Verification of "One-piece Flow Production"
Verification of "One-piece Flow Production"
( Company D's Case )
Introduction – Conveyor belt removal and misinterpretation of a production cell's capabilities
At some point in the history of production innovation, common practice was to remove the conveyor belts running through facilities and to replace them with a small number of manned workstations of W900 x D600 size. This was deemed the era of “cell production”.
Mass production became a thing of the past, LCA (Low Cost Automation) was considered and adopted almost immediately, and each cell was outfitted with simple tools and jigs.
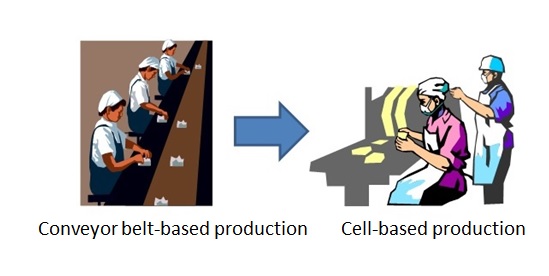
The Waste of Over-production
In an ideal realization of this process, there would be an invisible conveyor belt running between these cells, providing some sort of communication as well as ensuring that each product is produced one at a time.

Process Segmentation, Cell Specialization, and Insufficient Staff Utilization
Comparison of Models Using GD.findi
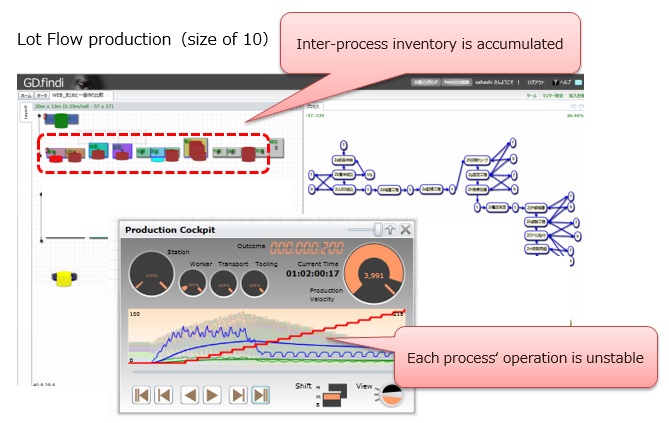
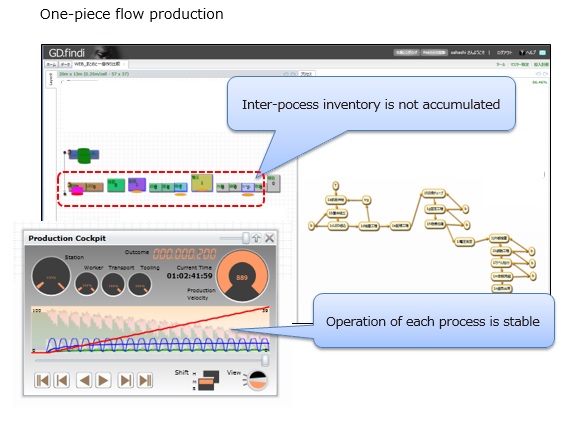
Verification and Quality Control in Production Simulations and Supply Chain Management
The factory managers of Company D, upon making the comparison between these two production models, naturally considered the problem of product quality and how changing to one of these models would influence it. The ability to understand the problems within a previous production phase will surely aid in minimizing damage in future iterations. For instance, if a defective part has been produced by some intermediate phase and its existence acknowledged, this knowledge can be used to aid in quality control screening of the final product. In addition, because all of the work-in-progress is handled by a smaller number of workers, it is a simple matter to halt production, resolve any quality problems that may arise, and then resume production at a whim. In “Lot flow production”, because supply generation must be done quickly, the limiting reagent in the production process is in the part delivery phase. A consequence of this is that the lead time in the supply chain is lengthened. ~Supply Chain Management~ In the context of lot flow production, requires that supply generation be done quickly. As the limiting reagent in the production process is in the part delivery phase, a consequence of this is that the lead time in the supply chain is lengthened. Furthermore, if raw material supply is carried out in-house and the size of a customer’s order is small it becomes possible to perform an express delivery of the final product. The link introduced by such a customer enables application of SCM through a virtual conveyor-like construct, and draws attention to members created during the production simulations. ~Unevenness of Production~ “One-piece flow production” as the advantage of creating an instance of the product soon after the start of production. Although the point in time where the final product is produced is somewhat late, this procedure’s forte is that it completes units at a relatively constant rate enabling accurate prediction of lead times. On the other hand, “Lot flow production” is characterized by some unevenness in the work quality on a day-to-day basis. This knowledge is known ahead of time, regardless of the skill of Company D’s workers brought into the equation.
The Effect of "One-Piece Flow Production"
In “One-Piece Flow Production”, the product creation phases are visible clearly, and the first product is completed in a relatively short amount of time. This characteristic allows for the designer to see the product and provide input for future iterations of the product without incurring excessive expenditure.
In addition, the same types of inspections can be made by management from a very high-level position regardless of their manufacturing proficiency to pick out “coarse” problems and smooth them out. This will lead to sustainable improvement, as any individual involved in the process will be able to provide input and implement those changes rapidly.
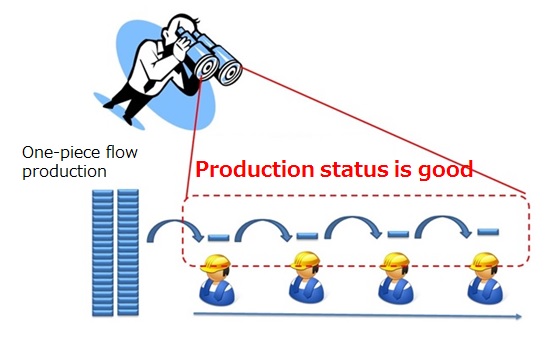