- GD.findiが解決できる課題
- 製品紹介生産活動の現場とサイバー空間をつなぐ 生産シミュレーション
GD.find MS
Modeling & Simulation
ライン設計を強力に支援する完全ノーコード生産シミュレータ - よくあるご質問
- 事例
- ウェビナー
- お役立ち情報
事例:パナソニック株式会社
シミュレータを活用してAGV導入への提案を具現化
パナソニック株式会社 様
業種:総合家電の生産・販売など 従業員数:259,385名 課題:最適なAGV台数の検討
導入前の課題 |
|
導入後の効果 |
|
GD.findi MS を選んだ理由 |
|
- インタビュー動画
GD.findi MS の感想や導入効果についてコメントをいただきました。
山村様・下野様(5分12秒)
槇原様(6分30秒)
サイバーフィジカルシステムを目指しGD.findiの導入を推進するパナソニック
パナソニックのモノづくりの現場で大きな変化が起きている。生産シミュレータを活用することで、スピードとクオリティを革新的に向上させる取り組みが進められているのだ。電池事業では工場ラインに無人搬送車、AGVを提案するために生産シミュレータ「GD.findi」を活用。従来の10分の1の時間で実装計画を策定して各工場に提案し、導入から1年で4工場10ケースの案件をとりまとめるという成果を上げている。
条件の異なる動的な検証に威力を発揮するGD.findi
パナソニック全社でのスマートファクトリーの推進役を担うのが、マニュファクチャリングイノベーション本部である。1963年に発足した生産技術研究所を母体とし、独自の生産設備の開発など、生産技術を核に事業拡大に貢献して来た。現在では製造現場のデジタル化にも取り組んでいる。 同本部の次世代拠点プロジェクト主幹技師の槇原正氏は「グローバルに300弱の工場がありますが、事業部密着型で小規模なものが多く、非効率な面もあります。調達、オペレーション、サプライチェーンをITでワンオペレーション的な仕組みに変えることで、サイバーフィジカルシステムの構築を目指していきます」と話す。
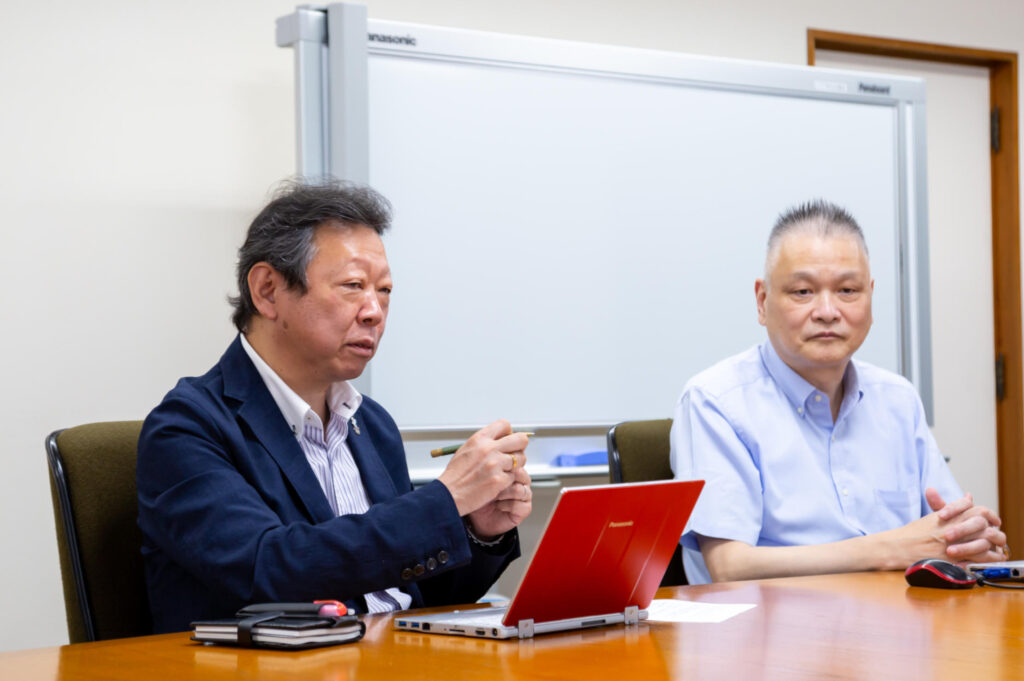
同社では以前から製造現場をデジタル化するために、生産プロセスの分野でシミュレータを導入してきた。しかし、生産プロセスのシミュレータは定着しなかった。「買っては使わなくなることの繰り返しでした」と槇原氏は振り返る。
そんな時に出会ったのがGD.findiだった。5年前のことだ。「ブラウザ経由で利用できて、サブスクリプションモデルなので、導入しやすいと思いました。また、プログラミングレスのGUIベースでモデルが作れるので、専門家ではない現場の担当者でも使えると感じました」と槇原氏は第一印象を語る。
その後、ユーザーによってカスタマイズが必要な製品の生産ラインをはじめ、生産量の変動に対応する工程設計の検証用など各生産工場にGD.findiを提案して来た。現在、大きな成果を上げている電池事業部門には、MI本部のシステムのクラウド活用や知見の融合などを行い、導入を加速した。
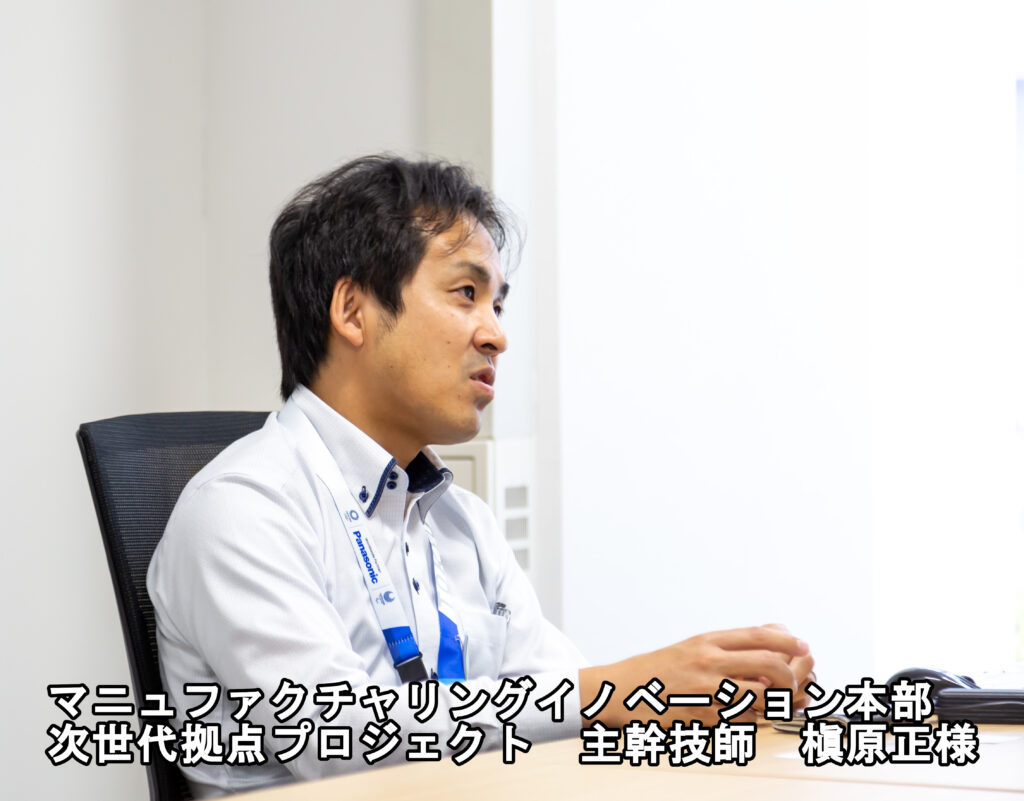
槇原氏は「GD.findiはモデルを再利用することで、迅速に精度の高いアウトプットが得られます。毎回、データや条件が異なり、揺れ動く場合の動的な検証に威力を発揮するものだと考えています。」と評価する。
槇原氏が現在、注目しているのは、海外の工場との連携にシミュレーションを活用することだ。ウィズコロナの状況下では国内のエンジニアが海外の工場に指導に行くことが難しくなる。そこでGD.findiを使って精緻なシミュレーションを行い、その結果を元に生産ラインの計画、設計などを指導していくという使い方だ。
「シミュレーションをコミュニケーションツールとして使うことで、よりロジカルな議論が行えます。GD.findiをサイバーフィジカルシステムに向けてのツールの一つとして位置付けています」と槇原氏は語る。GD.findiによってエンジニアリング力がボトムアップされ、同社の底力の強化を目指している。
シミュレータを活用して電池工場への提案を具現化
GD.findiを使って、工場でのAGVの導入を加速し、大きな成果を上げているのが電池事業部門である。長い伝統を持つ電池事業だが、生産ラインの効率化と製造コストの削減に迫られていた。そこで注目したのが無人搬送車、AGVの活用だった。 エナジーマニュファクチャリングセンター 製造力強化担当 兼 スマートファクトリー開発部部長の山村聡氏は「省人化の視点で、AGVを活用することは重要なソリューションです。但し、闇雲に導入しようとしても投資対効果が合わないことがよくおこります」と語る。
AGV導入を確実に製造力強化に結びつけるために山村氏が考えたのが、シミュレーションの導入だ。事前にシミュレーションすることで、オペレーション設計を最適化し導入後の成果を検証する際のエビデンスにもなる。そこで生産シミュレータ「GD.findi」を利用することに決めた。
山村氏は以前、槇原氏と同じマニュファクチャリングイノベーション本部に所属し、GD.findiを推進していた。「インターフェイスがわかりやすく、直感的に使えることが利点、リアルな現場に近づけるのではなく、スピーディに見通しが立てられることにメリットを感じている」と話す。
レイアウトやオペレーションが決まれば、すでに生産ラインがある既存の工場であっても、半年あればAGVを導入できる。工場への提案からオペレーション設計までのスピードアップを図ることは全体のスケジュールの短縮につながり、それだけ導入によって得られるメリットも大きくなる。
実際にGD.findiの威力はすぐに現れた。GD.findiを利用した工場に対する提案活動を担当したスマートファクトリー開発部エンジニアリング1課の下野雅己氏が2018年5月からGD.findiを使い始め、6月末には第一回の提案を行うことができた。対象としたのは新規の生産ラインにおけるAGVの最適な台数、人員数と製品置き場のパレット数の最適化設計だ。
「フロアプランを取り込んでAGVを2台から4台、作業者を1名から4名の組み合わせでシミュレーションを行い、最適なAGVの台数と作業者の人数、そして製品置き場の最大必要パレット数を算出しました。GD.findiのシミュレーション動画と算出結果のグラフを一緒に提案したので、説得力のある提案になったと思います」と下野氏は話す。
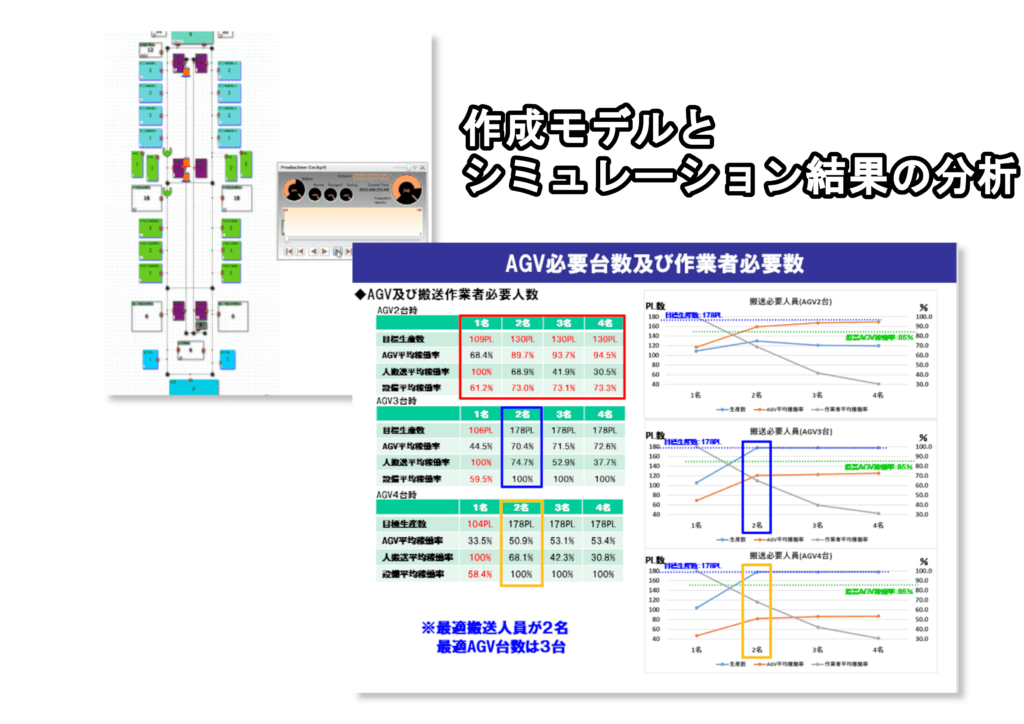
最初の提案までの時間を従来の10分の1に短縮
山村氏と下野氏はその後もGD .findiを駆使したAGV導入のための提案活動を続け、1年で4工場10ケースに対して提案してきた。現状を調査して、モデルにデータを投入。シミュレーション結果を現場とすり合わせ、必要があれば粒度(モデルの細かさ)などを変えて再度シミュレーションを行っていく。AGVの台数も1台から12台とケースは様々で、棟間の搬送にも適用した。 「最初の頃は思うようにモデルが作れないこともありましたが、すぐに慣れました。
難しいのは現場へのヒヤリングを受けてターゲットとする範囲を決めることと、どの程度の粒度でシミュレーションするのかが適切かということです。細かくし過ぎても時間ばかり取られて成果が得られないこともあります」と下野氏は利用する上でのポイントを語る。
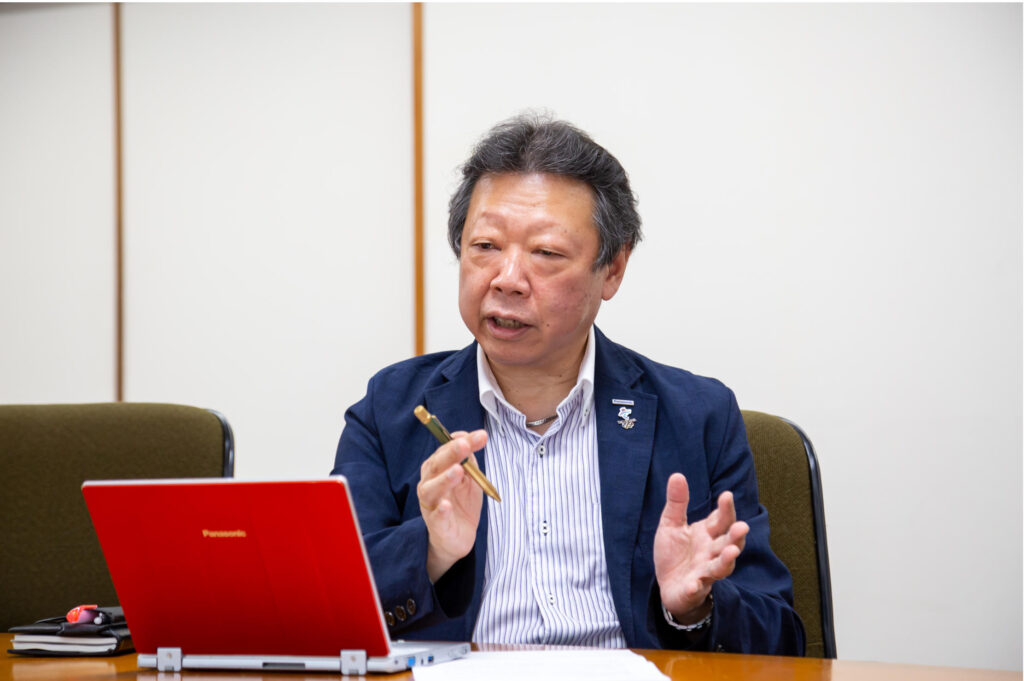
特徴的なのは、これまでの経験やノウハウを蓄積して次に活かそうという取り組みだ。モデルの作成やシミュレーションの実行方法、事例などを「搬送シミュレーション活用ガイドブック」にまとめて社内利用者の裾野を広げると同時に、これまで作成したモデルの再利用を推進している。モデルを再利用できれば提案サイクルも短くできる。
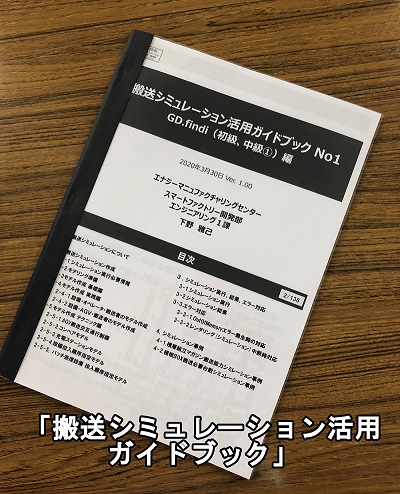
山村氏は「重要なのはスピーディに提案していくことです。シミュレーション自体は2日もかかりません。従来の10分の1です。そのお陰で、社内起案をとりまとめるのに平均して1ヶ月かかっていたのが、2週間程度に短縮されました。リアルタイムにできるのが理想ですが、3日程度まで短縮することを目指しています」と話す。
エナジーマニュファクチャリングセンター内にある「Smart Factory Lab」では、様々なタイプのAGVが導入され、AI技術を駆使したセンシングとの組み合わせなど、先進的な製造工程の研究が行われている。最終的に目指しているのは、工場におけるサイバーフィジカルシステムの構築であり、スマートファクトリーの実現だ。
「今は台数の最適化やオペレーション設計にシミュレーションを利用していますが、今後はIoTなどの実データを使って生産現場の異常感知や改善活動の検証に使っていきます。GD.findiはシミュレータですが、AIによる予兆監視などと連動できるようになると、製造業のデジタルトランスフォーメーションの実現にも貢献できるはずです」と山村氏は今後の期待を語った。
お客様プロフィール
会社名 | パナソニック株式会社 |
---|---|
事業内容 | 総合家電、AV機器等の生産、販売 |
資本金 | 2589億円 |
従業員数 | 259,385名(連結) |
特徴 | AV機器、白物家電が主力。電池などのデバイス事業、照明、住宅設備も展開。 |
本社所在地 | 大阪府門真市大字門真1006 |
ご連絡先 | 06-6908-1121(本社) |
HP | https://www.panasonic.com |
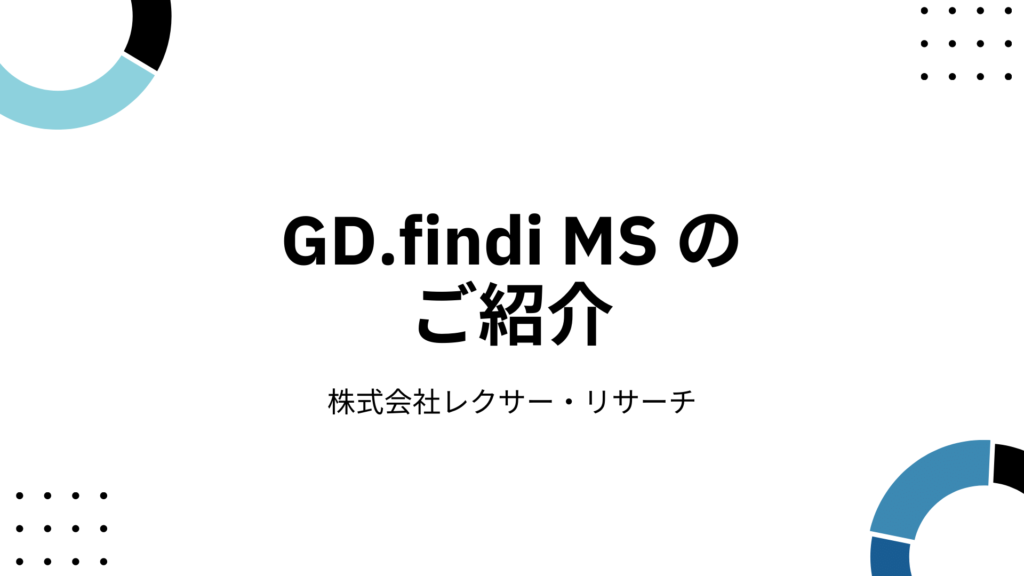