- GD.findiが解決できる課題
- 製品紹介生産活動の現場とサイバー空間をつなぐ 生産シミュレーション
GD.find MS
Modeling & Simulation
ライン設計を強力に支援する完全ノーコード生産シミュレータ - よくあるご質問
- 事例
- ウェビナー
- お役立ち情報
モノづくり用語解説 | 本記事は 3分で読むことができます
ジャストインタイムとは?意味から3原則など基礎から解説
執筆者:レクサー・リサーチ マーケティング 山上玲奈(やまがみ れいな)
無料ガイド: 製造業の現場における3つの課題を解決する基礎ガイド
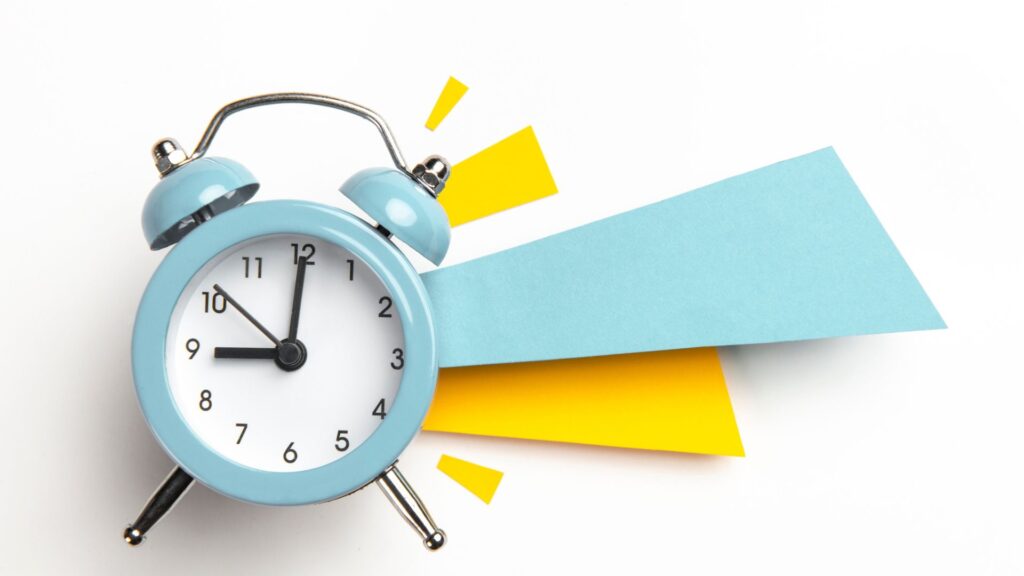
製造業において、ジャストインタイムはリーン生産の重要な実施ステップであるため基礎を理解しておくことは非常に重要です。
そこで本記事では、ジャストインタイムの基礎について解説いたします。
ジャストインタイムとは
ジャストインタイム(JIT)とは、メーカーが製品在庫を備蓄しておくのではなく、必要な時に必要な分だけ用意することを推奨する考え方です。 効率に重きを置くJITの考え方は、企業は余分な保管スペースの費用を払わずに済み、規格に合わない製品を排除できるとともに、輸送費も最小限に抑えることができます。
この考え方は、しばしば在庫をなくす考え方として紹介されていますが、これは解釈の齟齬で、実際は余分な材料の保管や輸送を避けており余剰が全く目立たないため、そのように見えるだけなのです。つまりこの考え方は先述のように効率性を強く求めているためメーカーのコスト削減に高く貢献します。
ジャストインタイムの歴史
この生産方式は、日本の自動車メーカーであるトヨタ自動車が最初に開発し、その有用性から現在では世界中のメーカーで採用されています。
ジャストインタイムという言葉は1950年代にトヨタのチーフエンジニアである大野耐一様が初めて使った言葉であるというように知られています。しかし、この概念自体は第二次世界大戦中にフォード社がB-24爆撃機を製造する際に初めて米国に導入されました。さらには戦後、同社は同じ手法で自動車などの生産を効率化するようになったというのが実際の概念自体の始まりです。
戦後の日本では、アメリカの工場は規模が大きく、資源も豊富なため、競争に勝てないことに気づき、在庫を必要な分だけ生産するシステムを開発しました。これが結果的に、日本での最初のジャストインタイムの始まりとなりました。
ジャストインタイムの広まり
先述のようにJITはこの原則を他のビジネス分野、特に物流やサプライチェーン・マネジメントに応用することで、収益性を向上させることを目的としているのです。
そして自動車製造での成功を受けて、JITの原則は医療、小売、接客業など他の産業でも採用されるようになりました。マクドナルド、クライスラー、ウォルマートなどもJIT生産方式を採用しています。例えば、食品を一日中冷凍庫に眠らせておかないために、開店直前の朝に仕入れを行ったり、衣料品を余らせないために、注文が入ってからすぐに作ったりすることがこれに当たります。
ジャストインタイムの3原則
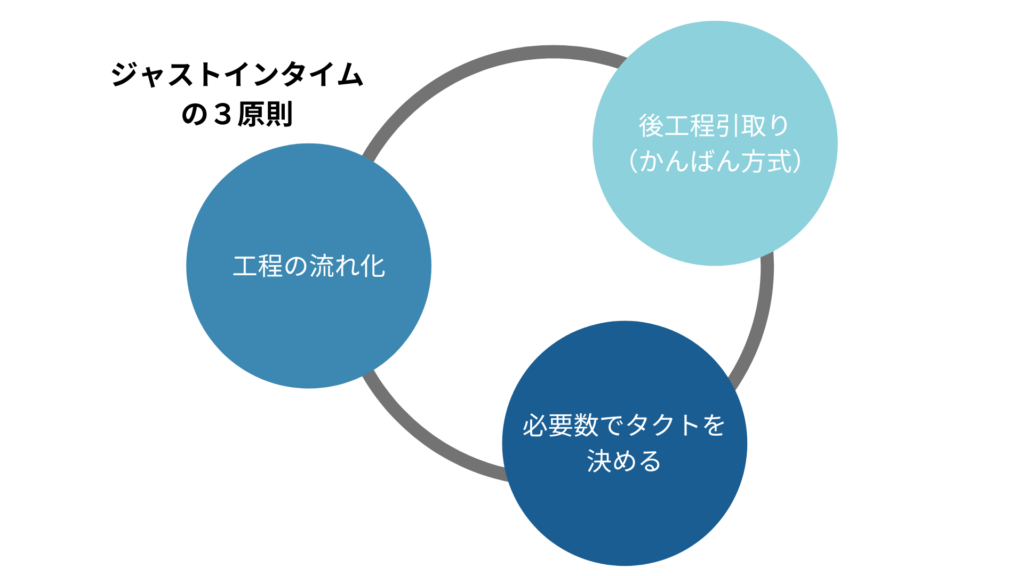
ジャストインタイムには、以下の3原則があります。
- 後工程引取り(かんばん方式)
- 工程の流れ化
- 必要数でタクトを決める
後工程引取り(かんばん方式)
後工程引取りとは、工程が前工程から必要なものを必要な時に必要なだけ取り出し、前工程は取り出された分だけ生産することであり、かんばん方式とも言われます。
後工程引取りの目的としては、”製造側の都合を排除し、クライアントへの販売時点からスタートすること “などがあります。
工程の流れ化
工程の流れ化としては、工程間でモノを滞留させないことや余分な在庫やバッファを蓄積しないといったことがあげられます。
工程の流れ化の目的は、細く速い流れで製品を作ることであり各工程はバッチで生産し、仕掛品がどこにも滞留していないことが必要です。
そのため、一個流し生産や小ロット生産を実行し、滞留や停滞をなくすことが重要で、プレスや鋳造などの切り替えを伴う製造工程においては、段取り時間を短縮し、大量生産からの脱却を目指すことが必要です。
必要数でタクトを決める
必要数によるタクトの決定は、生産する個数から逆算を行うことで求められます。タクトタイムとは、稼働時間を必要生産数で割ったものです。
この式で示されるタクトタイムで製品を作るということは、必要な作業者の数が少なければ、少ない数の製品を作り、必要な作業者の数が多ければ、多い数の製品を作ればよいということになります。
最小人数でラインを作る
固定人数で生産を行う方法は、需要が少なくなった際に余分な生産を招きかねません。つまり、必要最小限の人数でラインを設計することがポイントとなります。
過剰生産によるムダを排除する
計画通りに生産した場合、実際に必要な生産量が計画した生産量より少ない場合に「過剰生産のムダ」が発生します。一方で、実際の必要数が予定数よりも多い場合は、計画通りに生産すると欠品の恐れが出てしまいます。
過剰生産のムダや欠品のリスクを最小限に抑えるためには、販売に追いつくだけの柔軟性が必要です。逆に言えば、売れ行きに応じて柔軟に対応できる最小限の人員でラインを構築することが、ジャストインタイム生産には重要なのです。
売れ行きを把握し、それに応じた生産計画を立てることで、過剰在庫や欠品のリスクを抑えることができるのです。
ジャストインタイムの狙い
ジャストインタイム方式の目的は、最も効率的かつ効果的なプロセスに依存することで、コスト、無駄、余剰在庫を最小限に抑えることにあります。
そのためには、在庫の必要性を把握し、不要な生産物や材料を排除するということが必要です。そして、ワークフローを合理化し、ボトルネックをなくすためにサプライチェーンの計画を可能な限り正確に立てます。そうすることで無駄を省きながら効率を最大化するワークフローが実現します。
ジャストインタイムの効果
JITの効果としては、コスト削減、品質管理、納期、安全性、顧客満足度、スペースの効率化など、さまざまな面で改善が見られるでしょう。
コスト削減の効果としては、過剰生産や不良品の発生を防ぐことができるほか、長期間使用されない余分な在庫をなくすことで、保管スペースを最小限に抑えることができます。さらに、JITの特徴である不良品の早期発見により、不良品を大量に廃棄したり、備蓄したりする必要がないため、生産コストと在庫コストの両方を削減することができます。
まとめ
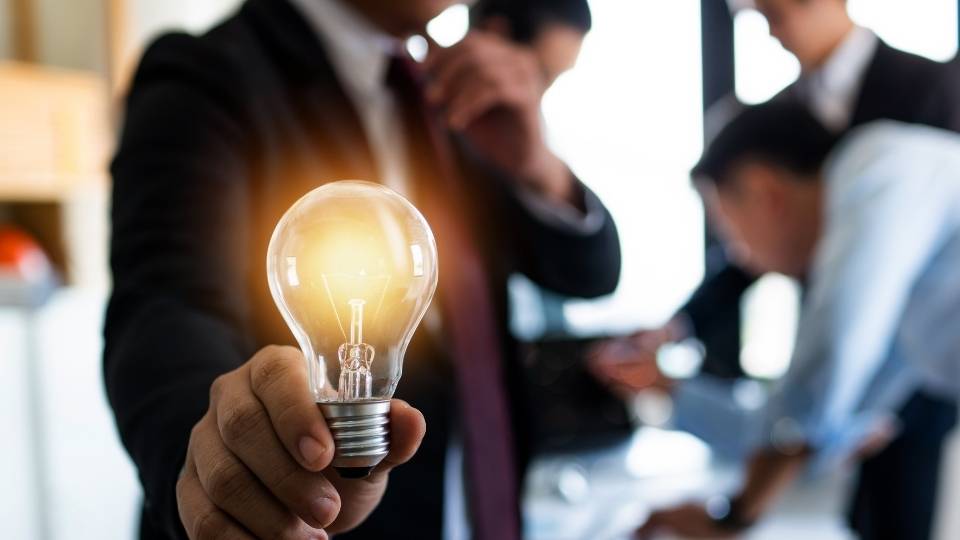
この記事では、ジャストインタイムの意味からその効果まで解説しました。
ジャストインタイムを一言でまとめると
“ジャストインタイムの目標は、各工程で無駄をなくすこと “
また、ジャストインタイムはトヨタに代表されるような車業界だけではなく、他業界でも活用できるコンセプトであるといえます。