- GD.findiが解決できる課題
- 製品紹介生産活動の現場とサイバー空間をつなぐ 生産シミュレーション
GD.find MS
Modeling & Simulation
ライン設計を強力に支援する完全ノーコード生産シミュレータ - よくあるご質問
- 事例
- ウェビナー
- お役立ち情報
モノづくり用語解説 | 本記事は 3分で読むことができます
製造業における平準化とは?意味から実現に向けたステップまで解説
執筆者:レクサー・リサーチ マーケティング 山上玲奈(やまがみ れいな)
無料ガイド: 製造業の現場における3つの課題を解決する基礎ガイド
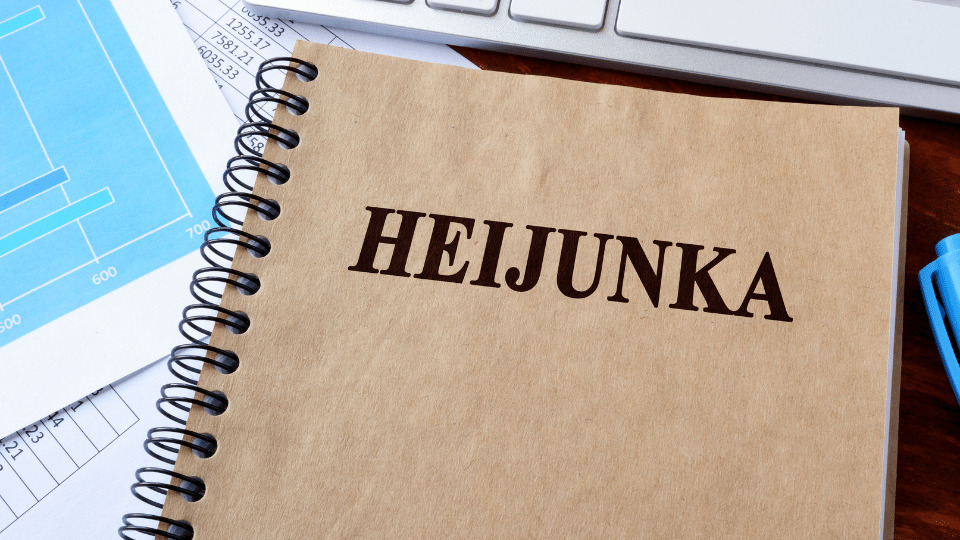
製造プロセスの平準化を考えた際に、コストがかかるのか、効果は何なのか、どの様な事をすべきなのか、と悩んでしまう方も多いのではないでしょうか。
この記事では、平準化の定義から、成功させるための重要な点や、具体例を用いた実際のステップをご紹介します。
平準化とは?
物流における平準化とは、「生産量や商品・部品種類を平均化する事。生産性(リードタイム・コストなど)を揃えることも同義」と定義できます。
では、平準化とはどのような作業に対応するものなのでしょうか。主に、平準化できる作業は、定期的に発生する作業やルーチンワークの作業です。つまり、作業の流れや行うべき作業が決まっていて、繰り返し発生する作業のことです。製造プロセスは、基本的にあらゆる箇所で平準化が可能と言える領域になります。
平準化によってもたらされる究極の目標は、「組織にとって最も生産的で効率的な仕事の仕組みを実現すること」です。
平準化を可能にする条件
どんな企業・工場でも平準化を進めることが出来る、というわけではありません。信頼でき、互いに尊敬し合える関係性を築き上げていく事が重要になります。
トヨタが平準化した企業の代表例と言えます。トヨタの歴史は長く、トヨタ生産方式と呼ばれる生産プロセスを生み出しています。これは、平準化の成功例と言えます。
2008年から2009年にかけて世界的な不況に見舞われた際、トヨタの販売台数は落ち込み、半年間で13億ドルもの損失を出し、過去最悪の四半期となりました。しかし、トヨタには自社のクルマの品質に対して自信を持っており、焦ることはありませんでした。トヨタは、自社の生産工程において、何が重要で、効率化に有効かを知っており、不況以前からうまくいっていた手順を適用し続けました。新しい、まだ試されていない生産方式を試すことはせず、従来の方法のさらなる改良を続けたのです。これは、一見すると当たり前で簡単なことに聞こえますが、経営層から現場含め、信頼関係が出来上がっているからこそ、今までの方法を否定することなく、更なる改善を続けていく方針を迷うことなく選択できたのです。
そして「ムリ・ムダ・ムラ」をなくし続けて、生産工程を平準化することができたのです。
平準化が進まない理由
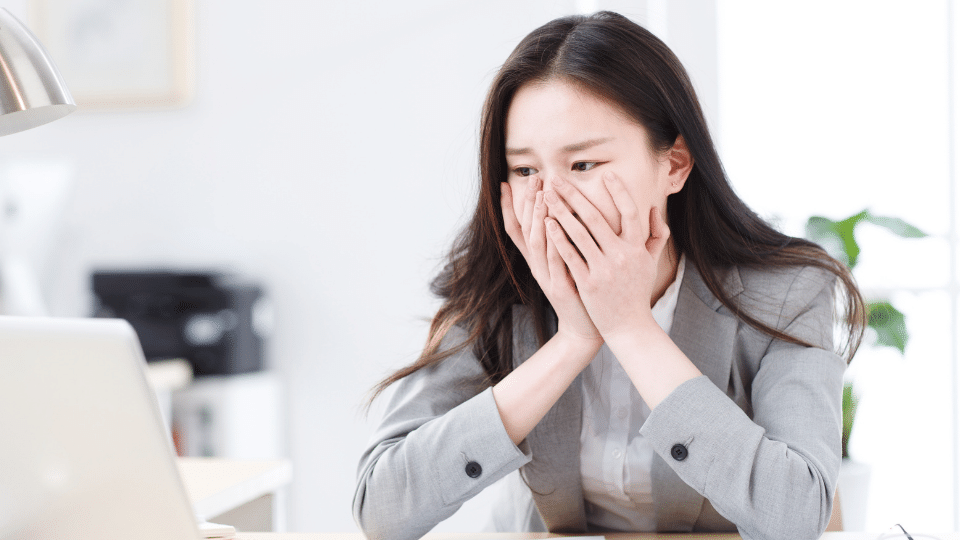
平準化した結果、生産が楽になり、コストも下がることは、分かっている一方で、平準化を実施するハードルは、手法によって様々です。平準化のための考え方として、IPF(Individual Piece Flow)、セルラー生産、リーン生産(LPS)などがあります。現在、製造工程の平準化に最もよく使われているのは、リーン生産方式(LPS)またはリーン生産製造方式(LPMS)です。
しかし、挙げられた手法のほとんどは、現場の作業についての詳細な知識が必要であり、プロセスにおいて様々な箇所でいきなり実施するのは難しいかもしれません。
前述したような生産方式は、製造/組立の全体的な効率を大きく向上させますが、多くの企業は、確立された生産方式を導入するのが、大掛かりなプロジェクトになってしまうことを懸念として挙げています。また、従来のプロセスを刷新するため、従業員がそれを受け入れてくれるかどうかや、新しいプロセスを全従業員に習熟してもらうためのトレーニングに参加させるために多くの時間がかかります。平準化を実現しコストを抑えたいのに、多くの資金も時間も費やす必要があるのです。
確立された生産方式は、確かに実現すれば大きな効果が出ますが、全プロセスから実施するのではなく、 まずは低コスト・小メンバーで出来る箇所から平準化していく 事も一つの平準化のやり方かもしれません。
「平準化」と「標準化」
平準化と標準化には多くの類似点がありますが、この2つの概念は製造業において明確に異なる意味を持つことに注意する必要があります。
複数の類似した商品を製造している工場において、各商品の大きさを例に考えてみます。
平準化は基本的に複数商品の全体的な形状や大きさを近しいものにしていくことです。これに対して、標準化とは、規定された寸法に対して、完成品を正確に合わせることや、そもそもの規定された寸法を定義することです。平準化は、複数商品を横並びで見た際の凸凹を均していく考えで、標準化は、商品の製造にあたって規定を定めたものに対して正確にズレなく製造できるか、という考え方になります。
もちろん、これらの概念が重なる場合もあります。例えば、パーツを水平にすることは、より精度を高めることにつながるかもしれません。
平準化に向けたステップ
製造プロセスの平準化を行うには、以下のステップで考えると効果的、と言われています。
① 平準化したいプロセス全体を分析し、可視化する
多品種生産のラインを例にとると、作業時間のうち、品種の切り替えに伴う段取り時間(製品の加工が終わってから次の製品加工に切り替えてスムーズに生産ができるまでの時間)が大きくなってしまう傾向があります。
そこで、平準化したいプロセス全体の作業として何があるのか分析し、可視化します。
ラインを稼働させている際に、実際に作業者が何をしているのか、出来るだけ詳細に分解していきます。
分解していくと、想定段階では生まれるはずがなかった時間含めて多くの時間がかかっていることが分かると思います。
例えば、1つの部品の作成が完了し、次の作成に移る際に必要となる部品が見つからず、探す時間、などもすべて分解します。
② 可視化したステップを、外段取り時間、内段取り時間、ムダ時間に分類
先ほどの例で挙げた、部品を探す時間はもちろんムダ時間になります。その他として、機械を稼働させながら並列で可能な作業(次の製品の作成のための型を準備する時間など)を、外段取り時間とします。
最後に、機械の稼働を停止させないと実施不可能な作業(型や、治工具の交換など)を、内段取り時間とします。
③ ムダ時間の徹底した削減
ここまでできれば、まずはムダ時間を徹底的に削減していきます。ここは、当たり前な工場内の整理整頓でもかなり削減できる可能性が高いです。他にも作業者の独自のやり方によって、発生していたが、誰にも指摘されずに気が付いていない場合などもあります。なので、作業マニュアルの改善や周知の徹底なども大きな効果を上げる可能性が高いです。
④ 内段取り時間の短縮
続いては、内段取り時間の短縮です。ここは、本当に機械を停止させないと出来ない作業なのか、の検証が大きなポイントになります。実は機械を稼働させたままでも出来る作業が、作業員の準備不足などで内段取り時間になっていることがあります。
内段取り時間は、リードタイムの長大化を招く要因で、工場全体の生産性に大きなインパクトがあります。 また、内段取り時間の中で、機械の調整を目視で行っているような事があれば、何らかのデジタル化によって、時間の短縮が出来ます。
⑤ 外段取り時間の改善
最後に外段取り時間の改善です。ムダがなくなり、内段取り時間も短縮されていくと、今までは外段取り時間として、機械を止めずに行えていた作業が間に合わなくってしまい、結果として機械を止めてしまう可能性があります。
そのため、他の工程で時間が余る作業者がいるのであれば、その作業者に一部外段取り時間を助けてもらえるような、動線の配置であったりを工夫して並行して出来る状態を作り出すことなどが有効です。
まとめ
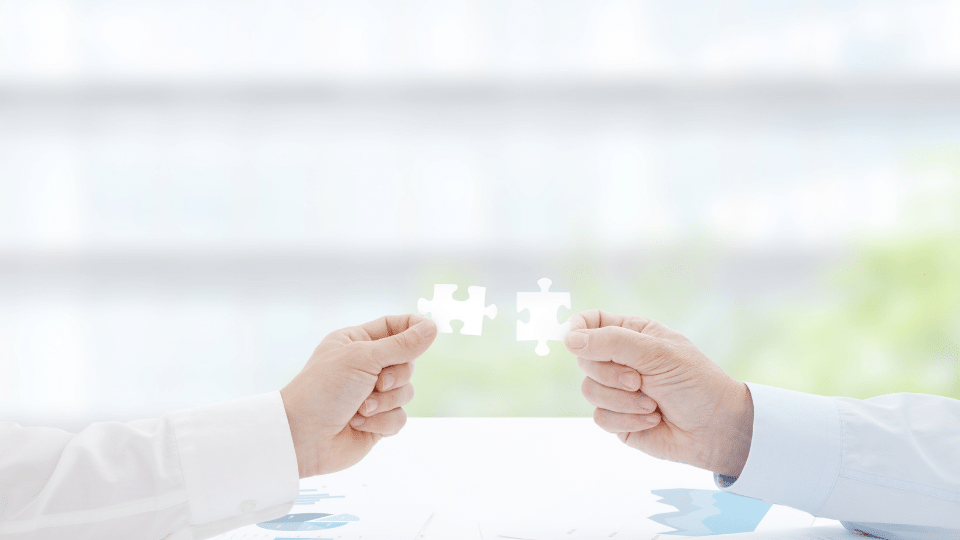
平準化というとトヨタのような大企業が多くの時間と労力を割いて完成させたもの、のように捉えてしまう方もいるかもしれません。また、体系化された平準化のための生産方式も、全工程に導入するとなると、コストがかかりすぎてしまい、敬遠してしまう方もいるかもしれません。
しかし、平準化は基本的には「ムリ・ムダ・ムラ」の削減、という製造業の大前提を突き詰めていく事で、実現可能です。まずは製造プロセスをきちんと分析して、少しでも改善できるところがあれば、改善する。それを繰り返すことで、実現することも可能です。