- GD.findiが解決できる課題
- 製品紹介生産活動の現場とサイバー空間をつなぐ 生産シミュレーション
GD.find MS
Modeling & Simulation
ライン設計を強力に支援する完全ノーコード生産シミュレータ - よくあるご質問
- 事例
- ウェビナー
- お役立ち情報
GD.findiとiPhone、テスラの共通点があった
前回はGD.findiが生産システムの構造化解析により編み出されたFINDIデータモデルをベースに従来の生産シミュレーションでは考えられないことを実現していることを紹介した。本投稿ではGD.findiの応用の仕方について考察したい。その従来シミュレーションでは考えられない使い方とは一体何なのだろうか?
ジョージ・ブランケンシップ物語
ジョージ・ブランケンシップ(George Blankenship)と言う名前をご存知の方は意外と少ないかもしれない。ところが「アップルストアの生みの親」と言うと、誰でも身近なイメージをお持ちになられるはずである。
ある日突然、ブランケンシップ氏はイーロン・マスクから電話を受けとった。「テスラの仕事を手伝ってくれ」と言う要望である。「何故、隠居している私を?」と言う質問にイーロン・マスクは答えた。「(私は)スティーブ・ジョブズ と同じことをしなければいけない。スティーブはiPhoneの使い方から市場を教育した。テスラも市場を電気自動車の使い方から教育しなければいけない。君の才能と経験が必要なのだ」
テスラ車は駆動系を燃焼機関から電動モーターへ置き換えただけと言う印象が強いが、テスラ車のコンセプトは全く違うのである。必然的にテスラ車の使い方も違う。ブランケンシップはテスラの顧客を教育するコンセプトをテスラのために開発した。テスラは全く新しい自動車のあるべき姿を提案している。そのために、積極的に市場を教育しないと、ただテスラ車を出荷しただけでは、正当な評価を得ることが出来ない。テスラが顧客満足度でダントツの成績を収めているのはジョージ・ブランケンシップの功績である。
GD.findiも全く同じカテゴリーに属する。即ち、従来型シミュレーションと同じカテゴリーだと言う考え方で使つかわれれば、大した顧客満足度が期待できない。イーロン・マスクが主張するように「既存のルールや常識の束縛」に囚われず、新しい道を開拓する者が、GD.findiを採用して栄光を手にするのである。レクサーの使命は、ジョージ・ブランケンシップを手本にユーザーにGD.findiの使い方を解説して、ユーザーがGD.findiのポテンシャルを引き出し、日本の製造業に明るい希望の光をもたらすことである。
ジョージ・ブランケンシップがGD.findiを説明したらどのようにGD.findiの特徴へスポットライトを当てるか想像してこの投稿を企画した。本投稿は下記のテーマから構成されている:
- 生産シミュレーションの革命
- 再利用性のマジック
- 究極のGD.findi応用法
- GD.findiで宝の山を探す
- 眠っているコスト改善機会を目覚めさせる
- 究極のコストダウン
- イーロン・マスクが導入したもう一つの奇跡
- GD.findiで起こる奇跡
日本の製造業がGD.findiを有効に活用し、素晴らしい実績を上げることを祈る。
生産シミュレーションの革命
生産シミュレーションのコスト構造は人件費が90%以上を占めている。従来型シミュレーションの場合はプログラミングが始まる前に、生産システムの解析が行われ、シミュレーションモデルのコンセプトが作成され、入念な検証が行われる。このプロセスに関して、ドルトムンド大学のラーベ教授が編集した分厚い本に仔細が記載されている。プログラムを書き始めると、修正コストが非常に高くつくので、事前に完璧なモデルを用意して、プログラムの修正を回避しないと経済性が確保出来ない特徴が従来型シミュレーションにある。
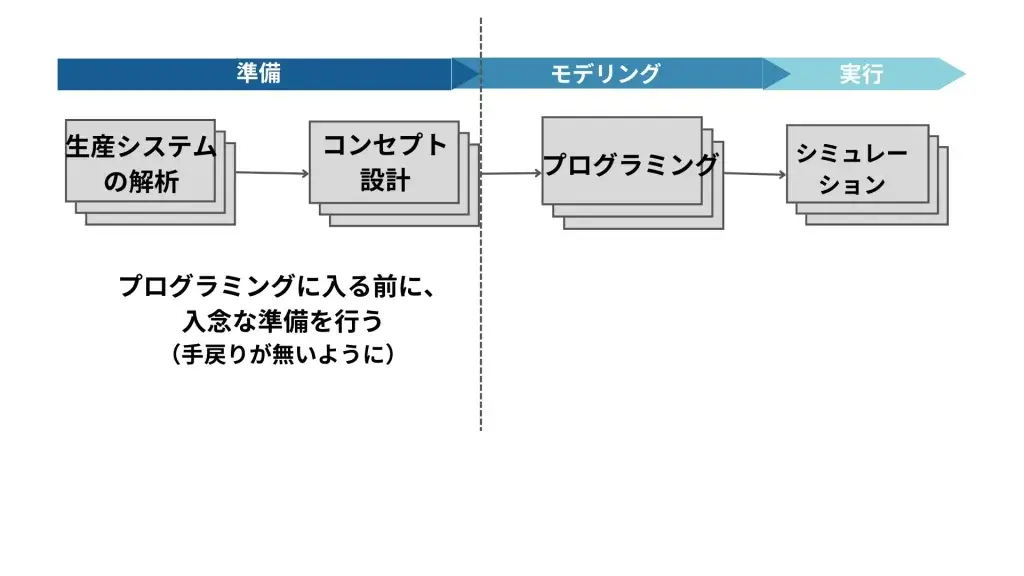
こう書くと「我が社ではそのようなことをしていない!」と言う声が聞こえてきそうである。同じモデルコンセプトしか必要のないシミュレーションの使い方を長年していると、マンネリ化して、そのような反論が当然上がってくる。
しかし、シミュレーション用途の多様性を追求すると、フロントエンドで大きな工数が発生する。GD.findiの場合はFINDIデータモデルが従来型シミュレーションのフロントエンドに相当する業務をソフトウエア化しているので、ターゲット生産システムとアプリケーションが多様であっても、コストが発生しない。ユーザーが何をモデル化するか決め、GD.findiが記述方法を管理する対話型モデリングはモデリングの工数を従来型生産シミュレーションの10分の1程度に削減する。これはGD.findiを体験した従来型シミュレーションのエキスパートの証言である。
その主な理由はGD.findiが自動的に記述する内容を、従来型シミュレーションでは一々コード化しなければならないからだ。フロントエンドと編集の工数を考慮すると20分の1程度の工数が正当な評価と言える。さらに、GD.findiのコピペ編集機能を上手に使うと、千分の1以下のシミュレーションコストが期待できる。ここで、その内訳を紹介する。
再利用性のマジック
コピペ編集が可能であると、シミュレーションモデルの再利用性が実現する。平均的生産システムであれば最低5年間は大きなシステム変更がない。すなわち、5年間は1度作ったモデルを再利用し編集すればシミュレーションが実現する。マザーモデルから、コピペ編集で小孫モデルが誕生するわけである。
「我が社ではシミュレーションの需要は1回限り、再利用の必要はない!」という時代遅れな声が聞こえて来そうである。従来型シミュレーションが限られたアプリでしか経済的に応用できない事実が常識化して、それに何の不都合を感じないと、そう言う意見が飛び出す。近い将来「そう言う不自由な時代もあったらしい」とパワーステアリングがなかった時代に「か弱い女性には自動車の運転が難しい」と考えられていたことと同じレベルの昔話になっているだろう。
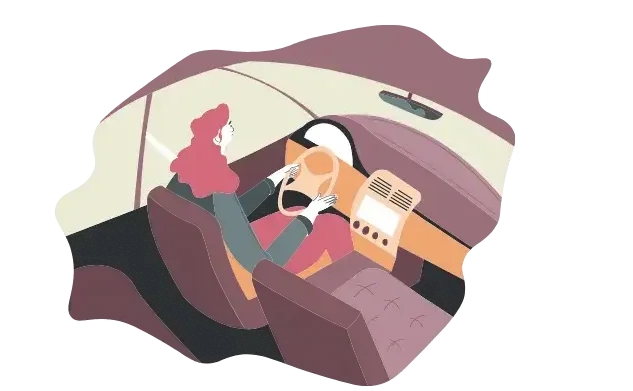
シミュレーションの経済性は
「付加価値 - シミュレーション費用 > インセンティブ」
で表現することができる。シミュレーション費用が小さくなると応用範囲が指数曲線で広大する。それと共に、小孫モデルの総数が大きくなり、シミュレーション費用がさらに小さくなる。この関係を数値化すると次のようになる。
「マザーモデル作成コスト/子孫モデル総数 + 編集コスト」
ドイツ最大手の生産シミュレーションに特化したエンジニアリング会社が受注する最小プロジェクト受注単位は約400万円である。従来型シミュレーションの場合、プロジェクトの目標が達成されると、作成されたシミュレーションモデルは使い捨てになる。膨大な工数がかかる編集をして別の用途に再利用するより、新規にゼロからモデルを作成した方が経済的に有利だからである。GD.findiの場合はどうであろう?比較対象を容易にするために、最初のGD.findiプロジェクトに400万円かかったと仮定しよう。GD.findiのモデルは再利用性があるために、コピペ編集すれば新しいプロジェクトに使える。10個のプロジェクトに採用したとすると、小孫プロジェクトのコストは下記の式で表現できる
「マザーモデル作成費(400万円)/小孫プロジェクト総数(10) + 編集コスト」
仮に編集コストが初期プロジェクトの10%だとすると小孫プロジェクトのコストは80万円となる。つまり、シミュレーションを経済的に採用できる範囲が
「付加価値 - シミュレーション経費(400万円) > インセンティブ」
から
「付加価値 - シミュレーション経費(80万円) > インセンティブ」
と大幅に広がる。コストが下がると指数曲線に従い、どんどんシミュレーションが使える裾野が広くなる。経験値としてコピペ編集に費やされる工数はネット値で数分、グロス値で15分程度が条件によってはすでに実現している。
これに相当する作業は、例えばステーション(装置)の配置換えであったり、装置のパーフォーマンスを2倍に設定したりするなど様々なケースが考えられる。15分とは、時給5000円だと仮定して、1250円である。つまりシミュレーションを採用すれば採用するほど、シミュレーション当たりのマザーモデル作成コスト分担費は低くなる。もちろんコピペ編集に半日かかるプロジェクトもあるであろう。それでも編集コストは2万円である。ある年商300億円規模のGD.findiユーザーは現在年間40シミュレーションモデルのペースでGD.findiを使っている。プロジェクト単位のマザーモデル作成コスト分担費は上記モデルを使い推定すると、10万円レベルである。編集に1日かかったとして、1シミュレーションのコストは14万円だ。このユーザーは現在、環境を整備してモデル作成件数を増やす試みをしている。具体的には生産システム全体のモデル、生産システムの一部を使った部分モデルなどをライブラリーとして用意し、シミュレーションを使いやすい環境を整備し、現場の人間の教育を行い、シミュレーションを扱える人材を増やしている。
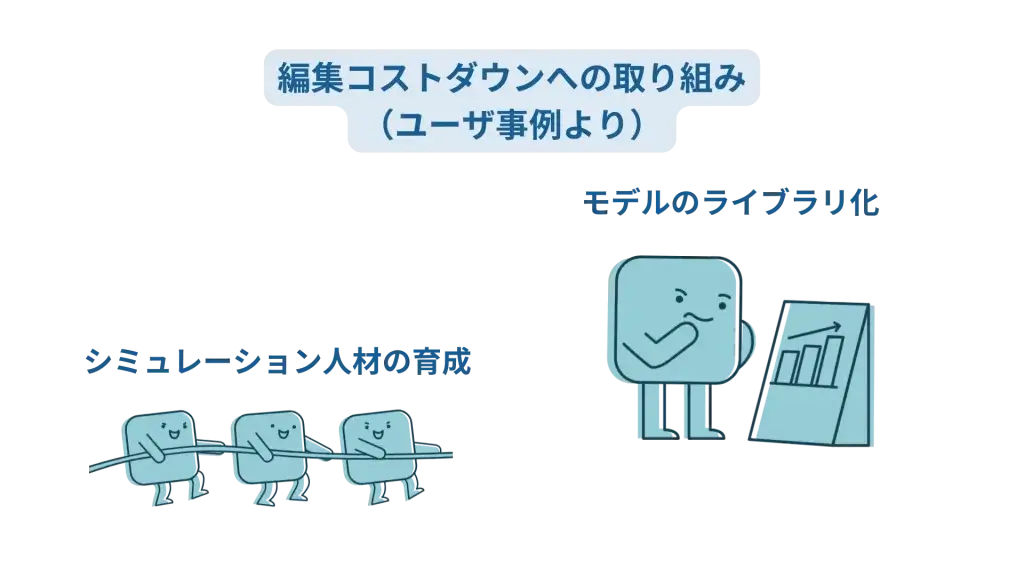
究極のGD.findi応用法
GD.findiの特性が認められて、GD.findiの本格的採用が実現すると、次のような使われ方が一般化する。
「毎週プロジェクトが立ち上げられ、1プロジェクトで平均して30のシミュレーションが実施される。そうすると、1年が正味44週間として、年間1320回シミュレーションが実施される。生産システムの寿命が5年と仮定すると、6600回がシミュレーションの総数となる。」
この場合、1シミュレーション当たりのマザーモデル作成費の負担は僅か606円である。編集に1時間かかる応用でシミュレーションを30回実施すると仮定すると、1シミュレーションの単価は5606円であり、プロジェクトでかかるコストは僅か17万円である。
「年間1320回もシミュレーションを実施するなど馬鹿馬鹿しい」という声が聞こえてきそうであるが、これが生産システムシミュレーションの将来像である。シミュレーションのプロジェクトには大型投資が伴うと言う古い概念があるから「馬鹿馬鹿しい」と言うことになる。本田宗一郎にまつわる逸話を思い出してほしい。彼は抜き打ちで工場を訪ね、前回の訪問以来工場に変化がないと工場長が怒られた。工場は絶えず変容しているものである。
コスト改善プロジェクトの頻度は必要な投資額により決まる。GD.findiのコスト体系であれば、投資の全く必要のないプロジェクトもシミュレーションの対象になる。投資の全く必要にない最適化プロジェクトの代表例は人員投入計画である。シミュレーションの対象がモバイルであればあるほど、投資負担が低くなり、頻繁に最適化が可能になる。シミュレーションコストが低くなると、いくらでもシミュレーションを応用し経済的に新しい付加価値を捻出する機会が溢れ出す。GDfidniを導入し、使いやすい環境を整備すると、本田宗一郎の理想「工場は常に変容し生産性を上げる」が実現する。
GD.findiで宝の山を探す
ここでシミュレーションの経済性の式をもう一度思い出してみよう
「付加価値 - シミュレーション費用 > インセンティブ」
シミュレーションコストが低くなれば過去に経済性が成立しなかったプロジェクトにシミュレーションが使えるようになる。それが何を意味するか考えてみよう。我々は直感的に、大きな最適化ターゲットを選ぶ習性を持っている。経済性の確率が難しい手法を経済的に使うためにはスケール効果を使い、規模の大きなプロジェクトを選ばなければならないからだ。
パレートの法則を使いモデル化すると、20%の投資案件が総投資額の80%を占める計算になる。そして、4%の投資案件が総投資額の64%を占める計算である。つまり、企業の取締役会で扱われる案件は投資額の64%に相当するプロジェクトと考えることが妥当である。それは、企業のコスト改善意欲を最も大きなテーマに集中させる特性が存在するからである。予算決定権が取締役会にあれば、64%の投資に相当する4%の案件に予算が集中する。
ところが、常に予算が集中しているテーマは最適化が進んでおり、コストダウンのポテンシャルが年々少なくなる傾向にある。自動車業界のコストダウンプロジェクトなどは、1%のコストダウンが実現すれば、大成功で赤飯を炊くと言う。通常は、小数点以下のコストダウンが平均的である。
ここで、GD.findiを上手に使い、1回のシミュレーション費用を大幅にコストダウンすると、過去に最適化プロジェクトの対象から外れた課題が経済的に最適化できるようになる。それらの課題は2つのカテゴリーに分けられる。
① 従来の最適化手法では、経済的な最適化が無理であると判断され、最適化がされなかった、眠っている課題
② 適切な「見える化」が出来ないために、問題点を明確に割り出すことができなかった課題
GD.findiを採用するとこれら二つの課題を解決することが出来る。そして、過去に最適化努力がされていなかったテーマを解決すると、小数点以下の最適化結果ではなく、二桁レベルのコストダウンが夢ではない。過去に改善努力がされていなかった領域で最適化が実現すると、つまり、GD.findiを使ってでしか経済的に対応できない、規模の小さなプロジェクトを数こなすと、宝の山を発掘することになる。数値化すると宝の山の規模がわかる。60%で実現する小数点以下の改善効果が0.5%だとここで仮定しよう。過去に改善努力の実績がない40%では二桁が実現可能であるが、保守的に5%の改善効果が期待できると仮定しよう。(60 x 0.005 = 0.3) に対し(40 x 0.05 = 2)と言う結果が出る。どちらの投資効果が高く、会社への貢献度が大きいかは歴然である。
眠っているコスト改善機会を目覚めさせる
ここで、「小さなプロジェクトを複数こなすより、大きなプロジェクトに集中した方が効率は良い」と言う意見が出てくることがある。ところが、実際には大きなプロジェクトは予算申請の必要があり、オーバーヘッドが大きい。GD.findiを導入して、現場の人間がシミュレーションを扱える環境を整備すれば、至る所で今まで実現しなかったコストダウンが実現する。コストダウンプロジェクトが実現しない理由は2つある。
① 「付加価値 -プロジェクトコスト > インセンティブ」の条件が満たされない。
② 予算申請をする手数が大きく、精神的閾値が高く、予算申請に至らない。
GD.findiが採用されて、現場の人間の教育が浸透すると、プロジェクトコストが劇的に低くなり、小規模プロジェクトでも経済性が実現する。そして、現場の人間がGD.findiで自由にシミュレーションを扱えれば、プロジェクトを社内もしくは社外のエキスパートへ外注する必要がなくなり、予算申請の精神的負担から解除される。「アイデアを思いついたから直ぐにGD.findiでチェックしてみる」と言う習慣が当たり前になる。
究極のコストダウン
我々は、こだわりの文化に対して誇りを持っており、拘りに拘って、既存のシステムを最適化することが得意である。ところが、究極のコストダウンは全く新しいコンセプトの導入であることを忘れてはいけない。
テスラのイーロン・マスクは「問題解決の目処が立っているレベルの志の低いプロジェクトは必要ない」と断言する。「実績のないところで、試行錯誤を繰り返して新しいソリューションを開拓するから競争力が養える」とも彼は主張する。但し、新しいコンセプトを導入するとは、リスクを伴うことも事実である。イーロン・マスクが選んだ道は「失敗の山を築き成功する」である。成功確率が0.1%の目標であっても、必ず成功する道が存在する。そして、学習が伴う試行錯誤を根気よく続ければ、成功の道が必ず開ける。
ここで大切なことは、失敗のコストが安いと、試行錯誤のPDCAサイクルを何回も回せることだ。イーロン・マスクはサイバースペースでコストが安い失敗を繰り返し、不可能と思われていた目標を達成することに成功している。物理的空間では「失敗のコスト」が高く、試行錯誤のサイクルを何回も回すことが経済的に考えられなかったが、サイバースペースで失敗を重ねることは経済的に許され、早く結果を得られる事実にイーロン・マスクはいち早く気付き、競争力強化に応用している。GD.findiを採用すると、試行錯誤のPDCAサイクルを低コストで高速に廻すことが可能になる。物理的空間では経験と勘に頼っていては、気が遠くなるほど低い成功確率のコンセプトが、PDCAサイクルを回し続けると実現する。
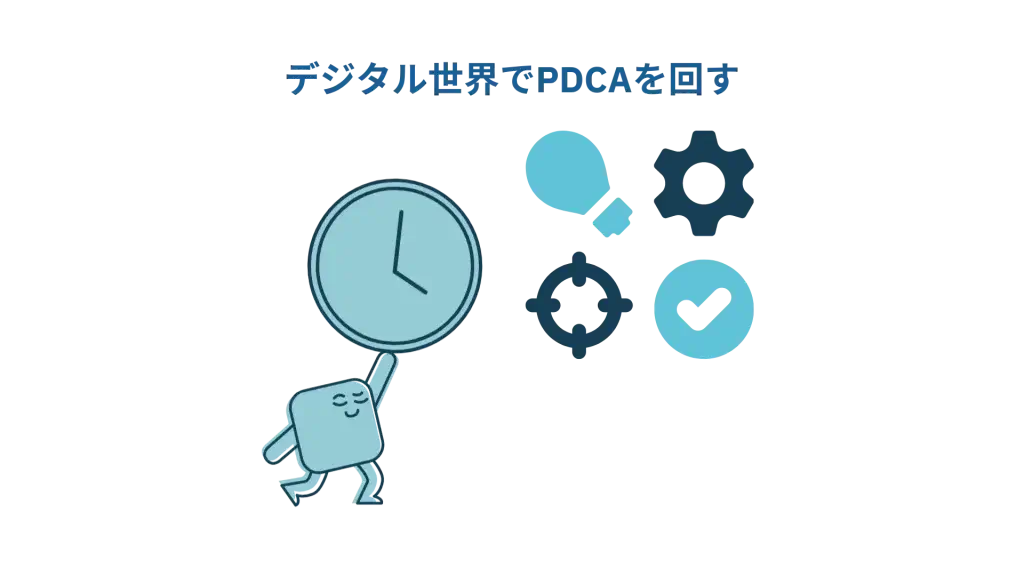
イーロン・マスクが導入したもう一つの奇跡
イーロン・マスクはプロジェクトの決定権を現場に委託している。これはアップルのスティーブ・ジョブズが「決定権はノーハウの所有者に委ねられるべきであり、社内で地位が高い人間に委ねられるべきでない」と主張したことと全く同じである。そして、イーロン・マスクはその実現のために様々な工夫をしている。
その一つが、サイバースペースへ開発を移し、開発コストと開発時間を最小限にとどめる努力である。開発コストがサイバースペースで低くなれば、決定権を委託するリスクが少なくなる。サイバースペースでの試行錯誤の唯一のコストはシミュレーションの回数である。物理的空間では同等の試みをすると、数万倍のコストと時間がかかり、事実上経済性が期待できない。
GD.findiを使いこなせると、現場の人間が、自分のアイデアにシミュレーションを使い検証することができる。予算申請をしなければいけない社内規定のハードルの下で気軽にシミュレーションが使えると、奇跡が至る所で起こる。
GD.findiで起こる奇跡
「奇跡」とは、想像できなかったことが実現することである。ここでGD.findiが起こす奇跡のメカニズムを説明する。
人類の進歩は「言語化」と密接なつながりがある。「文明」と言う言葉が表すように、ある領域で言語化が実現すると、新しい知見が生まれる。例えば、「エネルギー」という概念が言語化される以前は、我々はエネルギーについて思考することが出来なかった。「言語化」により、我々は我々の創造力を高めることができる。
GD.findiは構造解析に基づいた生産システムのデータモデルから導かれたモデリング言語である。つまり、GD.findiを使いこなせると、抽象化した次元で生産システムを考える能力が養われるのである。それだけではなく、最近知識には宣言的知識とプロセス知識があることが判明している。宣言的知識とは文章化できる知識であり、プロセス知識とは実践により体得する文章化できない知識のことだ。またGD.findiを使いこなすと、生産システムを抽象化した新しい目線で見ることができるだけでなく、様々なアイデアをシミュレーションすることにより、飛躍的にプロセス知識を向上させることが出来る。何十年掛けても得られなかった知見を数ヶ月で得ることが出来る。
何故ならば、生産システムは生産性を最適化するために非常に狭い実績のあるパラメータ領域でしか運転を許されないからだ。現場の人間の経験値は生産性が許す範囲でしか得られないのである。実績の外の領域で新しいアイデアをシミュレーションすることで現場は生産システムの理解を深めることが出来、理解が深まると更に新しいアイデアが生まれる。
つまり全く新しい成長曲線が誕生するのである。成長曲線は指数曲線であり時間と共に傾斜が急になる、つまり予想できなかった奇跡が実現する。さらに、GD.findiが可能にする言語を使って、現場の人間が新しい知見を共有すると、組織の改善意欲が高まる。生産現場の大幅なレベルアップが実現し、彼等の知見をGD.findiで言語化し、他の部門と共有することが可能になる。
GD.findiは今まで考えられなかった生産システムで起こる動的現象を言語化するツールとして機能するのだ。デザイナーとか芸術家の世界では、自分の作品を言語化して説明できる人が優秀であると言う定説がある。それは自分の作品を言語化する能力がある人は、考える力に富み、自分の作品スタイルを展開する能力が豊かであるからだ。生産システムを抽象化した言語で表現出来ると、全く同じ効果が期待でき、現場の人間の思考が新しい次元へ到達する。例えば改善運動が飛躍的に進化する。これについては今後の投稿で仔細を解説する。
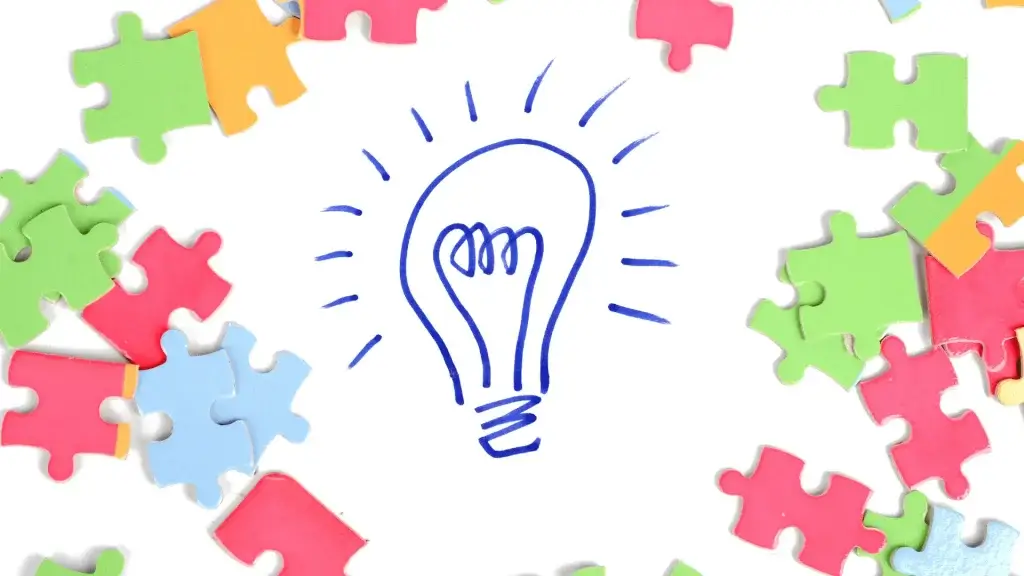
まだまだ、GD.findiの使い方に関しては未知の部分が多い。GD.findiは創造性が豊かなユーザーが、GD.findiのポテンシャルを引き出すことを待っている。考えられる用途は社員教育、工場間の知見の交流など尽きることを知らない。ジョージ・ブランケンシップがGD.findiの使い方を説明したならば、どのような解説をするか想像して、この投稿を企画してみた。是非、GD.fidniの使い方を工夫して、後を絶たない見学者が吃驚するような工場を作ってほしい。
次回投稿では、どのようなアプリが実現するか、具体的な例を解説する。
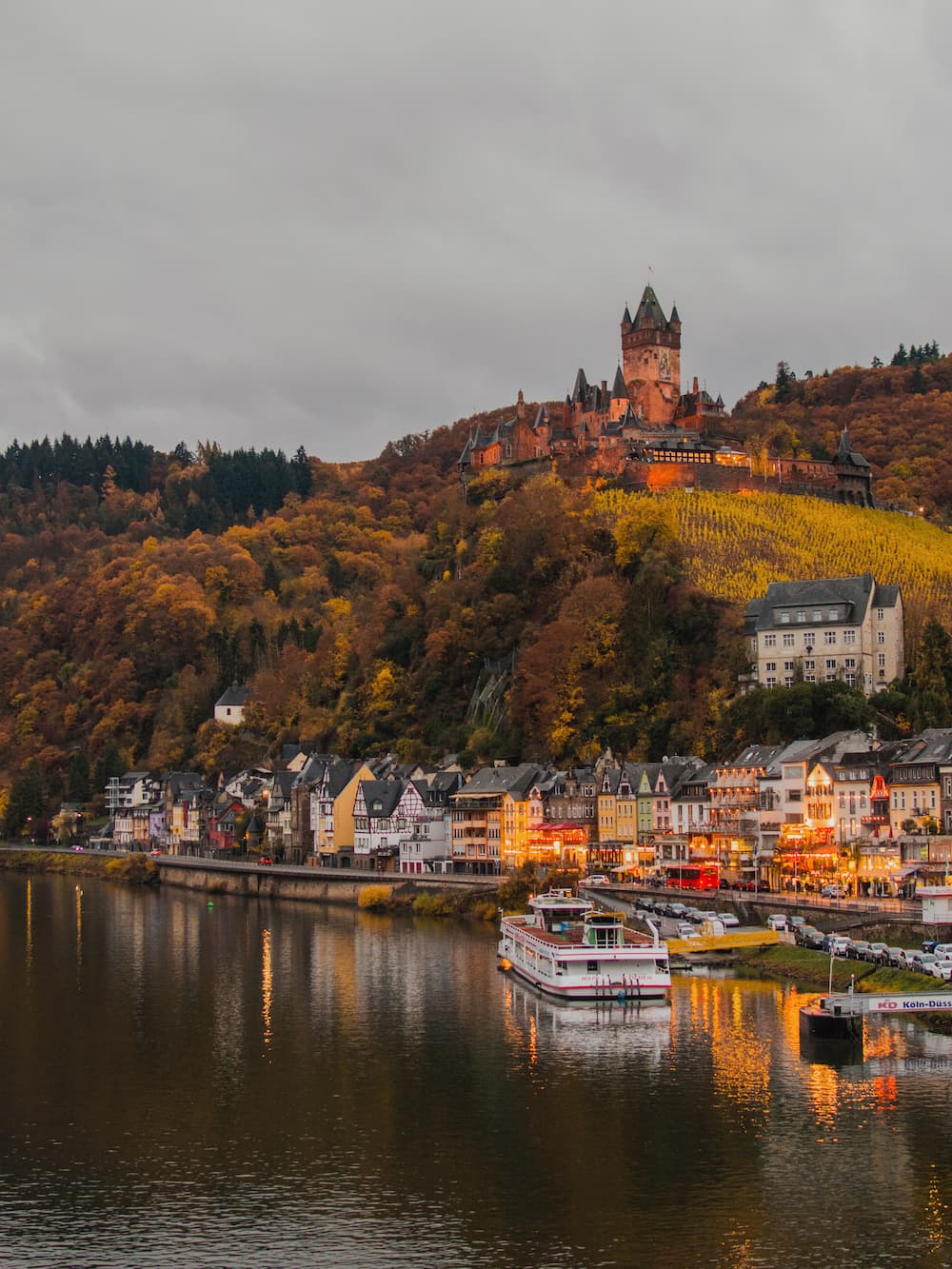
Ando Mahito
中学時代にドイツに渡航。カールスルーエ工科大学にて、機械工学を専攻の後、PhDを取得。卒業後は、シーメンス社やボッシュグループにて、プロジェクトマネジメントおよび経営企画、社内コンサルティングに携わる。
現在では、株式会社レクサー・リサーチ、フラウンホーファー財団IPA研究所と共同開発契約を結び、シミュレーション系最大手エンジニアリング会社と協力関係構築から生産シミュレータGD.findi のドイツ市場開拓に従事。
関連記事