- GD.findiが解決できる課題
- 製品紹介生産活動の現場とサイバー空間をつなぐ 生産シミュレーション
GD.find MS
Modeling & Simulation
ライン設計を強力に支援する完全ノーコード生産シミュレータ - よくあるご質問
- 事例
- ウェビナー
- お役立ち情報
事例:電気機器メーカー P社 様
ブラックボックス化していた搬送システム設計をユーザ主導型に。
コスト削減やスムーズな社内承認を実現
業種:エレクトリック 課題:システム設計がブラックボックス化しており、価格交渉以外関与できなかった
導入前の課題 |
|
導入後の効果 |
|
GD.findi MS を選んだ理由 |
|
ブラックボックス化していたシステム設計をユーザ主導型に。
コスト削減やスムーズな社内承認を実現
電気機器メーカーP社では、当時工場敷地内の屋外搬送システムの最適化設計が進められていた。複数の建屋を結ぶ搬送システムであり、構内のトラック搬送を避けるために高架設計にすることが考えられていた。従って、エレベーターの個数の最適化検討が求められていた。
GD.findi MS 導入に至った背景
同社では、このような搬送システムの設計において従来はゼネコンがシステムを設計し、同社に提案する形であった。そのシステム設計の過程やバックグラウンドはブラックボックス化されており、同社は価格交渉以外ほとんどシステム設計変更等の議論ができなかった。
上記の課題に対して、事前に社内で納得のいく搬送システムを設計し、ゼネコンに見積り・納品依頼をする流れに変革することはできないか、とツールの検討が進められた。その中でも、多様な生産システムの各要素を検証するにあたって、運用における再利用性や編集性の高い GD.findi MS が採用された。
GD.findi MS を導入したプロジェクトの流れ
ゼネコン主導で進められたプロジェクトは、GD.findi MS の導入後、以下のように変化した。
- シミュレーションの目的、範囲、制約条件(ヒトや搬送、時間、資源など)の洗い出し
- GD.findi MS にデータを割り振り、総合的なシミュレーションを実行
- シミュレーション結果から得られたアウトプットを現場と協議し、最適値を決定
- この結果をゼネコンに提出し、見積りを取る。また上層部には、GD.findi MS のアニメーションやシミュレーション結果をもとにプレゼンを行い、社内合意形成を図る
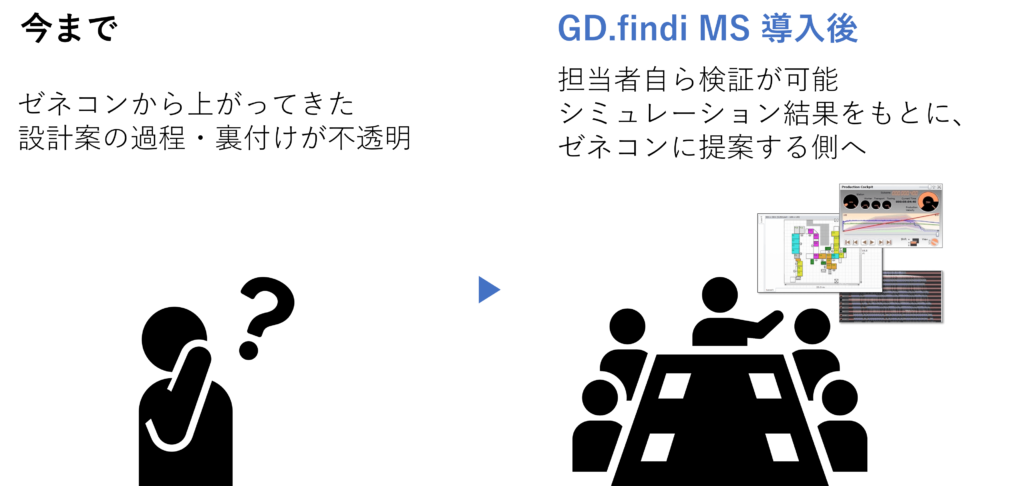
GD.findi MS 導入で得られたメリット
1. ユーザ主導型のプロジェクト推進が実現
GD.findi MS を活用することで、現場自ら複数のオプションからその最適値を導出することが可能になった。従来はゼネコン主導型でプロジェクトが進められていたが、GD.findi MS 導入によりユーザー主導型のプロジェクトに改革することができた。また、ゼネコン側に「このコンセプトは出来ない」と却下された場合も、「ではこのコンセプトでは?」と同社にはバックアップの持ち駒があるため、常に主導権を確保できた。
2. 無駄な工数、コストの削減
事前にシミュレーションで複数シナリオの結果が得られるため、ゼネコン側とのすり合わせや多くのミーティングに要していた時間が大幅に短縮された。結果として、ゼネコンの余剰見積もりの回避、システムの最適化などを込めて総工費の5~10%を削減できたと考えられる。
3. 上層部も議論に関わることができ、社内承認がスムーズに
検証結果をアニメーションやデータで可視化することができるため、上層部も最適化議論へ加わることができ、プロジェクトの承認がスムーズになった。
GD.findi MS ならではのポイント
1. 現場の声が反映されたシステム設計に
GD.findi MS は完全ノーコードで扱えるため、プログラミングやITの専門知識をもたない担当者自らの運用が可能である。現場層も巻き込んで運用を進めることで、現場の声が反映されたシステム設計が実現できた。
2. プロジェクトのイメージを構想段階から得ることができる
GD.findi MS はレイアウトと生産プロセスをGUI上で可視化できるため、プロジェクトのイメージを構想段階から得ることができる。また、シミュレーションモデル作成における柔軟性が他のツールよりも高いため、モデルを作りこむ前に、仮の値で登録することも可能であるため、認識を共有や確認をスムーズに行うことができた。
お客様の声
GD.findi MSを検討している方へのメッセージ
GD.findi MS を使い慣れてくると、新しい使い方の展開が可能になり、想定外のメリットに巡り会えます。キーワードは「見える化」です。
単発のシミュレーションでは見える化に限度がありますが、GD.findi MS のように複数シナリオを容易にできるツールでは、今まで見えなかった現象から新しい問題点を見える化し、解決することができます。
また見える化が出来ない為に、その管理が困難であった複雑な多品種小ロット生産方式の管理も出来るようになると考えられます。
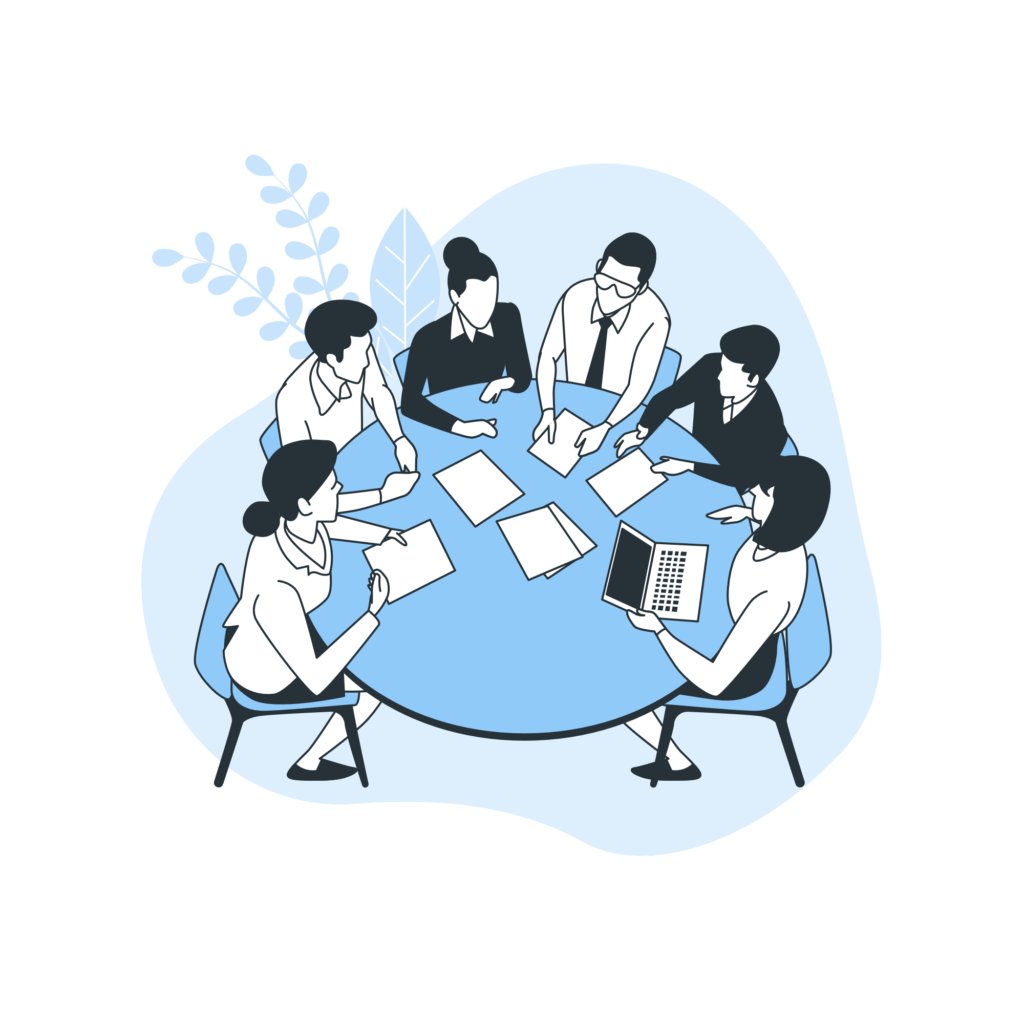
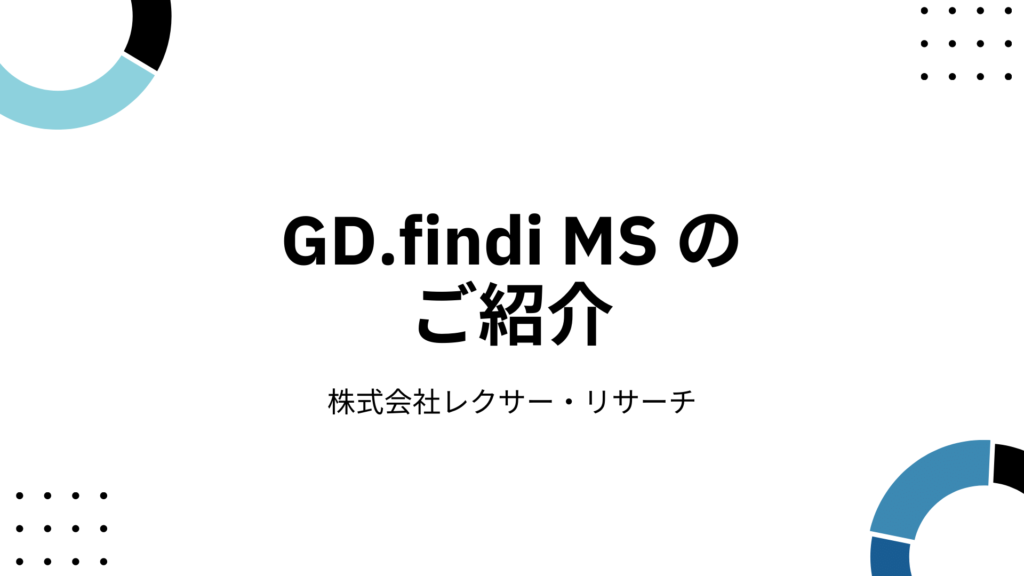