- GD.findiが解決できる課題
- 製品紹介生産活動の現場とサイバー空間をつなぐ 生産シミュレーション
GD.find MS
Modeling & Simulation
ライン設計を強力に支援する完全ノーコード生産シミュレータ - よくあるご質問
- 事例
- ウェビナー
- お役立ち情報
Best For You
搬送台車、搬送作業者の振る舞い
(搬送エージェントによる、搬送システムの設計)
- Home
- /
- Best for You
- /
- 搬送台車、搬送作業者の振る舞い
1.搬送設計から行う課題
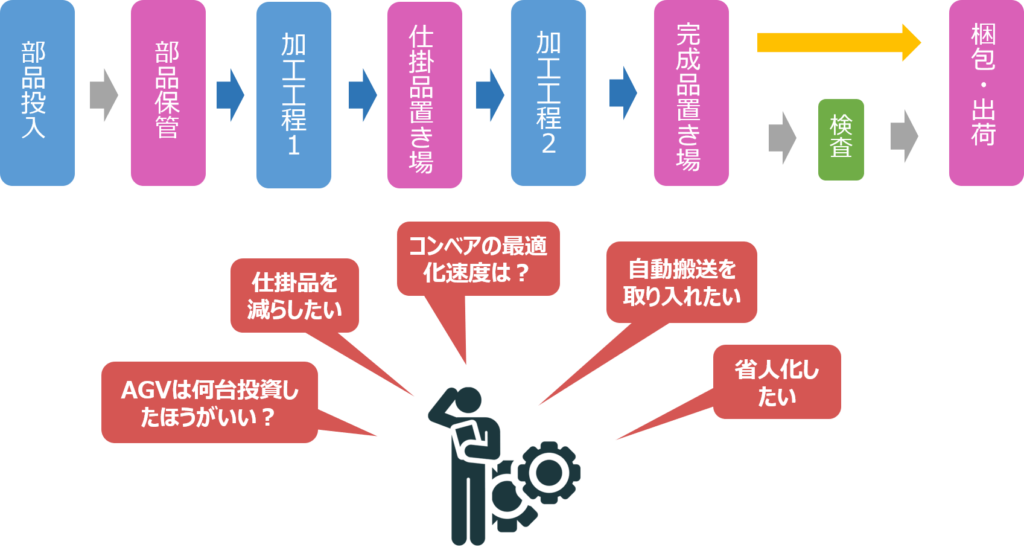
生産ラインや工場の変革、つまり、生産システムの進化は要素技術の革新によってもたらされます。皆様もご存じの通り、
・センサ技術(デバイスのみならず、画像解析や自動判別技術等)
・マテハン技術(ロボット技術の進化による自動化)
・搬送技術(自律動作するAGV等)
などを生産現場に導入されて、生産革新を進めていらっしゃる生産現場も多いことと思いますが、ここでは特に、搬送技術について取り上げてみたいと思います。
搬送技術の革新は生産システムの進化に大きな影響を与えます。従来、搬送に係る作業や時間は「付随作業」として非付加価値時間に位置づけられており、如何にこの時間を短縮するかに挑戦し、カイゼン活動が進められてきました。
そこでは、モノの流れの整流化、部品投入から出荷までの単一方向流し、レイアウトカイゼン、さらには、設備の内段取り自動化等による付随作業時間の削減を続けられていました。つまりこれらの考え方のベースは、一連の作業プロセスとモノの流れを整合させて非付加価値時間を減らそうとするものでした。
ここで、搬送技術の進歩や低コスト化が進みつつある今日、AGV等の自動搬送機器を柔軟に活用して搬送効率を高めたり、搬送作業者を減らしたりする等の方式の普及が始まっています。設備投資として自動搬送機器を導入しオペレーション・コストである作業者を減らすことや、高価な複合マシンを廃して安価な単機能マシンの組み合わせでリードタイム短縮や製造コストを抑える方式は、今後の潮流になっていくでしょう。
さて、ここでの課題は、生産プロセスとモノの流れがよどみなく同期して進むような生産システムが設計できるか、ということです。
つまり、必要なマテリアルが、必要な場所に、必要なタイミングで整備されていることが不可欠になります。また工場生産を遅らせない為に、不測の事態の際にも迅速に対応する必要があります。
ところが、このような点について十分なシステム設計を行うのは難しい…ということも少なくありません。その理由は、スタティック(静的)な生産システムの設計とダイナミック(動的)な搬送システムの設計を総合的な観点で良好に体系化設計することが難しいからです。例えば、AGVの導入においては、AGV専用のシミュレータによって巡回ルートの検証やスループットの評価等は可能であるものの、生産プロセスにおける作業の流れとモノの流れを総合して評価することは困難です。また、AGVが高機能化して自律性が高まれば高まるほど、生産ライン側との乖離が大きくなります。皆様の生産ラインにおいて最適なAGVの台数を見出すことは容易ではなく、結果、余剰なAGVを導入してしまうことに繋がってしまいます。
また、定時・非定量、非定時・定量といった基本的な搬送であっても、どの程度のAGV台数で、どのくらいの時間間隔で、さらには搬送上限の設定をどうやって決めるのか等、ご苦労された経験は多くの方がお持ちであると思います。
つまり、今日では、搬送システムの能力を最大化させるために、生産ラインと搬送システムを統合して設計・評価することが重要になり、今後ますます必要になるといえます。
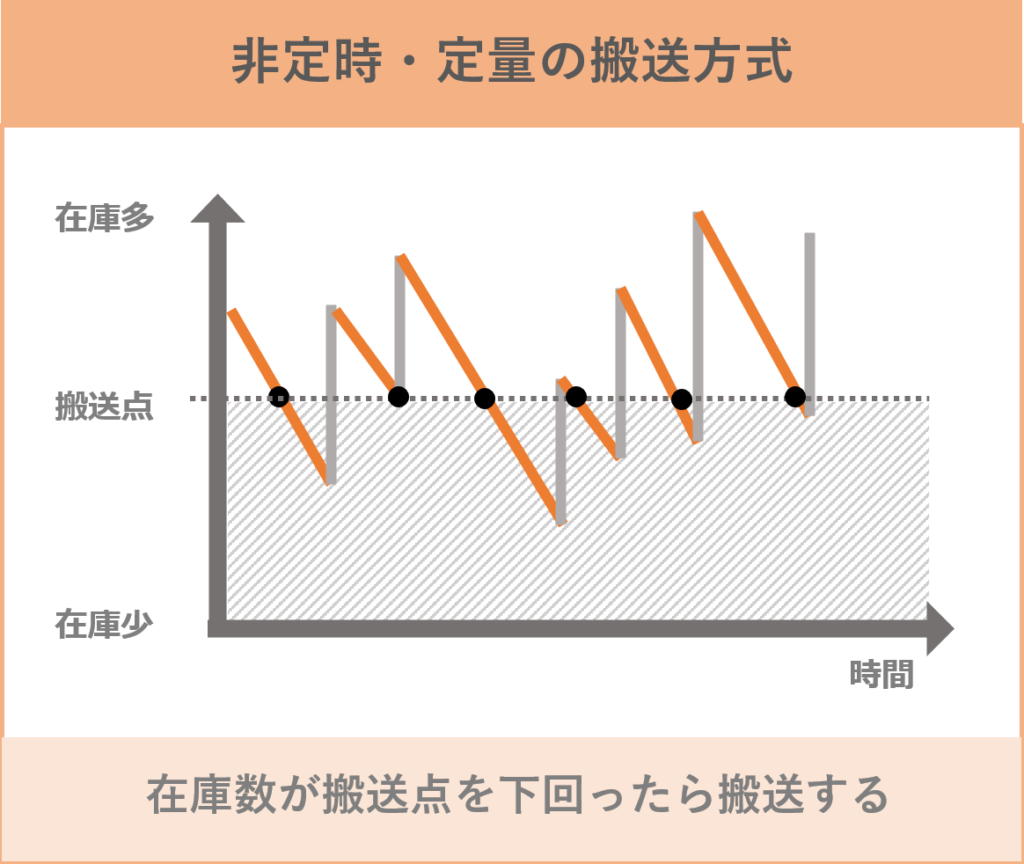
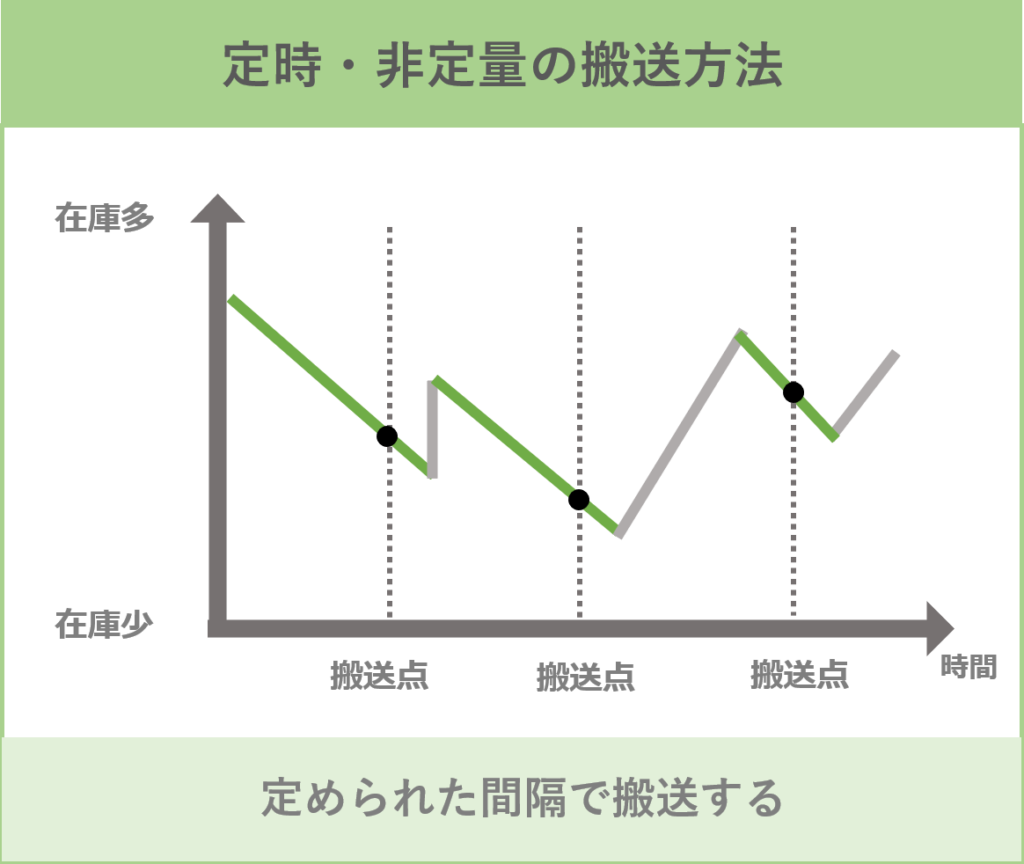
2.搬送システム設計に対するアプローチ (ノーコードで設計できる搬送システム)
搬送システム、特に自律的に動作するAGV等では、静的な生産システム設計の方式では対応が困難です。つまり、標準作業組み合わせ表やチャート図のような、決まった流れで評価することはできません。なぜならば、自律動作する搬送システムは自らのロジックに従って、時々の状況に合わせて振る舞い、動作が変わるからです。
これに対応するためには、自律動作する搬送システムを模擬するオブジェクトをバーチャル空間に配置するとともに、生産プロセスと連携させて、その振る舞いを総合的に評価するアプローチが有効です。
GD.findiの生産シミュレーションでは、運搬が可能な通路を定義し、生産ラインのシミュレーションと連動させることで、搬送システムが所定の目的通りに動作するかを検証し、搬送システムのスペックを決定することができます。
例えば、現場のフロア・デザインに合わせて、搬送用の通路を描き、その通路構成の設計の違いでどのような差異が出るのかを検証します。GD.findi ではこれらの搬送にまつわる設定はノーコード(画面上の操作のみ)で行うことができます。
下図のように、異なったレイアウトに対する搬送通路の設計がどのように影響するかを確認することができ、搬送作業の設計に大変有効です。
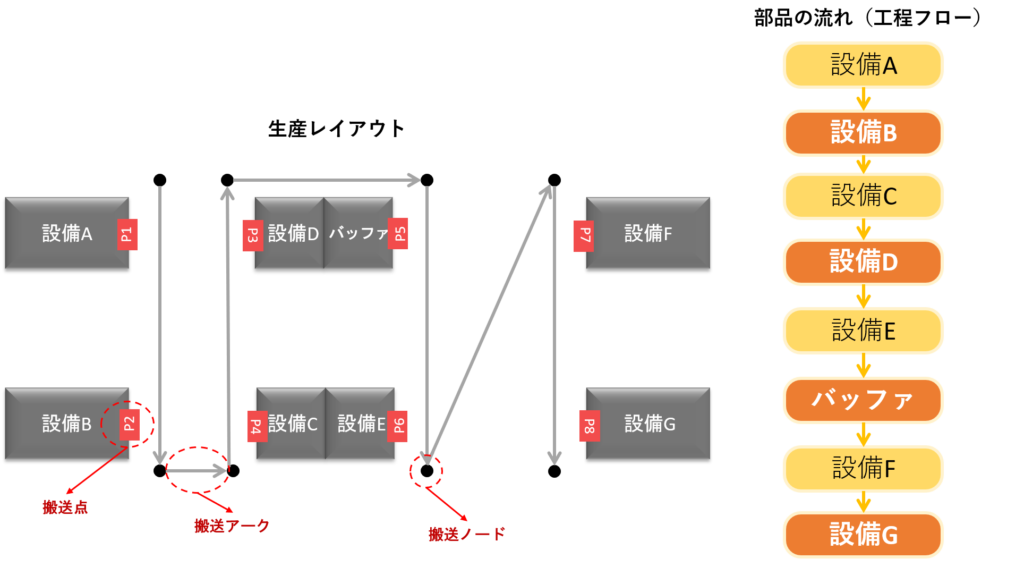

3.搬送システムのバーチャルでの記述(表現)方式
ここまで議論しましたように、搬送は動的(ダイナミック)な振る舞いをしますので、生産システム上その設計については注意を要します。つまり、細かい振る舞いばかりに気をとられていては大きなものの流れをとらえることができず、大きな振る舞いだけを注目してしまうと搬送設備仕様の細かな影響を検証できません。
そのため設計方式としては、大きなものから捉えていき、段階的に絞り込みながら詳細設計まで落とし込む、という考え方が有効です。
ここでの基本的な考え方は、「搬送システムは生産ステーション(生産を行う設備、場所のこと)間の物流を担うものであるが、搬送自体は制約として作用する」という点に留意しています。つまり、搬送自体は付加価値を生み出さない活動で、付加価値を生み出す生産ステーションの活動の間を、如何にロスを少なく繋ぐことができるか、という視点に立ち、良い生産システムを設計するということが重要になります。
この考え方に基づくと、以下のようなステップでGD.findiを活用していただくことで効率的、すなわち、ラピッドに搬送システムの設計を完成させることができます。
1 搬送システムを明示的に定義しないで生産システムを設計する
GD.findiでは、搬送システムを明示的に設定しない状態でも、生産ステーションから次の生産を受け持つ生産ステーションにワークを流すことができます。この場合、搬送時間はゼロ、もしくは固定値を設定することができます。これにより、「制約条件としての搬送」を排除した状態で生産システムの持つ最大の能力を確認し、見出すことができます。(GIF1参照、赤い丸が部品を四角のブロックがステーション:設備を示しています)
2 搬送システムを明示的に定義して生産システムを設計する
生産ステーション間に「エージェント」を設定することにより、そのエージェントの機能によって搬送の振る舞いが制御され、搬送システムとして動作します。ここで、GD.findiでは様々なエージェントが準備されているので、どのような搬送形式が適しているのかをエージェントを切り替えながら検証を進めます。(GIF2参照、作業者エージェントが搬送作業を行っています)
3 搬送システムが動作する通路やスペックを設定して生産システムを設計する
さらに、エージェントの振る舞いについて、より詳しく条件を設定することも可能です。
・通路の設定
レイアウト上で搬送エージェントが移動可能な通路を設定。エージェントは通路を自律的に選択しながら最短距離で移動。
・搬送エージェントのパラメータ設定
台数、移動速度、受け持ち範囲、荷積みステーション、荷下ろしステーションの設定等。
このようなステップを通じて、目的とする搬送システムの概念設計、また、要求設計を効率的、効果的に実施することができます。
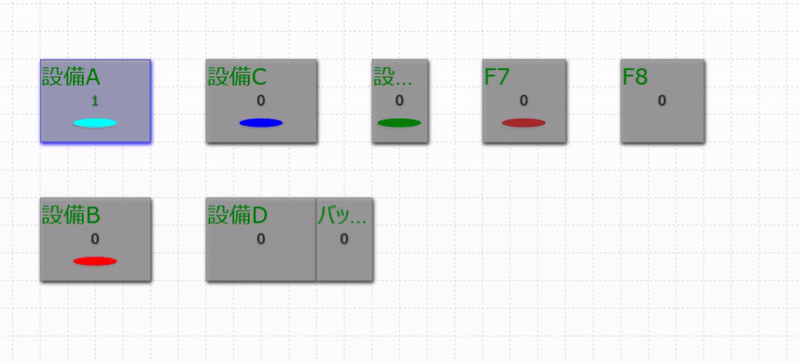
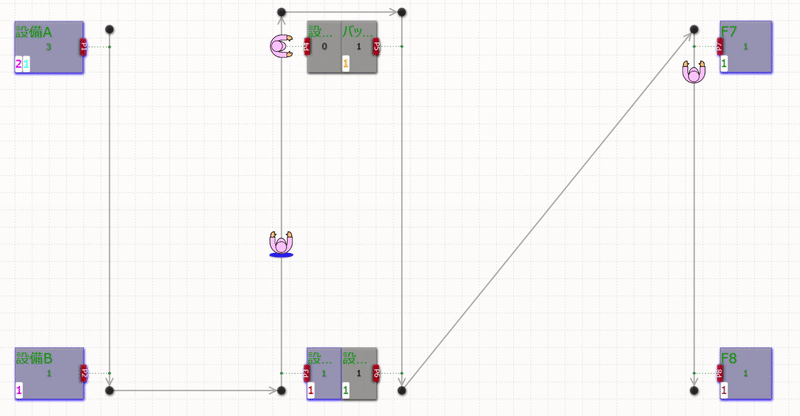
4.GD.findi が提供するエージェント・ライブラリ
さて、このような搬送システムを設計する場合に「エージェント」を活用することが有効であることを述べました。GD.findiでは、牽引車、通路指定作業者、AGV_scheduled等の異なる機能を持つ搬送方式を準備しており、GD.findiの「エージェント・ライブラリ」としてご提供しています。生産システムのデザインに応じて、生産ラインに適したエージェントを選択することができます。
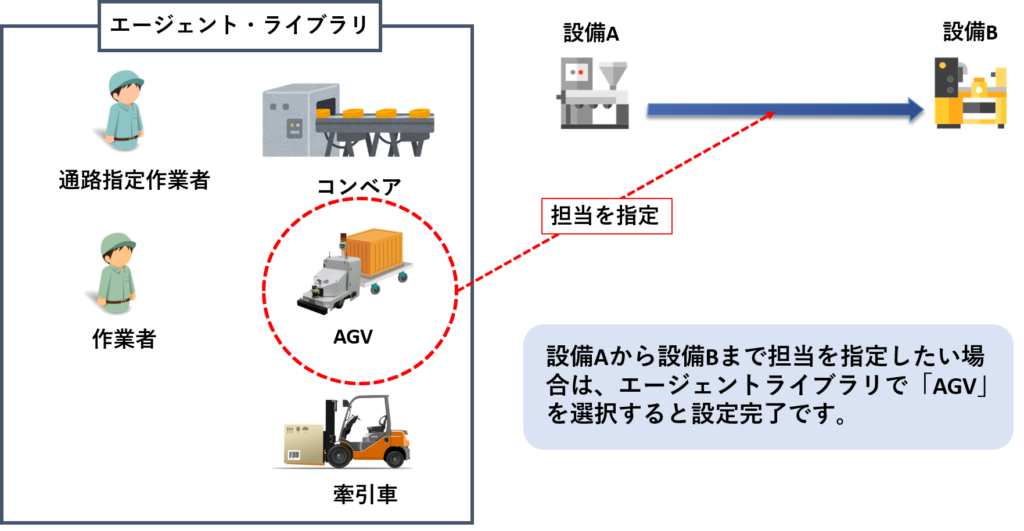
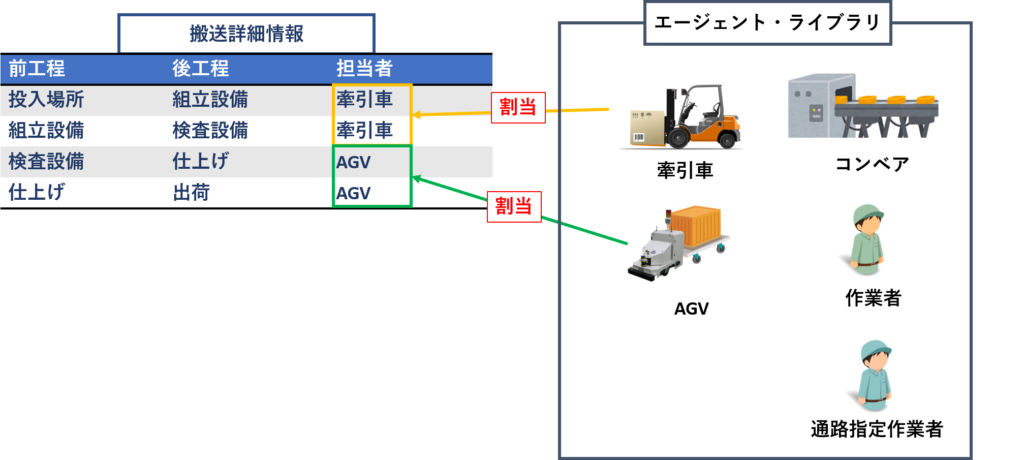
5.搬送システム設計の評価(マテリアルフローチャート)
次に、設計された搬送システムの良し悪しを評価する方法について、少し、ご紹介します。GD.findi の特長のひとつに、「マテリアルフローチャート」によるデータ分析技術があります。マテリアルフローチャートとは、生産レンダリング(生産シミュレーション)の実行後、進度グラフやアセット(搬送作業者等)フローをグラフィカルに表示する機能です。ステーションや搬送作業の稼働状態はガントチャートで、ステーション内やステーション間の移動時間をマウスオンした際のポップアップ表示で、それぞれ表示されます。
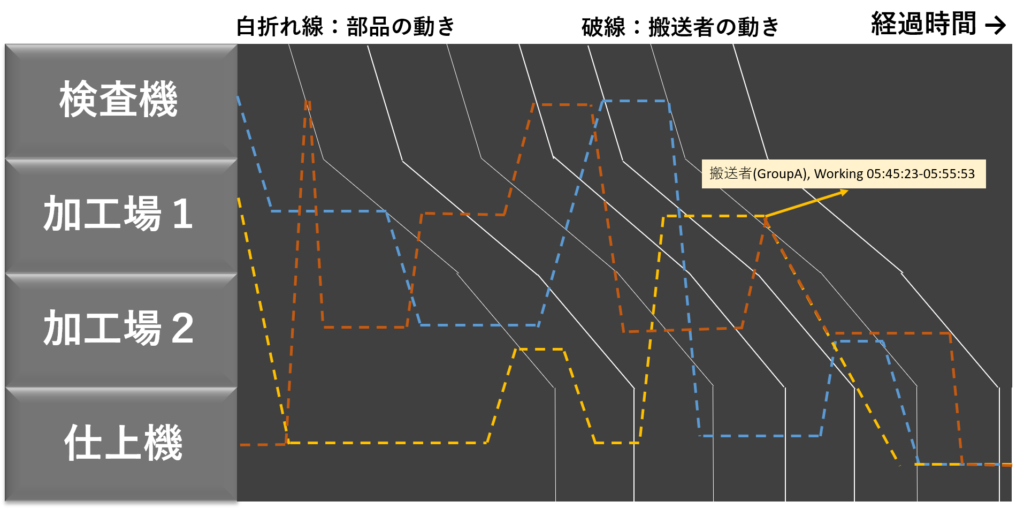
6.活用例:エージェントを活用した最適な搬送アセットの決定
複数の搬送作業を持つ生産システムにおける最適な搬送デバイス数を決定することは容易ではありません。AGVの数が少ない場合、設備側で作業者を待つことにより作業が停止し、結果、工程間在庫が増えてしまう等のロスが発生することになります。GD.findi ではこのような状態に対して、シミュレーションで最小限の搬送台数を求めることができます。例えば、ある生産ラインの目標生産数64個、搬送者稼働率85%以下を達成したい場合は、搬送者数を1~5名それぞれのパターンでシミュレーションを実行し、その結果を比較分析します。(表1参照)

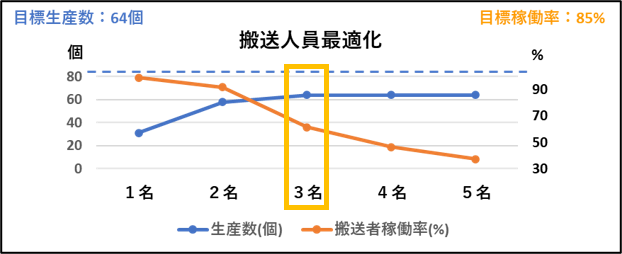
表のデータをグラフにすると、生産ラインに最適な搬送者数がわかります。
この例では、生産目標を達成している搬送デバイス数は、3台以上となります。一方、搬送デバイスは3台より増やしても生産数は増えないことがわかります。つまり、搬送デバイスの数は4台以上に増やしても無駄な投資であることが言えます。
つまり、目標生産数を達成して、最小の投資となる搬送デバイス数は「3台」であるといえます。
このように、搬送エージェントを活用することで、複雑な振る舞いの搬送作業の最適化設計を行うことができます。
ここまでは搬送システム設計についての考え方をご説明しました。尚、このテーマで具体的な課題をどのように解決していくかを、「GD.findi レシピ(操作事例集)」としてご用意しております。
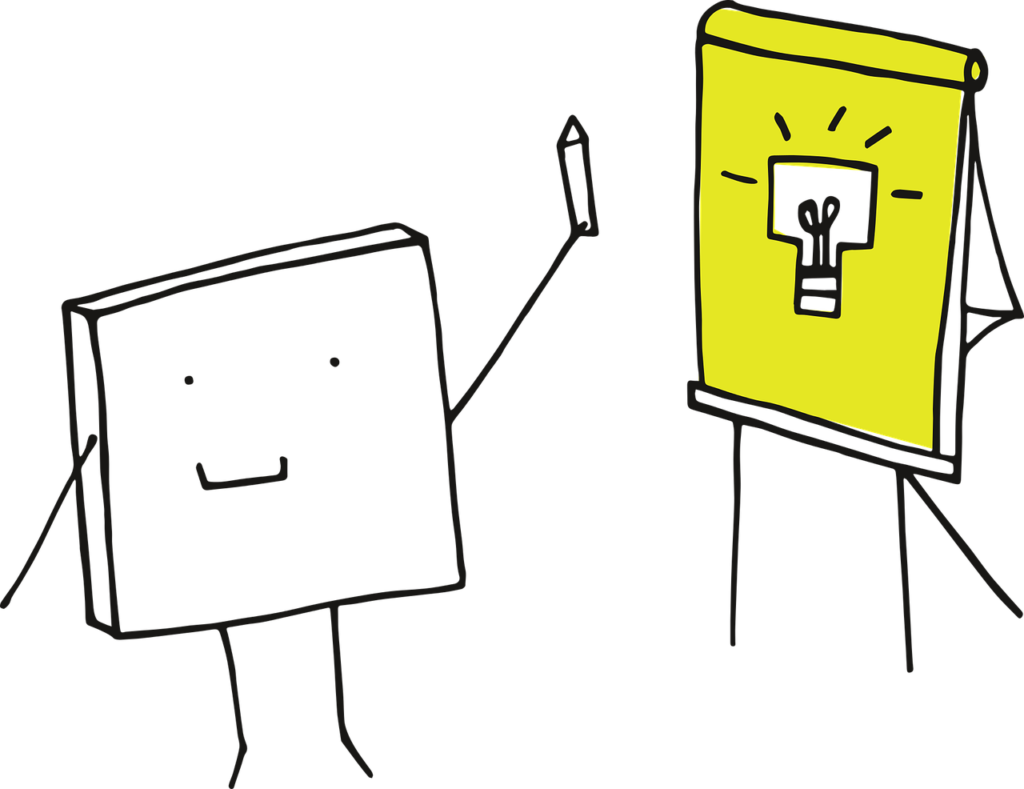