Transport system design with transport workers and autonomous devices (AGV)
- Home
- /
- Best for You
- /
- Transport system design with…
1.Major issues in transport system design in manufacturing
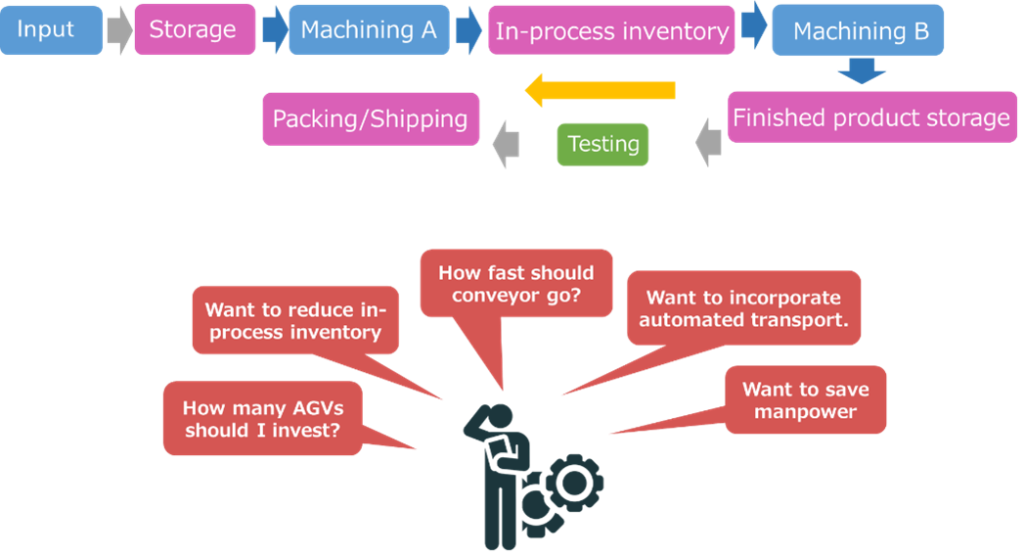
As we all aware of the evolution and transformation of production lines and production systems has brought many innovative technologies into the manufacturing industry, for example:
- Sensor technology (not only devices but also image analysis and automatic identification, etc.)
- Material handling technology (automation through the evolution of robot systems)
- Transportation technology (autonomous AGV, etc.)
We are sure that many production sites are familiar with the above but here, we would like to introduce the transportation technology which has a significant impact on the evolution of production systems.
Conventionally, the work and time involved in the transport design have been positioned as “incidental work” with non-value-added time, and production sites have been searching for kaizen activities to reduce the time by streamlining the flow of goods, one-way flow from input to shipping, layout kaizen, and automation of internal setup of equipment, etc. Namely, the final purpose of these ideas is to reduce non-value-added time by integrating a series of improvement activities in the process of goods.
Nowadays, transport technologies such as AGVs and other transport devices are becoming popular options to improve transport efficiency and reduce the number of transport workers. Therefore, in the future, capital investment in automatic transportation, multi-function machining to shorten the lead times and reduce costs will be the new trend in the manufacturing industry.
For this reason, the challenge for most production managers is whether it is possible to design a production system that allows production processes and the flow of goods to proceed in harmony with minimum stagnation. To be specific, it is essential to have the necessary materials in the right place at the right time, as well as the ability to respond to unforeseen circumstances to avoid delaying production.
However, it is often difficult to adequately design the right systems for the problem. The reason is that it is almost impossible to design a system for static production activities and dynamic transportation activities with a comprehensive perspective manner without the help of technology. For example, with the implementation of AGVs, although it is possible to verify travel routes and evaluate throughput using AGV-specific simulators, it is difficult to comprehensively evaluate the flow of goods in the production process. On top of that, the more sophisticated and autonomous AGVs become, the greater the deviation it has with the production line. It is not easy to find the optimal number of AGVs for your production line, and as a result, you may end up implementing too many AGVs.
I am certain that many of you have experienced the difficulty of deciding how many AGVs to use, at what intervals, and even how to set the upper quantity limit for transportation, regardless of whether it is basic transportation at Scheduled Quantity, Unscheduled Time Conveyance or Scheduled Time, Unscheduled Quantity Conveyance (see figure 2.). Especially, the importance to design and evaluate production lines and transport systems in an integrated manner to maximize the productivity of the transport system has been dramatically increased in recent years.
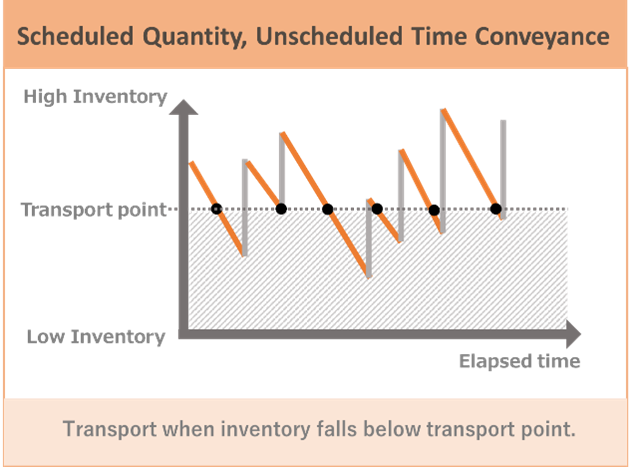
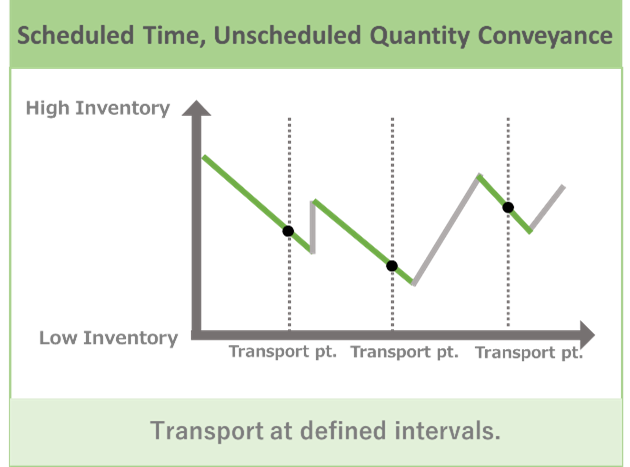
2.The approach to transport system engineering with no-coding platform.
A static production system design is often facing trouble with transport control, especially for AGVs that operate autonomously. That is, it cannot be evaluated in a fixed flow such as on a work combination table or chart diagram. The reason is that autonomous transport systems follow their logic and change the behavior and actions according to the current situation.
To deal with this problem, an effective approach is to place autonomous transport devices as an object in virtual space and associate it to the production process to evaluate its behavior comprehensively.
Therefore, by using GD.findi’s virtual factory, it allows you to define the transport route and associate it to the production line to verify if the transport system operates as planned and determine the specs of the transport system.
For example, you may want to draw a route according to the floor design of your site and verify the differences in the design of the arrangement. in GD.findi, these transportation settings can be done with a no-code platform with only on-screen operations.
As shown in the figure 3&4, it is possible to see how the design of the transport routes affects the design of different layouts, which is very useful for designing transfer operations.
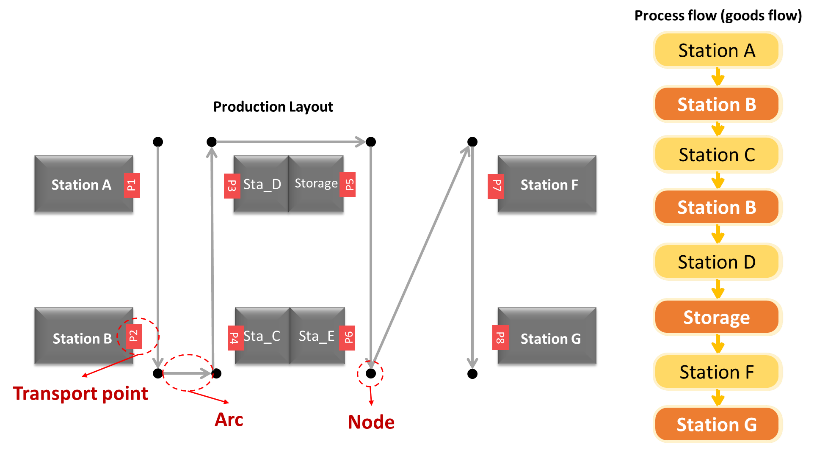
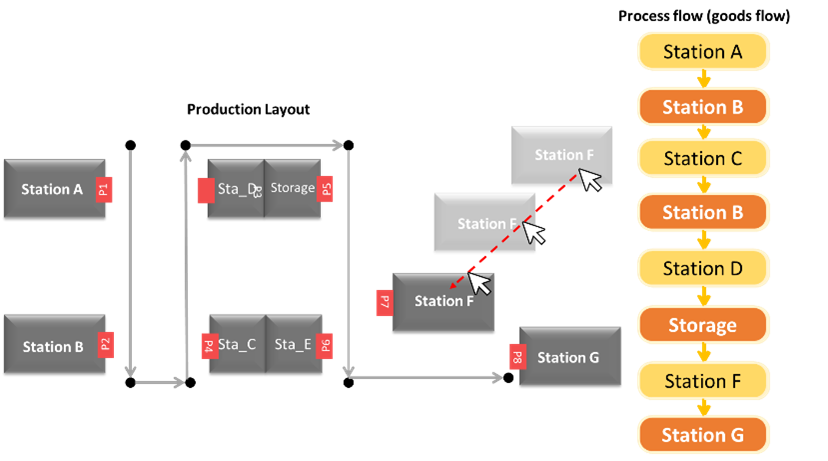
3.Virtual representation of transport system
As we have discussed so far, transportation behaves dynamically, so the design of the production system must be carefully considered. For instance, it is impossible to observe the large-scale flow of materials if we only pay attention to the details, nor can we verify the detailed performance if we only focus on the large-scale flow.
Thus, an effective design method is to start with the big picture, and then narrow it down step by step to the detailed design.
The basic idea to keep in mind with this method is that the transport system is designed to handle the logistics between workstations (i.e., facilities and locations where production takes place), but the transportation itself acts as a constraint. It is important to design a good production system considering the manufacturing activities that generate product value with minimal loss.
Based on this concept, you can use GD.findi in the following steps to efficiently and rapidly complete the design of your transport system.
1 Design a production system without specifying the transport system.
GD.findi allows materials to flow from one workstation to the next workstation even without having to explicitly set up a transport system. In this case, the transport time can be set to zero or a fixed value. This allows us to check and find the maximum capacity of the production system without transportation which was considered as a constraint. (See GIF1, the colorful circles indicate parts, and the square blocks indicate workstations: equipment)
2 Add specifications to the transport system.
By setting up "agents" between workstations, the behavior of the transportation is controlled by the abilities of the agents, and the production system operates with transportation activities. Here, since GD.findi has various agents available, we will proceed to examine what kind of transport style is suitable by switching agents. (See GIF2, a worker agent is performing a transport operation.)
3 Set up the routes and conditions in which the transport system will operate.
Next, it is possible to set more detailed conditions for the agent's behavior:
- Set up transport routes.
Routes are set on the layout for the transport agents to travel through; The agent will autonomously select the shortest distance.
- Set up parameters for transport agent.
Number of units, travel speed, loading/unloading range, etc.
Through these steps, the conceptual design of the desired transport system can be efficiently and effectively implemented.
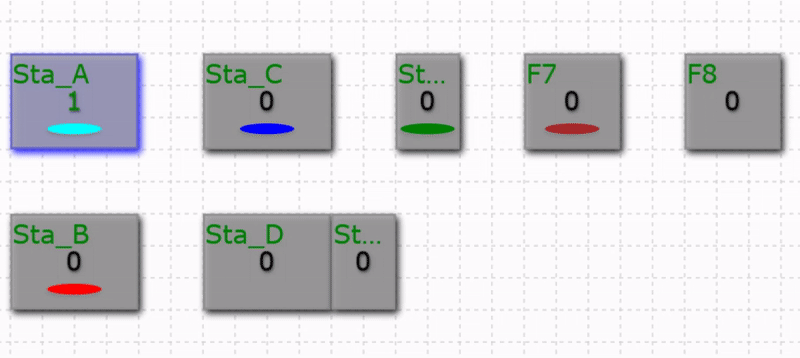
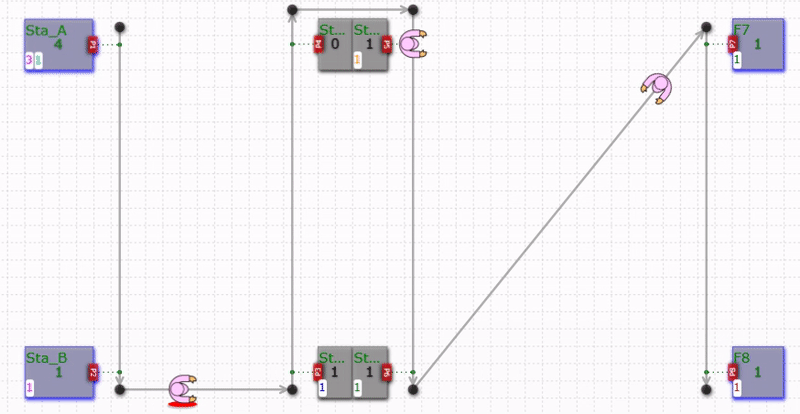
4.Agent library provided by GD.findi
Now, we know that it is effective to use “agents” when designing such a transport system. GD.findi has a variety of transport agents with different capabilities, such as tow truck, passage-designed worker, AGV_scheduled, etc., which are available on GD.findi’s “Agent Library”. Depending on the design of your production system, you can choose the right agent for your production line.
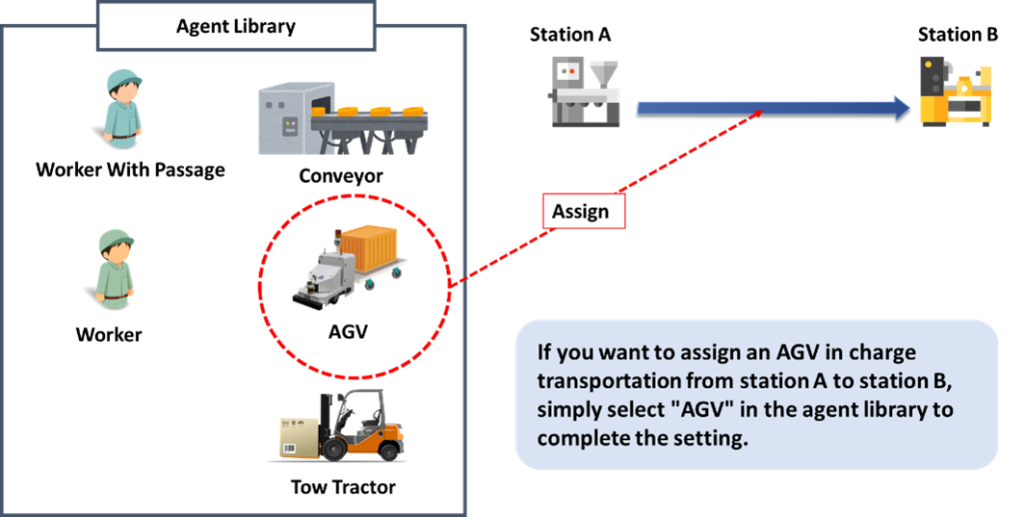
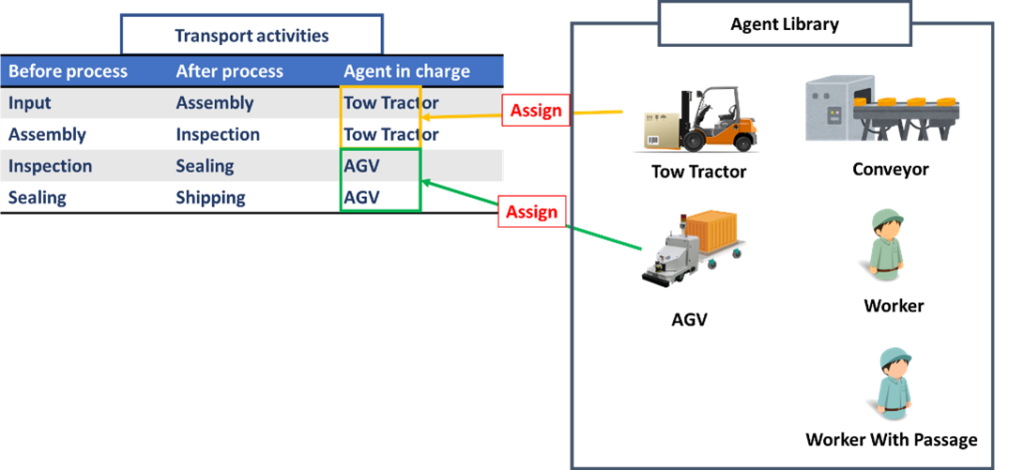
5.Transportation system design evaluation (material flowchart)
Next, let us take a look at how to evaluate the quality of a transport system. One of the features of GD.findi is its data analysis technology using “Material Flow Chat”. Material flow chart is a function that graphically displays the progress and agents (e.g., transport operator) flow after the production rendering (production simulation). The operational status of stations and transport operations is displayed in a Gantt chart, and the travel time within and between stations is displayed in a pop-up window when the mouse is pointed at it.
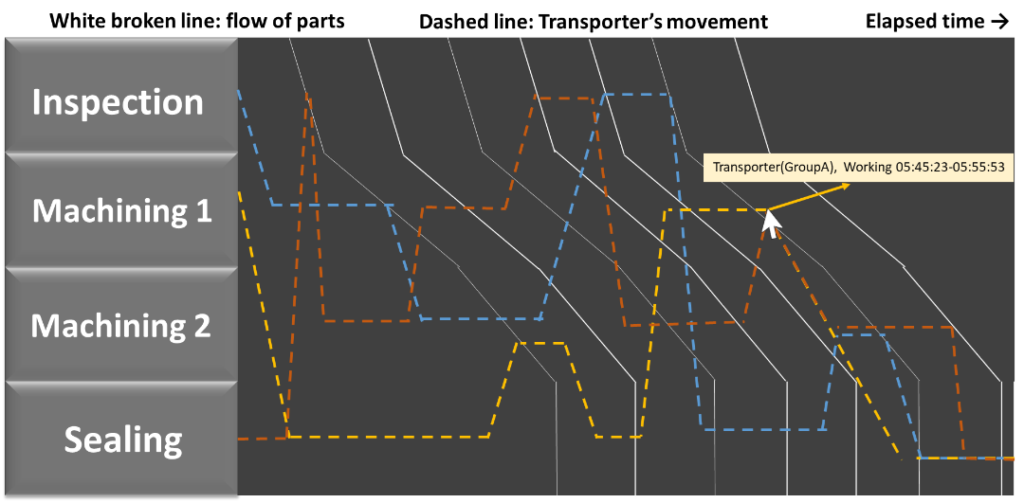
6.Practical example: Determine optimal transport assets (AGVs) using agents.
Determining the optimal number of AGVs in a production system when there are multiple transport operations is not an easy task. If the number of AGVs is low, workers will have to wait on the machine side, causing the process to stop and resulting in losses such as an increase in in-process inventory. GD.findi can simulate such a situation to find the minimum number of AGVS that gives the best outcome. For example, if you want to achieve a production target of 64 units and an AGV work rate of 85% or less, you can run a simulation with 1 to 5 transport agents and compare and analyze the results. (See Table 1)

By graphing the data, we can see the optimal number of AGVs for the production line.
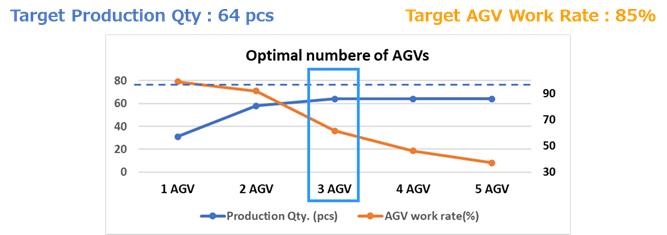
In this example, the number of AGVs that achieve the production target is three or more. However, increasing the number beyond three does not increase production. This means that increasing the number to four or more is a wasteful investment.
As a result, we can say that the number of AGVs that will achieve the target production number and result in the lowest investment is 3 units. In such manner, the transport agents can be used to optimize the design of transport tasks with complex behaviors.
So far, we have explained the concept of transport system design. We have also prepared a “GD.findi Engineering Recipe” to show you how to solve specific problems in this topic.
If you are interested, please do not hesitate to contact us.