- GD.findiが解決できる課題
- 製品紹介生産活動の現場とサイバー空間をつなぐ 生産シミュレーション
GD.find MS
Modeling & Simulation
ライン設計を強力に支援する完全ノーコード生産シミュレータ - よくあるご質問
- 事例
- ウェビナー
- お役立ち情報
管理職のための GDfindi 基礎講座 #3 「見える化」
言葉は、人類に複雑な現象を考え結果を共有することを可能にし、素晴らしい文化の発展に貢献して来ました。私達は名前のないものを考え、結果を共有することはできません。例えばエネルギーという言葉が存在しなかった時代には、エネルギーを生産し管理する発想は生まれなかったのです。
言葉は、人類に複雑な現象を考え結果を共有することを可能にし、素晴らしい文化の発展に貢献して来ました。私達は名前のないものを考え、結果を共有することはできません。例えばエネルギーという言葉が存在しなかった時代には、エネルギーを生産し管理する発想は生まれなかったのです。そして人間は文字を発明し、考えを記録する技術を獲得しました。文字は言葉を「見える化」しています。さらに印刷技術が開発され、知識を広く普及させる技術が誕生しました。
顕微鏡の発明は、目に見えないものを見える化し、例えば医学の発展に大きく貢献しました。微生物学は顕微鏡なしでは考えられません。そして、予防接種などを開発して、歴史に残る偉業を残したパスツールは、運良く顕微鏡が発明された時代に生まれたのです。つまり、顕微鏡の存在が必要条件であり、パスツールの才能と努力は十分条件であったのです。
見えない現象を見える化すると、問題提起が可能になります。そして、問題が提起されると、解決方法の開発まではさほど遠くありません。また見える化が不可能な現象は管理することができません。私達は私達の五感で把握できる領域だけでは満足せず、五感で把握できない領域を見える化して、近代文明を構築してきました。「見える化」が近代文明の原動力だと言っても決して過言ではありません。
そして、サイバーフィジカルシステム(CPS)の到来により、見える化が新しい意味を持つようになりました。CPSは物理的世界をサイバースペースでデジタルツインという形で再現しています。ウィキペディアでデジタルツインを検索しますと「さまざまな目的で使用できる物理的資産、プロセス、人、場所、システムおよびデバイスのデジタル複製を指す」とあります。
適切なソフトがあれば、私達は現象、システム、プロセス等のデジタルツインを使って見える化するだけではなく、様々なシナリオで、インプットに対してデジタルツインがどのような挙動をするか、もしくはどのようなアウトプットを出すかまでを見える化することができるようになります。見える化の範囲が画期的に拡張するのです。パスツールが運良く顕微鏡が発明された時代に生まれたように、私達は今まで未知だった世界をCPSにより見える化できる時代に運良く生まれたのです。これは素晴らしいことです。
GDfindiと見える化
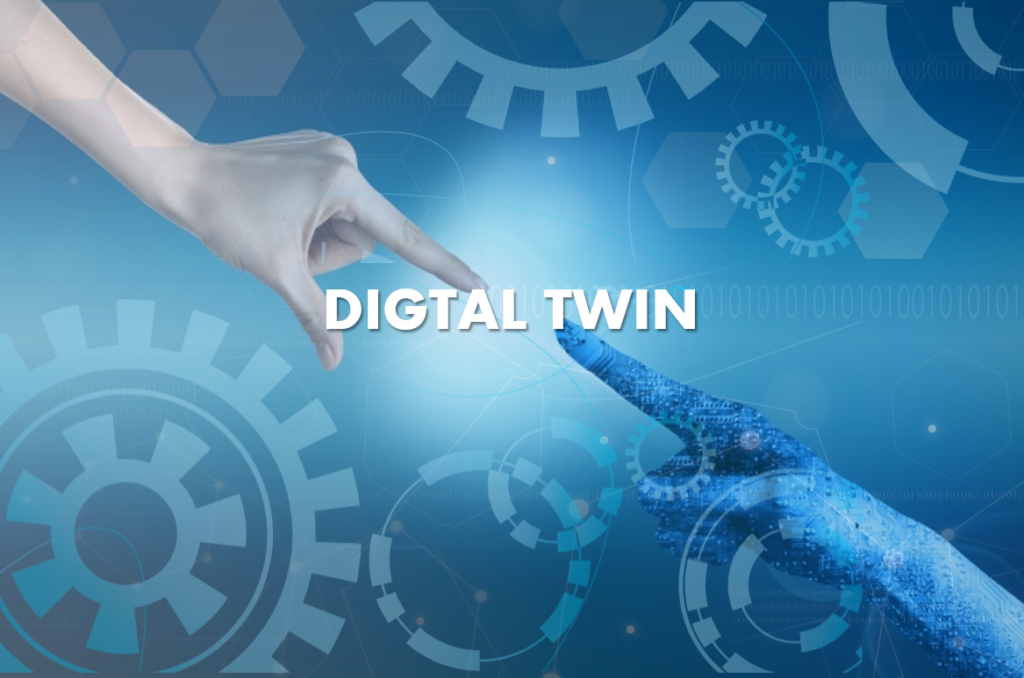
GDfindiはシミュレーションのツールと呼ばれていますが、正確には「生産システムの構造化されたデジタルツインを、プログラミングを必要としない手法で作成するツール」です。シミュレーションはGDfindiを使って作成されたデジタルツインを応用し付加価値を創造する数多くのアプリケーションのうちのひとつなのです。
一般には「プログラミングを必要としない」にスポットライトが当てられますが、「構造化されたデジタルツイン」にGDfindiのポテンシャルが凝縮されています。それは「構造化」という言葉の裏に、生産システムの構造化されたメタモデル(データモデルFINDI)が存在し、システムを構成する要素の相互関係が構造の中に既に埋め込まれていることを意味します。
管理職のためのGDfindi基礎講座シリーズの投稿の中に、GDfindiのモデリングは従来型シミュレーションの約10分の1しか時間がかからないとありますが、その一つの理由は、システムを表現するために必要な要素間の相互関係が、構造化されたモデルの中に埋め込まれているからです。また従来型シミュレーションモデルがシーケンスモデルと呼ばれる由来は、シーケンスをシミュレーションするために必要な領域しかプログラミングでモデル化されていないためです。例えば、従来型シミュレーションでモデルを変更すると、モデルは記述された変更にしか対応しません。GDfindiの場合は変更した局部と相互関係がある全ての要素にデザインインされた相互関係に基づき影響があります。
つまり、GDfindiのモデルはターゲット(対象生産システム)をシステムとしてモデル化しているのです。では、従来型シミュレーションでシステムの特性を持った生産シミュレーションのモデルを構築することは可能でしょうか?答えは「イエス/しかし」です。システムの特性を持ったシミュレーションモデルを構築することは従来型シミュレーションでも可能です。しかし、その為には非常に高いレベルのスキルを持ったプログラマーが経済的に許されないレベルの工数を費やさないと実現しないでしょう。
GDfindiが改善の革命を可能にする
この特性により、GDfindiでは生産システムの例えば何らかのレイアウト変更をした場合、システムのパフォーマンスがどのように変わるかを見える化することができます。このことは、例えばトヨタ生産方式で世界的に有名になった「改善」に革命を起こすことにつながります。従来の改善は経験と勘に頼れる範囲で、リスクの少ないスモールステップで改善運動を繰り返しました。GDfindiを使った改善運動では、経験と勘が効かない領域での見える化が改善を可能にします。そのため、生産システムの効率化スピードを従来の何倍にも高めることができます。
構造化されたモデルのメリット
モデルアーキテクチャーが構造化されていると、生産システムのモデルを複雑性に伴い階層化できます。構造化されているということは、木に例えますと、幹があり、枝があり、葉があるように、モデルが階層化されていることを意味します。新しい生産システムのコンセプトを確立する場合、複雑性の低い幹の次元でコンセプトを構築し、例えばレイアウトが想定通りの結果をもたらすか、シミュレーションで確認できます。そして問題点を解決できると、次の複雑性レベルへモデルを高めます。そして枝のレベルで、設定されたプロジェクトゴールを満たすために問題がないか、シミュレーションでチェックして、必要があれば最適化をします。従来は生産システム全体を経験と勘に基づき綿密に設計しました。そして、設計が期待されたパフォーマンスを実現するかは、生産システムを立ち上げないと、実証できませんでした。そのために、設計にはマージンが見積もられることが必要でした。
GDfindiを使った生産システムの設計は、アジャイル開発方式に非常に似ています。最小限の複雑性でシミュレーションの実行可能なモデルを作成し、シミュレーションを実施します。そして、シミュレーション結果をもとに、コンセプトが変更されます。納得のいくモデルが誕生するまで、このプロセスが繰り返されます。これはモデルの編集とシミュレーションにコストがかからないGDfindiだからこそ経済的に実現するプロセスです。この最小限の複雑性でシミュレーション可能なモデルがアジャイル開発方式のMVP(ミニマム・バイアブル・プロダクト)に相当します。GDfindiの場合はシミュレーションですから「ミニマム・エクセキュータブル・モデル(MEM)」が正しい名称になります。シミュレーション結果を見える化すると、プロジェクトに関わる全てのメンバーが問題点を理解し、お互いに知恵を出し合い短期間で解決案を捻出できます。そして大切なことは、新しい解決案がすぐにモデル化されて、シミュレーション結果としてアウトプットされることです。デイスカッションの余韻が冷めないうちに、結果をチームメンバーが理解できる形に見える化できると生産性が大幅に高まります。デジタル化されたデータは工夫さえすれば、見えなかった現象を誰にでも理解できるように見える化することが出来ます。
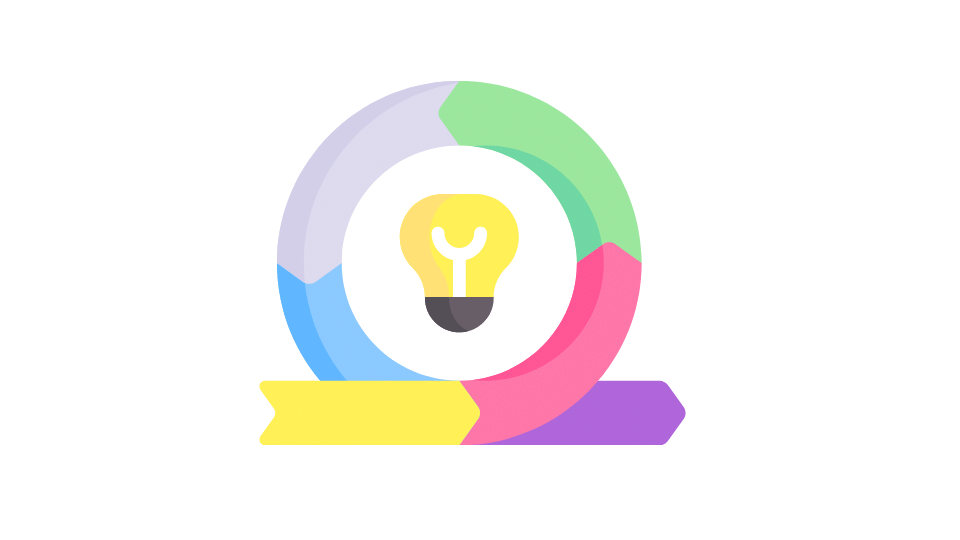
また、コンセプトが決定すれば、適切な領域を設定して、複数のプロジェクトを立ち上げ、詳細設計を複数のサブプロジェクトで並行して運行することが可能です。その際必要なことは、領域間のインターフェイスが適切な仕様で定められていることです。API(アプリケーション・インターフェイス)さえ事前に決められていれば、プロジェクト間の管理負担が殆どなくなります。プロジェクトをサブプロジェクトへ細分化する作業が適切に行われ、適切なAPIが設定されれば、複雑性の少ないサブプロジェクトのスピードでプロジェクトが運営されます。経験と勘に頼っていた時代には、必要な経験と勘のオーナーにプロジェクトが委ねられ、そのような人材が数少なかったために、複数のサブプロジェクトを立ち上げることは事実上不可能でした。ところが、シミュレーションを活用してPDCA-サイクルを回すことは、経験と勘がない人間にもできるのです。経験と勘に頼り手探りで設計するのではなく、数値化されたシミュレーション結果を基に判断を下すことが出来るのでそれが可能になります。テスラが従来の自動車メーカーの10倍以上のスピードで開発を可能にしているアジャイル方式は、GDfindiを採用すれば、少なくとも生産システムの領域で実現することが出来るのです。
ツールが変わると仕事の仕方が変わる
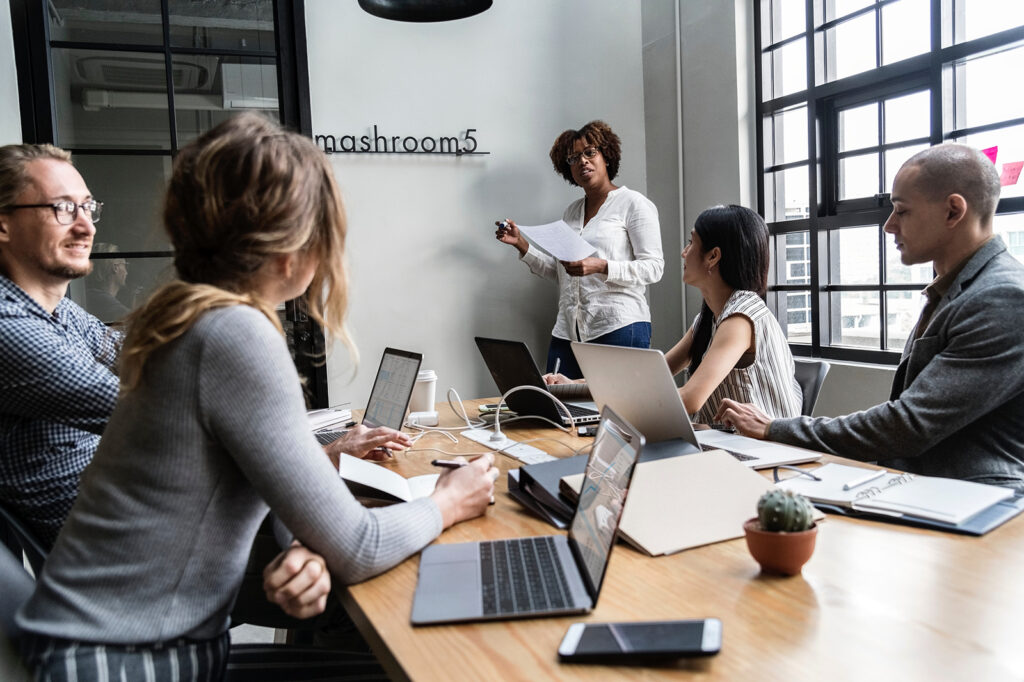
90年代に日経ビジネスの記事で紹介されたエピソードを私の記憶を辿って紹介します。当時3次元精密加工が可能なマシーニングセンター(MC)が発表されました。ある企業は、熟練金型工に3次元MCを与えて、仕事の効率化を期待しましたが、生産性が全く上がりませんでした。そのままでは「高価な3次元MCを使っても生産性は上がらない」という評価が残るところでした。ところが、入社して数ヶ月の新人社員とプログラマーのチームを作り、3次元MCを使わせると、金型作成が従来よりも30%短い時間で可能になったそうです。熟練工は経験と勘に頼った彼の得意な仕事の仕方の成功体験に束縛され、3次元MCの使い方を研究しなかったのです。過去の束縛がない新入社員は、3次元MCの使い方に集中して、素晴らしい実績をつくりました。データサイエンスの教科書は「大学の研究調査ではデータサイエンスを導入すると、従来の企業プロセスの生産性が1%から3%改善される」という実績を紹介して、持論を展開します。
「従来の経験と勘に頼り最適化されたプロセスは、長年最適化されている以上、データサイエンスを導入しても伸び代が少ない。ただし、データサイエンスには従来可能でなかったことを可能にする力がある。その領域が見極められデータサイエンスを投入すると、大きな付加価値を実現することが出来る。」
GDfindiにも全く同じ理論が通じます。従来の経験と勘に頼り、暗闇を手探りで歩くような仕事のパターンだったところを、GDfindiを導入すると、見える化が実現します。ただの見える化ではなく、プロジェクトのチームメンバー全てが理解できる形に現象を見える化することができるのです。そして、チームメンバーがアイデアを出し合い、高い次元の解決案を捻出することができるのです。その為には、従来の手法に頼らず、GDfindiを使った最適な仕事の仕方を考案する必要があります。その際のポイントはデータサイエンスの教科書が提供してくれています。「GDfindiがないときは出来なかったが、GDfindiで可能になったことは何か?」「馬鹿とハサミは使いよう」と申しますが、GDfindiもツールです。使いよう次第では過去に見えなかった現象が見える化でき、問題が定義され、解決案が導かれ、生産性が上がります。
一つの極端な例は「今まで見える化ができないために、選択オプションにも乗らなかった生産方式を、GDfindiを採用すれば見える化して、使いこなすことが出来る」です。テスラはライン生産方式を廃止しています。そのために複数の同じ工程をカバーするセルの一つを必要に応じて生産プロセスから外し、新しい改善案を常時現場でテストできる体制を作っています。その為、今までには考えられなかった改善活動のスピードアップを実現しているそうです。GDfindiの特性を把握して上手に採用すれば、今までは管理ができないために、導入できなかった生産方式の導入も夢ではありません。
まとめ
ご紹介したケースは氷山の一角です。身近な見える化の例は、大谷翔平で脚光を浴びたアメリカ大リーグです。大リーグではスタキャストという装置を使い選手の動きを数値化しています。
数値化すると、今までは考えられなかった指数が誕生します。著名な指数は大谷翔平が大リーグトップの成績を上げたバレルです。指数が誕生すると、どのようにして、選手を評価して、成績を伸ばすか新しい技術が開発されています。これと全く同じことがGDfindiを使えば、生産システムの解析、改善で実現します。
「シミュレーション」という表現を使うと、従来型シミュレーションのイメージに縛られて、GDfindiの使い方が束縛されます。従来型シミュレーションは様々な制約がある為に、シミュレーションが貢献できるポテンシャルの僅か数%しか開拓出来ていません。ユーザーが必要としている質問は「従来のシミュレーションができることを、GDfindiが安くできるとか、早くできるか?」ではありません。ユーザーがするべき質問は「GDfindiを使えば、どのような今まで出来なかったことが実現するか?」です。そしてキーワードは「見える化」です。「何がGDfindiを使うと見える化できるか?」答えは驚くほど沢山あるはずです。
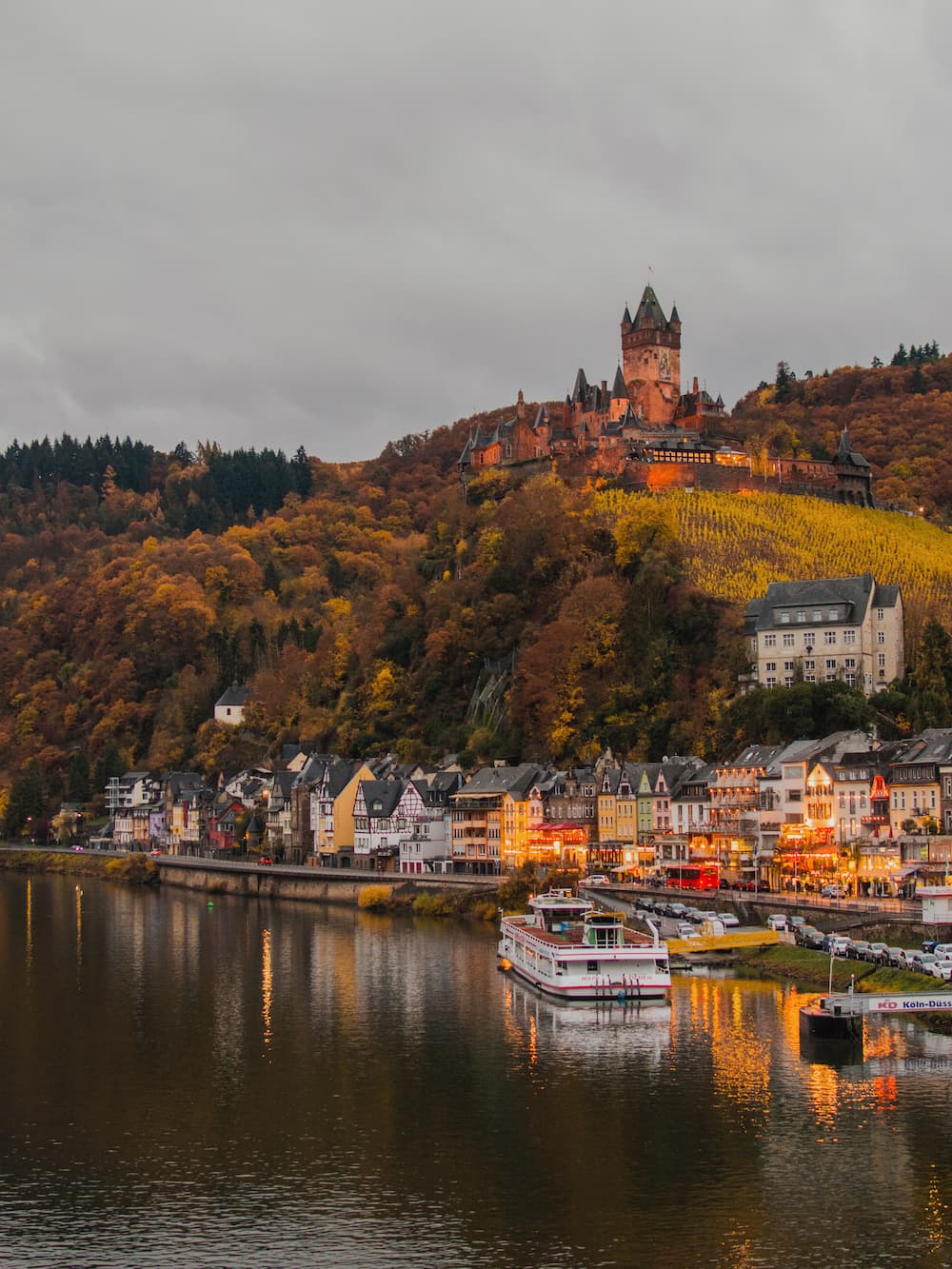
Ando Mahito
中学時代にドイツに渡航。カールスルーエ工科大学にて、機械工学を専攻の後、PhDを取得。卒業後は、シーメンス社やボッシュグループにて、プロジェクトマネジメントおよび経営企画、社内コンサルティングに携わる。
現在では、株式会社レクサー・リサーチ、フラウンホーファー財団IPA研究所と共同開発契約を結び、シミュレーション系最大手エンジニアリング会社と協力関係構築から生産シミュレータGD.findi のドイツ市場開拓に従事。
関連記事