- GD.findiが解決できる課題
- 製品紹介生産活動の現場とサイバー空間をつなぐ 生産シミュレーション
GD.find MS
Modeling & Simulation
ライン設計を強力に支援する完全ノーコード生産シミュレータ - よくあるご質問
- 事例
- ウェビナー
- お役立ち情報
事例:株式会社田中製作所
サイバーフィジカルシステムで生産計画と生産現場をリアルタイムでつなぎ、多品種小ロットの生産性を15%向上
株式会社田中製作所 様
業種:金属プレス部品の製造 従業員数:130人 課題:アナログの生産管理方法が、煩雑で生産性が上がらない
導入前の課題 |
|
導入後の効果 |
|
MD-MES を選んだ理由 |
|
- インタビュー動画
MD-MES の感想や導入効果についてコメントをいただきました。
株式会社田中製作所 田中様 (17分22秒)
サイバーフィジカルシステムで生産計画と生産現場をリアルタイムでつなぎ、
多品種小ロットの生産性を15%向上させた田中製作所
金属プレス金型の設計製作、金属プレス部品を製造する株式会社田中製作所では、金型による多品種小ロットのプレス生産を行う単発ラインの生産性の低さが課題となっていた。生産する製品が変わるたびに金型の段替えや調整が必要となり、現場にも大きな負担がかかっていた。しかし、生産シミュレータ「GD.findi」を導入して、最適な製造計画を立案し、作業指示や作業実績をリアルタイムに管理することで、生産性を15%向上させることができた。
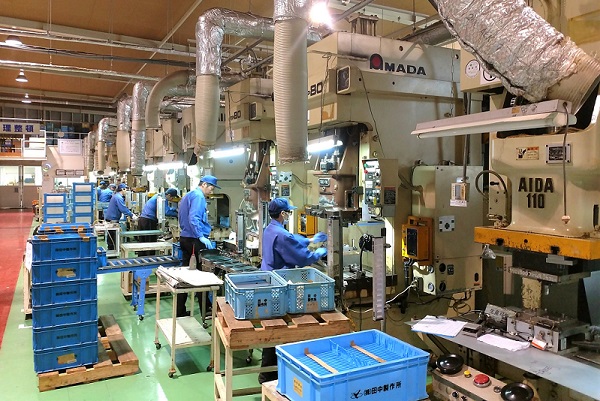
生産性向上を阻んでいたアナログでの生産管理
田中製作所は創業55年、社員数130名の金属プレス部品の製造メーカーであり、電気、自動車などのプレス部品を製造している。特に独自の金型技術を持ち、精密板金の設計製作から精密部品のプレス加工、アセンブリ加工、委託加工など、多品種小ロット生産から量産までを手がけている。
同社にとっての課題は、多品種小ロットの単発ラインの生産性の低さだった。そこでは一台一台、単発で金型部品の製造が行われていたが、製造する部品によって金型を入れ替える段替えや精度を出す調整作業が必要になり、さらに特急進行の注文への対応が求められる中で、どう生産性を高めるのかが大きな課題になっていた。
同社代表取締役社長の田中道男氏は「小ロットで作る製品は約500種、個数も一個から3千個と幅があり、生産指示が煩雑を極めていました。ライン長が毎朝ホワイトボードにその日の生産計画を書き出すのですが、納期変更や特急品があって書き換えが繰り返し行われ、夕方になったら何が書いてあるのかわからないくらいに混乱していました」と語る。
こうした昔ながらの進め方は、作業現場の混乱を招くだけではなかった。作業順番をどう入れ替えるのか、どんな段取りで進めると良いのか、といった現場の制約条件のノウハウが熟練工であるライン長の頭の中にあって、属人化されてしまっていたのだ。また、ライン長の技術や知識の継承も進んでいなかった。
「工場全体で見ても、大きな生産計画と日々の生産計画や生産指示がなかなかつながらずに、コストやリードタイムの問題も発生していました。そこで15年ほど前にカンバン方式を導入してみたのですが、特急品への対応がうまくいかないといった問題が発生しました。カンバン方式は当社のような生産形態には合わなかったようです」(田中氏)。
課題解決に必要とされた製造を熟知したパートナー
生産計画と生産現場が齟齬をきたしていた中で田中氏が考えたのは「生産管理と製造をタイムリーに連携させる」ことだった。しかし、情報システムに精通している人材は社内にはいない。同社は生産現場の問題を理解してくれるデジタル技術を持つパートナーを探し始めた。そこで思いついたのが生産シミュレータ「GD.findi」提供するレクサー・リサーチだった。
「以前、3D作業マニュアルを開発した時に、GD.findiの前身であるGP4を使ったことがありました。お客様に動画で見せることができて好評でした。その時に生産現場に精通している会社だとわかりました。製造業や生産ラインを熟知している会社が作ったソフトなら合うはずだと考えたのです」と田中氏は振り返る。 同社が目指したのは、データで生産計画と生産現場をリアルタイムに管理する「稼働管理システム」の構築である。
具体的にはGD.findiの作業管理システム「GD.findi MD-MES」によって、担当者のスマホに作業指示を送り、スマホを使って作業終了報告のデータを収集。超並列シミュレーションの「GD.findi Predictive Minig」を活用して最適な作業計画をリアルタイムに立案し、作業員のスマホに指示を送り、全体の進捗状況を大型ディスプレイに表示するというものだ。
同社では、まず単発ラインの1つに導入し、検証を開始した。2017年9月のことだ。「現場でスマホを使うことに対して、当初年配の作業員は抵抗感を持っていましたが、“家に帰ったら使っているでしょう”と説得しました。それ以外は特に問題なくスムーズに導入できました」と田中氏は話す。
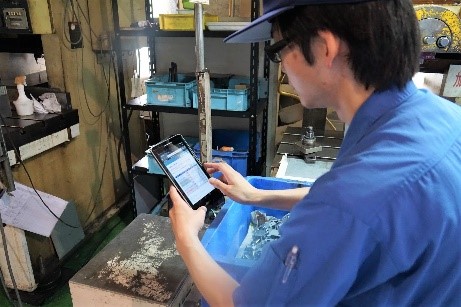
狙い通り現場に情報と生産計画の連携ができることを確認した同社は、その後、単発ライン12台に同様の仕組みを導入し、1年くらいの時間をかけて前工程と後工程にも適用範囲を広げていった。
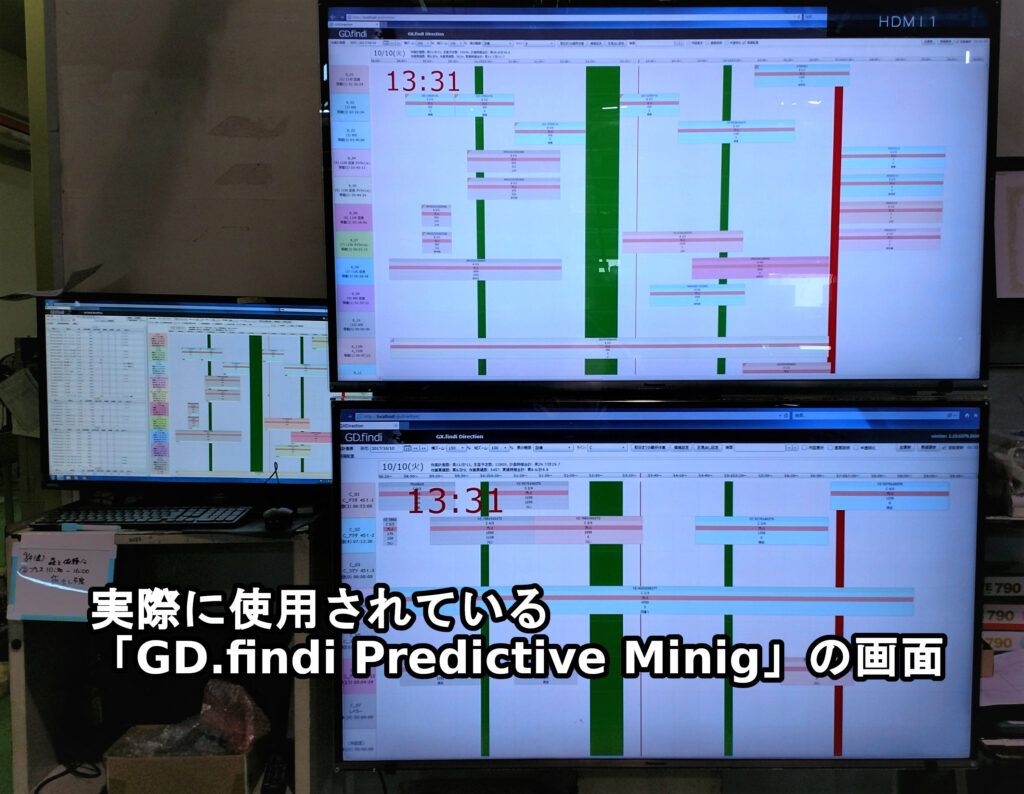
システム化で業務が変わり15%の生産性向上を実現
この稼働管理システムによって同社の現場の業務の流れは大きく変わった。従来は1日の作業が終了して作業日報をまとめてからしか実績数字わからなかったために、残業して翌日の生産計画を立案していた。それがリアルタイムに処理されることで、当たり前になっていた残業がほとんどなくなった。さらに、作業しながら実績データが収集されているので、作業日報自体も不要になった。
実際に同社の生産効率は大幅に向上している。「同じ出来高を残業することなく達成できるようになっています。そこから考えると、生産性は15%程度向上していることがわかります」と田中氏は評価する。
また作業の変更指示がリアルタイムに送られてくることで、作業ミスも削減された。田中氏は「これまでは作業をするプレス機に取り付けられない金型を間違って持ってきてしまうようなことが起きていました。今は事前にシステムから警告が出ますから、そういうミスは全くなくなりました」と話す。
間接作業やミスが削減されたことで生産能力に余裕も生じる。その状況を明確に把握できることは、特急品への対応という面でも大きなメリットをもたらしている。これまで現場調整のために3日待ってもらっていたのが、今なら「今日入れることできる」と即座に判断できるようになった。
さらに重要なのが、作業データが蓄積されていて、後から品質管理活動にも活用できることだ。同社ではデータを分析することで、間違いやすいところや注意するべきところをデータベース化し、朝のミーティングで大型ディスプレイで品質管理シートを見せながら、作業員に対して具体的な作業注意を与えたりしている。
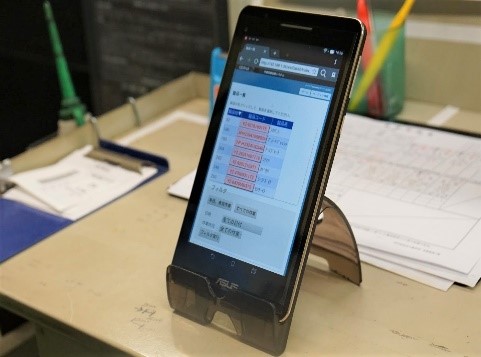
「業務の流れが変わったことについても、現場は“楽になるなら良いのでは”という反応でした。導入した後は“もう家に帰れるの”と喜んでいました。その後はむしろ現場から要望がたくさん出てくるようになりましたが、それをレクサー・リサーチの担当者が理解して対応してくれたことで、現場の担当者との信頼関係が深まりました」(田中氏)。
適用範囲を拡大することでさらなる業務改革を推進
GD .findiの導入は残業時間の削減だけでなく、作業員の精神面にも大きな効果をもたらした。「一人ひとりが次にやることが明確になったこと自体にも大きな意味があります。ディスプレイから全体の進捗が把握できるので、後どこまで頑張れば良いのかがわかり、精神的な負荷も減っています」と田中氏は語る。
また、システム化したことは取引先へのアピールという面でも成果が出ている。「こういう取り組みをしていることをお客様にお見せするのですが、“プレス工場でこんなことをやっているのは見たことがない”と驚かれます。それが当社の信頼獲得にもつながっています」(田中氏)。
技術部の大畑氏は「受注内容を元に金型製作の作業工程を決めるのが私の仕事ですが、予定の組み替えなどのプランニングの部分をGD.findiがサポートしてくれるので、自分は作業内容を考えることに集中できるようになりました。GD.findiは自分の考えをサポートしてくれるパートナーのような存在です」と話す。
また、生産管理を担当する西尾氏は「GD.findiに対しては、現場の状況が把握できること以外にも、大きな可能性を感じています。他の工場との連携やプレス時点でのデータの自動収集なども検討中です。GD.findiは私にとって切磋琢磨する相手なんです」とGD.findiとの知恵比べを楽しんでいるようだ。
同社では今後、金型自体の設計・製作、さらには営業から量産ラインへとGD.findiの適用範囲を広げていく計画だ。田中氏は「レクサー・リサーチはアナログを理解した上でデジタル化をアドバイスしてくれるので安心できますし、GD.findiは自社の状況に合わせて導入できるシステムです。どの製造業でも一歩一歩進めていけば必ず効果が出るでしょう」と感想を語る。業務改革に取り組む製造業にとって、GD.findiは強力な武器になるはずだ。
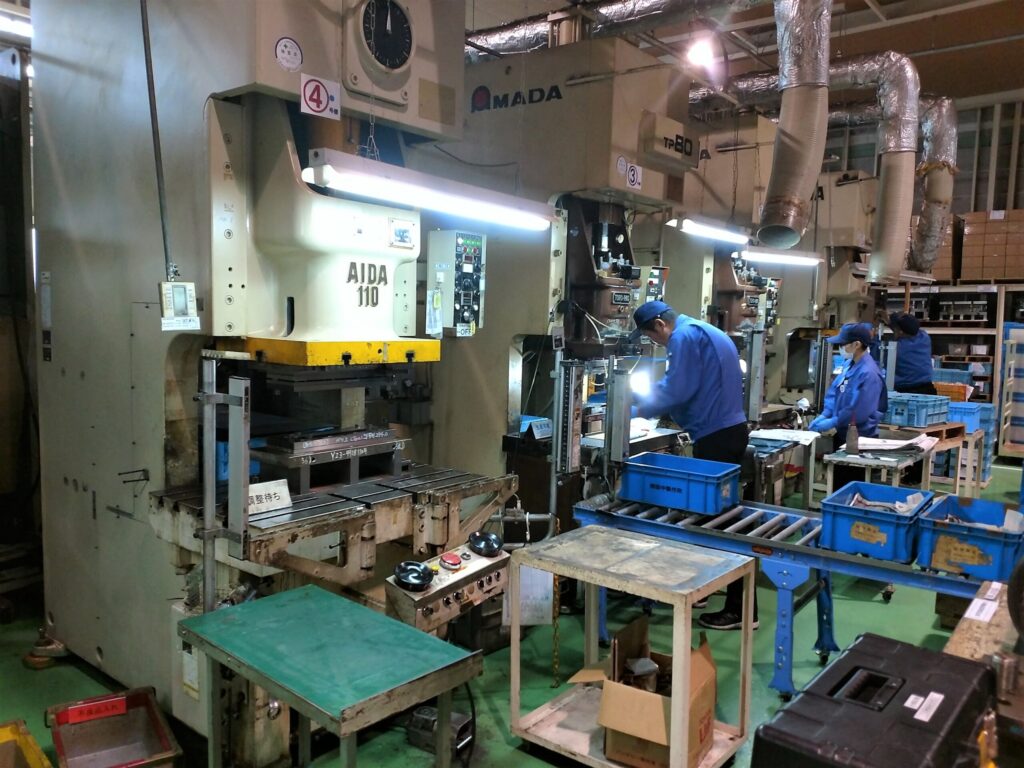
お客様プロフィール
会社名 | 株式会社田中製作所 |
---|---|
事業内容 | 精密プレス金型の設計製作による金属プレス部品の製造及びアッセンブリー等 |
創立 | 1965年(昭和40年)7月 |
資本金 | 4500万円 |
従業員数 | 130名 |
特徴 | 金属プレス加工を中心とした事業から、 コネクタの一貫生産、高精密加工分野へと、 独自の発想力と技術力を高めて時代のニーズに即応。 |
拠点 | 本社所在地:鳥取県鳥取市気高町宝木1562番地132 |
ご連絡先 | 0857-82-3355(本社) |
HP | http://www.heart-tanaka.co.jp |
公開されている以外にもご紹介できる導入事例がございます。
生産システムシミュレータ「GD.findi」や弊社サービスに ご興味のある方は下記のお問い合わせフォームよりご連絡ください。