Case: Phase One Japan Inc.
- Home
- /
- Newsroom
- /
- case
- /
- GD.findi MS
- /
- Phase One Japan Inc.
Phase-One Japan forms a consensus through Simulation to Implement Business Revolution.
Phase One Japan is the Japanese subsidiary of Denmark-based camera system company, GD.findi was introduced as a simulation to reduce lead time in high-mix low-volume production. By promoting operational reforms with the agreement of the production site, the company shortened the manufacturing lead time from 28 days to 10 days and reduced the factory inventory by 30%. Using this know-how, the company is now expanding its business.
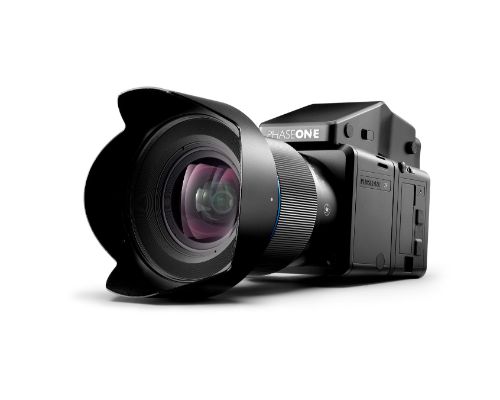
Use Simulation to provide convincing indicators.
The main product of Phase One, is high-end medium format camera systems for professional photographers. The company inherited the optical business of Mamiya Digital Imaging and has been manufacturing lenses and cameras at its production plant in Nagano. “Our strength is our high quality product. We also have the advantage of having a production base in Japan, which allows us to provide prompt service after-sales” said the Plant Manager Mr. Eiji Ibuka. The company also gained a positive reputation from professional photographers for its reliable high quality and quick response.
However, the company has faced some challenges. As a manufacturer with a long tradition, there were many craftsman-like technicians in the field, and it took up to four weeks to complete a product, and the company had a large inventory of work-in-progress and finished products. In order to increase the flexibility and productivity demanded by the head office, it was necessary to shorten the lead time and reduce the inventory.
“There were about 500 kinds of products made in small lots, and the number of pieces ranged from 1 to 3,000, therefore the production orders were extremely complicated. Every morning, the factory manager would write down the production plan for the day on the whiteboard, but due to changes in delivery dates and sudden orders, the plan was repeatedly rewritten, and by evening, it was so confusing that no one could understand what was written.” said President and Representative Director of the company.
It was in 2017, three years after the launch of Phase One Japan, the company made the decision to undertake a major operational reform. “We approached several companies that provide solutions for production innovation, we gathered information, and considered who to partner with,” recalls Mr. Ibuka. As a result, the company chose to partner with Lexer Research the provider of GD.findi, a production simulator.
“In order to involve the shop floor and promote both awareness and operational reform at the same time, we needed a consensus that everyone could understand. In this respect, GD.findi allowed us to visually see the effects of improvements and to quantify the optimal solution based on simulations and set it as a KPI. Also, I felt that the employees were familiar with the field and would take our problems as their own,” said Mr. Ibuka, explaining why he selected GD.findi.
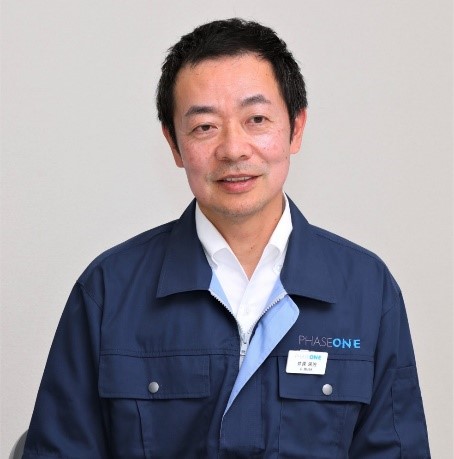
Improvements and production optimization methods identified by simulation for procurement.
The implementation of GD.finid began in the spring of 2017. A “Production Innovation Team” was formed within the company to corporate with Lexer Research. “The Production Innovation Team consisted both business system staff and manufacturing process staff to reflect the thoughts on manufacturing side. We started with four members and increased the number to nine at the peak of the project,” said Mr. Ibuka. While receiving a lecture from Lexer on GD.findi’s functions and ideas for improvement, the actual work was done by the members of the production innovation team. After one year and three months, we repeatedly ran simulations on the layout of the production floor, the allocation of people and equipment, and the configuration of the supply chain.
Specifically, we input data such as layout, process, number of people, parts, etc. into GD.findi rendering (simulation), and then confirmed the next decision from the results to controlled the process. From there, it became clear what needed to be changed in the conventional way.
The first thing that came to light was the need to improve the supply chain. As a result of our test of what needed to be changed, we found that we needed to review the subcontractors that we had outsourced the lens manufacturing process. The only way we could get closer to our goal in the simulation was to re-test between internal and external production,” said Mr. Ibuka.
We also pursued a floor plan that would allow us to achieve our target lead time. This involved a major change in the production system in the factory. The factory had been producing all products in lots, but it was necessary to switch to single-unit production, where one worker is in charge of multiple operations and assembles many products into finished products.
At the same time as making major changes to the floor plant layout, we switched 10 out of 13 lens models that had been produced in lots to single-unit production. I think it was a bold change,” said Mr. Ibuka.
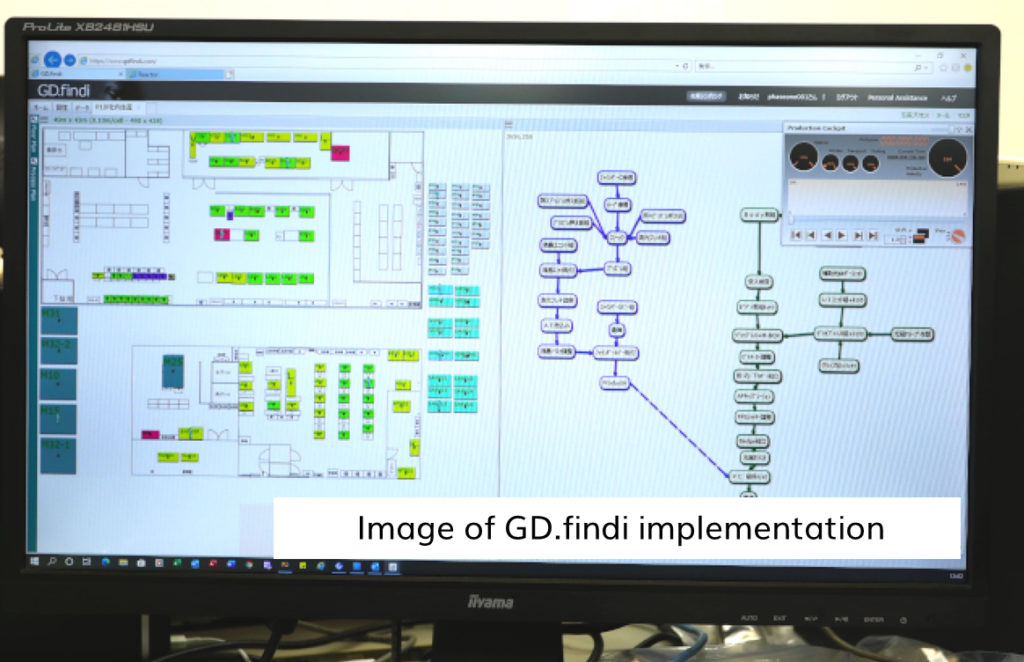
Use simulation to shorten manufacturing lead time and reduce inventory.
Based on the possibilities and feedback obtained from the simulation. The first thing was to set a goal of shortening the lead time of products from 28 days to 10 days and reducing the number of inventory items in the factory by 30%. Although this was a high goal. “We were confident that we could achieve it by managing indicators based on KPIs from the simulation. That’s how much confidence we had in GD.findi” said Mr. Ibuka. In addition, GD .findi was able to help out members to build consensus in the field. GD.findi is an system that is easy to use for the people in charge in the field. While it has its own logic behind it, the simulation can be done by using its own terminology. It is the kind of tool that can change the workplace by the people in charge themselves,” said Mr.Ibuka.
Since GD.findi is a tool that is familiar to the people on the shop floor, it proved to be very persuasive when we switched from in-house production and lot production to single-unit production. “We were able to persuade the shop floor in a logical manner because we knew the effects of using GD.findi for in-house production and production method improvement.
All of these business reforms were based on the results of GD.findi simulations. By implementing GD.findi solutions, the company was able to reduce the lead time from 28 days to 10 days and reduce the number of inventory items in the factory by 30%, just as the simulation showed.
GD.findi has also proved effective in other ways. “The front line is now able to think flexibly and not be afraid of change. We have found that there is a lot to gain by changing the conventional way of doing things, and the awareness of the people in charge of the field has changed as they have gained success in implementation.
Showed improvement to head office and be entrusted with digital camera back contract.
After GD.findi had achieved a great success in reforming the company’s operations to reach everyone’s expectation. The company was now ready for the second act of the project. The company’s head office had been working on the assembly of digital camera backs (electronic image sensor) for some time, and there was a proposal to transfer this work to Japan.
“If we work on the digital camera backs, we will be able to manufacture the entire digital camera system. We knew that there would eventually be a limit to what we could do with just the camera itself, and we felt strongly that we had to do it as the core plant of the Phase One Group” said Mr. Ibuka.
However, it was not enough to simply say “I want to do it. It was necessary to show head office that whether there would be any problems in purchasing parts, and whether the manufacturing process could be reliably controlled, and what advantages the transfer would bring. This is also where GD findi comes into the game.
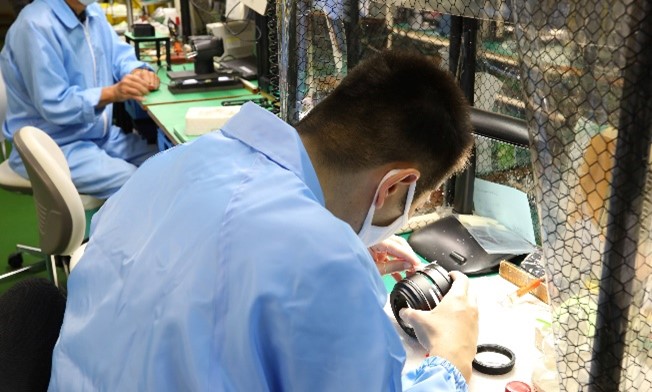
The company made a presentation to the head office based on its experience of formulating an optimal production plan and clarifying the direction of the company from parts purchasing to manufacturing process through GD find. We were able to convince the head office by showing them the logic behind the improvements, and we were able to use our experience in simulating lens manufacturing,” said Mr.Ibuka.
After successfully obtaining the agreement from the head office, the transfer of digital camera backs production was completed in 2019, allowing Phase One Japan to add a new production category. GD.findi has become a powerful simulation engine to transform management and production.