品)」も、その推移を調べることで在庫状況の変化を可視化することができます。
例えば、複数の生産を担っている生産ラインで、前工程⇒後工程というシンプルな図式で考えてみましょう。このとき、前工程で複数製品のバッチ生産計画が設定されている場合を仮定します。生産製品が複数ある分、在庫の積み上がりは生産計画に依存して、その予測は難しくなります。後工程での生産計画との関係で在庫変動が決まりますから、このような動的な要素はEXCELのような静的ツールで計算するのは困難です。また、生産計画通りに生産が進むわけではなく、一般的には遅れる方向で推移しますから、この変動を組み込んで在庫変動を予測する必要があります。
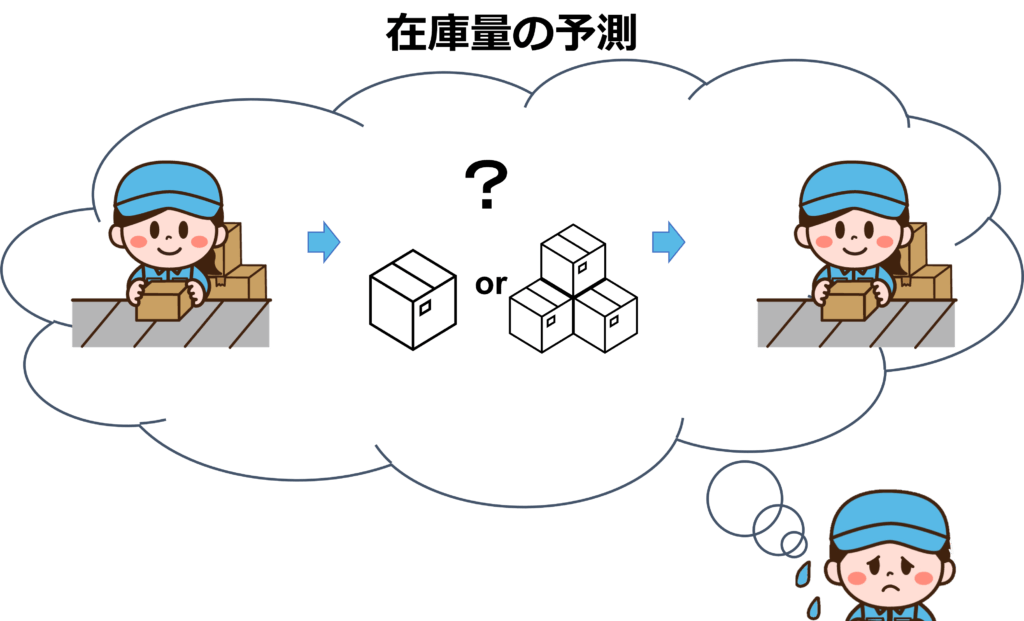
GD.findiでは、シミュレーションを実行する初期時点での各ステーションや中間在庫、バッファの「在庫」を設定することができます。ある程度の初期在庫を設定した上でシミュレーションを実行することで、前工程と後工程の稼働状況の変化による在庫量の推移を直に「観察」することができます。シミュレーション上で「観察」することで、後工程で手待ちが発生しない最低限の在庫量を見極めることができます。
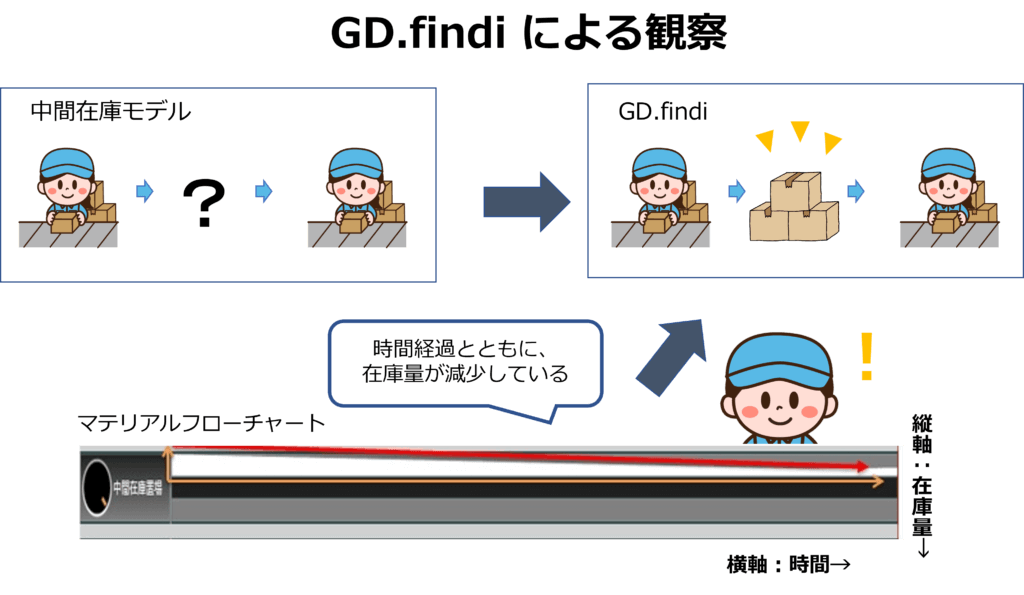
4.中間在庫量の推移の確認
下図のように前工程より後工程の処理能力が低いラインを仮定します。前工程と後工程がフルで動作させる場合には、中間在庫が欠品して後工程で手待ちが発生することになります。
このような形態に対応するためには、前工程の稼働時間を下げ、後工程の稼働時間を高める必要があります。ここでのポイントは、前工程の稼働でどの程度、中間在庫を積んでおく必要があるかを求めておく、ということです。
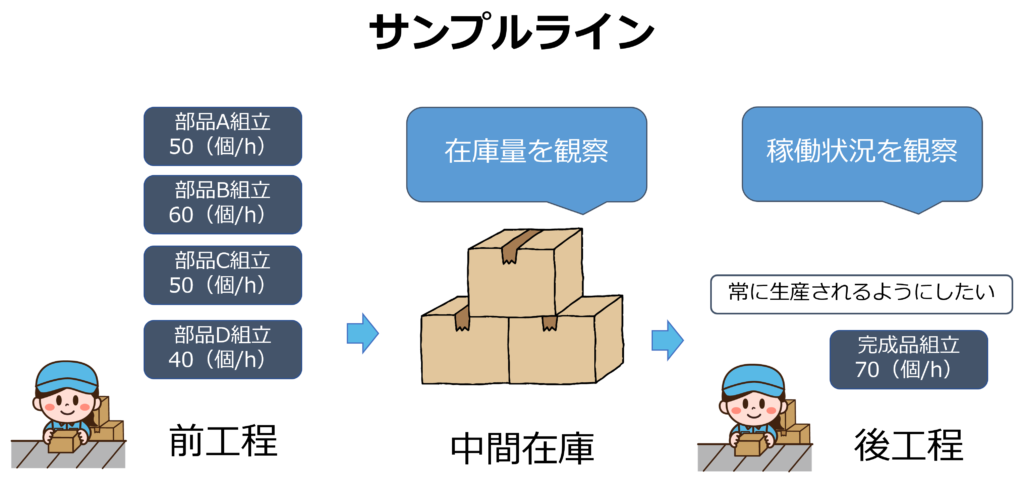
このようなケースには、GD.findiに搭載された「出力ログファイル」機能を用いることで、シミュレーション結果をデータとして出力して在庫量の変動を「観察」することができます。
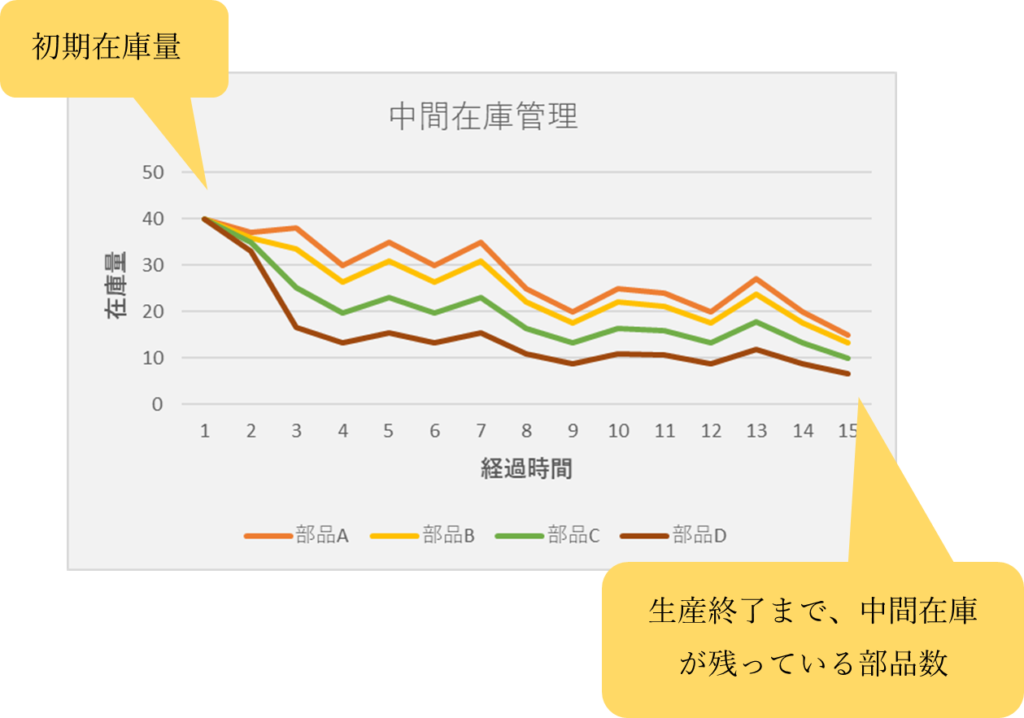
例えば上のグラフのように在庫数の推移を部品別に可視化し、中間在庫の推移量を確認すると、生産終了時の中間在庫置場に各部品が残っていることが分かります。
部品Aの初期在庫を40⇒30個に減らしてみた場合もシミュレーションしてみましょう。
中間在庫の推移グラフ(グラフ2)を見ると、生産終了時もまだ部品 Aが残っていることが分かります。
部品Aの初期在庫を40⇒30個に減らした場合(グラフ3)、生産を終えるまでに部品が不足してしまいました。
以上の「観察」により、欠品と在庫過剰を回避しつつ、生産終了時までに手待ちを発生させないために必要な部品Aの在庫量は21 ~29 個だということがわかります。
このようなシミュレーションによる「観察」を全部品の在庫数に注目して実施すれば、後工程の手待ちを回避し、生産終了時に部品を残留させずに済む個数も特定することができます。
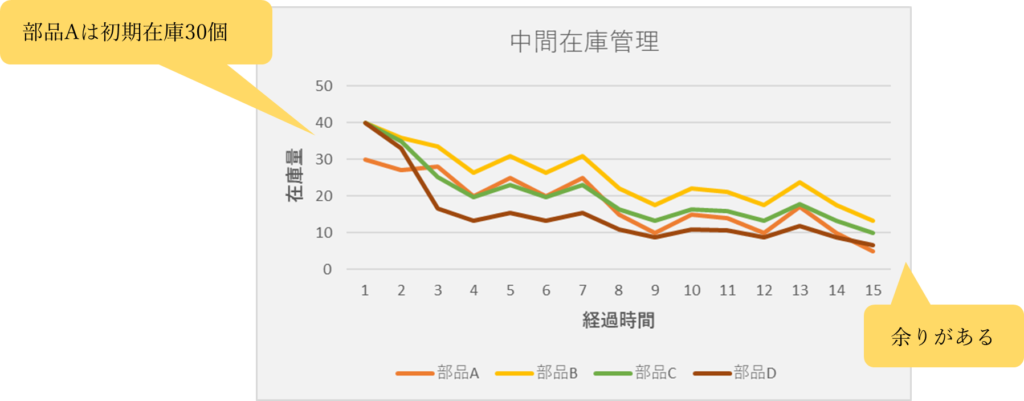
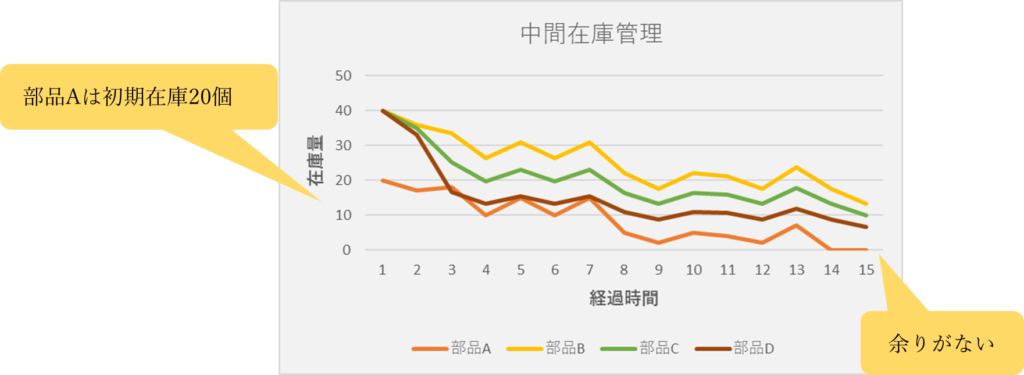
このように、GD.findiの「初期在庫」・「各工程の生産計画」・「出力ログファイル」を活用して中間在庫量の推移を「観察」することができます。さらにGD.findiでは、生産不具合による部品ロスの影響等も反映させることができます。
ご興味のある方は、ぜひお問い合わせください。