- GD.findiが解決できる課題
- 製品紹介生産活動の現場とサイバー空間をつなぐ 生産シミュレーション
GD.find MS
Modeling & Simulation
ライン設計を強力に支援する完全ノーコード生産シミュレータ - よくあるご質問
- 事例
- ウェビナー
- お役立ち情報
事例:アセンブリメーカー P社 様
シミュレーションで従来は検証できなかった範囲の改善も可能に。
設備配置・プロセスの最適化で、生産性向上を実現
業種:アセンブリー 課題:改善効果を数値化できず、改善の提案・実行に移すことができなかった
導入前の課題 |
|
導入後の効果 |
|
GD.findi MS を選んだ理由 |
|
シミュレーションで従来は検証できなかった範囲の改善も可能に。
設備配置・プロセスの最適化で、生産性向上を実現
GD.findi MS 導入に至った背景
アセンブリメーカーP社では、設備と部品置き場が限られたスペースに置かれており、配置が適当か疑問視されていた。しかし、レイアウト変更等の改善効果を数値として示すことができず、改善計画の提案書作成ができないままでいた。
こうした課題に対して、バーチャル上で現行と改善後の生産システムをそれぞれ数値化して比較することのできるGD.findi MS が採用された。
GD.findi MS 導入で得られたメリット
1. 従来は改善の対象にならなかった範囲まで、検証・改善が可能に
レイアウト変更等の改善アイディアを GD.findi MS で検証することにより、従来はリスクが課題で、改善の対象にならなかった案も検証し改善できるようになった。
2. 設備配置、プロセス組み合わせの最適化を行い生産性向上を実現
GD.findi MS のシミュレーション結果から、複数の部品棚の配置替えやプロセスの組み合わせを最適化することで、生産性が向上することが判明。数値的に改善効果を示すことができるため、説得力のある提案資料の作成、改善の実行が可能になった。
GD.findi MS ならではのポイント
複数パターンのシミュレーションをスピーディに実現可能
GD.findi MS は高い編集性・再利用性を持っているため、少ない工数で複数パターンのシミュレーションを行うことも可能。現場では試すことが難しい設備の配置換えも、GD.findi MS ならGUI上でモデルを編集し、配置パターンの評価をすることができる。
お客様の声
GD.findi MSを検討している方へのメッセージ
GD.findi MS を活用し、改善案を仮想実験で数値化することにより、リスクのない環境で、改善の閾値を大幅に低くすることができます。
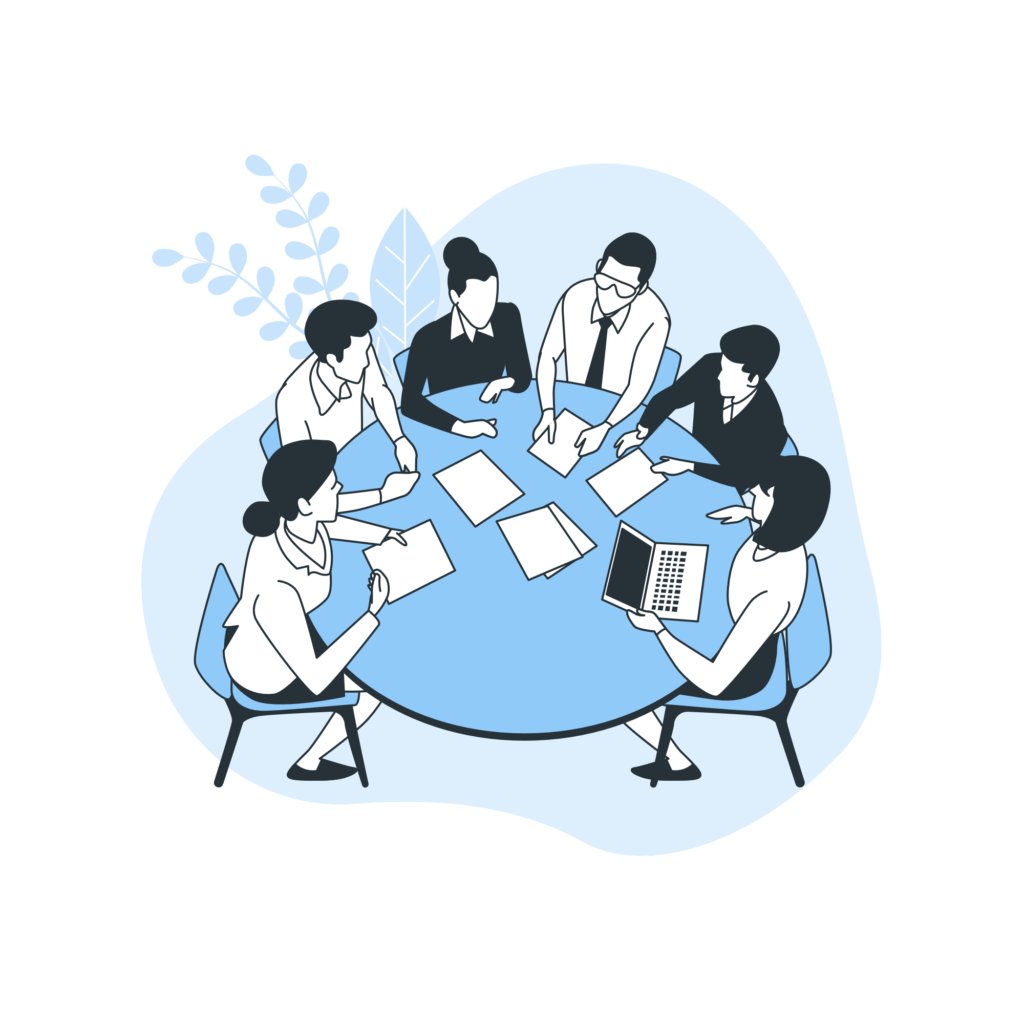
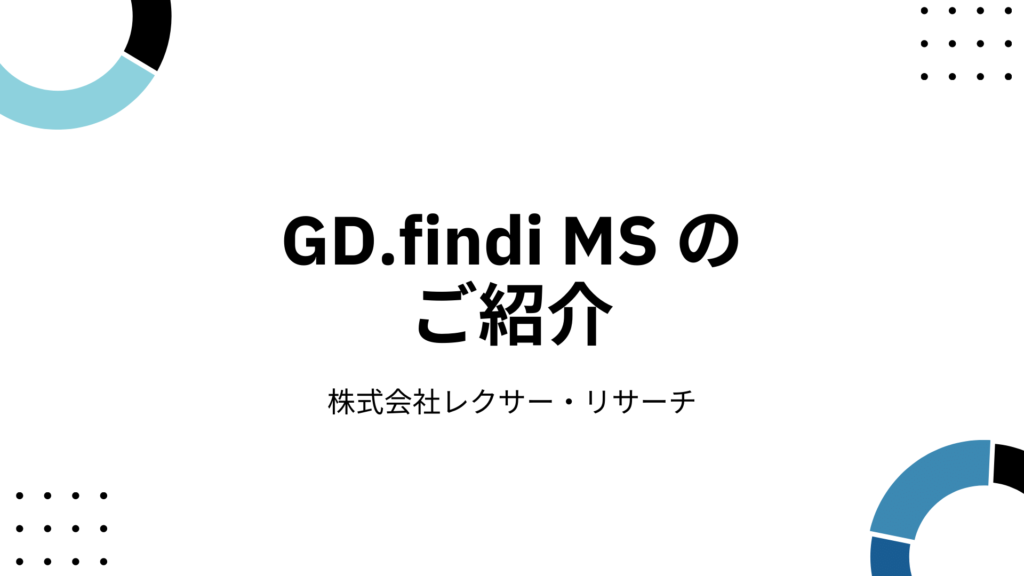