The optimal number of in-process inventory
- Home
- /
- Best for You
- /
- The optimal number of…
1. Challenges and common issue toward inventory management
In the manufacturing industry, inventory management is a common issue in operations. There are always conflicting risks such as overstock and shortage. As known, maintaining inventory is one of the key factors for sustainable business management as it causes cash flow to decline, destroying the balance sheet and putting pressure on capital. Therefore, it needs to reduce the inventory in the production department, and most of the time the inventory is strongly urged to be reduced.
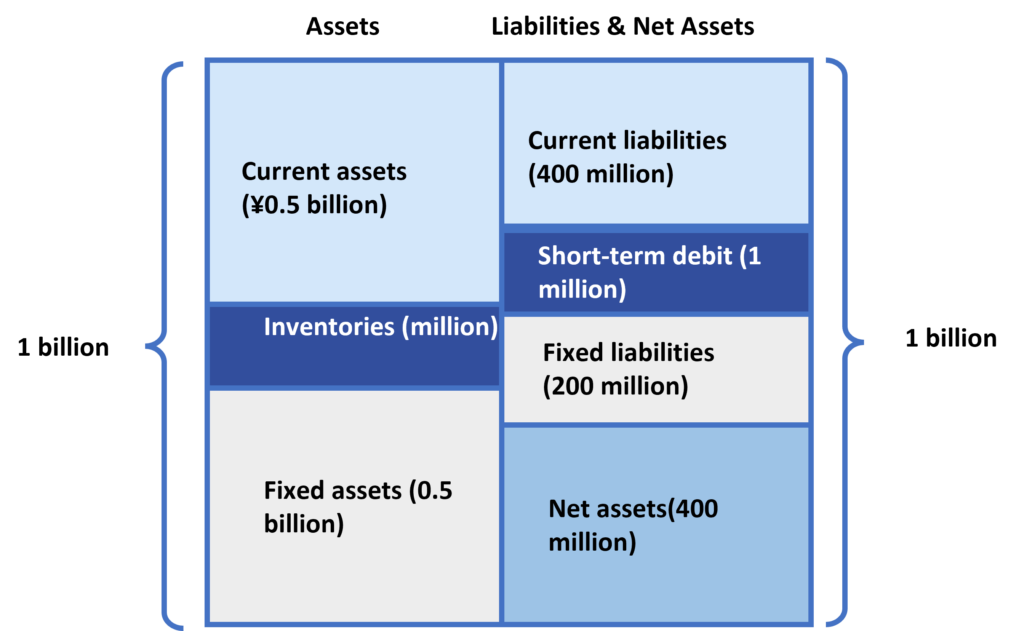
In manufacturing, especially in the production control division, they plan to minimize the supply of materials based on the shipment plan. Here, fear of shortage risk leads to excess inventory, while fear of overstock risk leads to shortages. The key to inventory management is to continuously maintain the relationship between these conflicting elements, but this is never an easy undertaking.
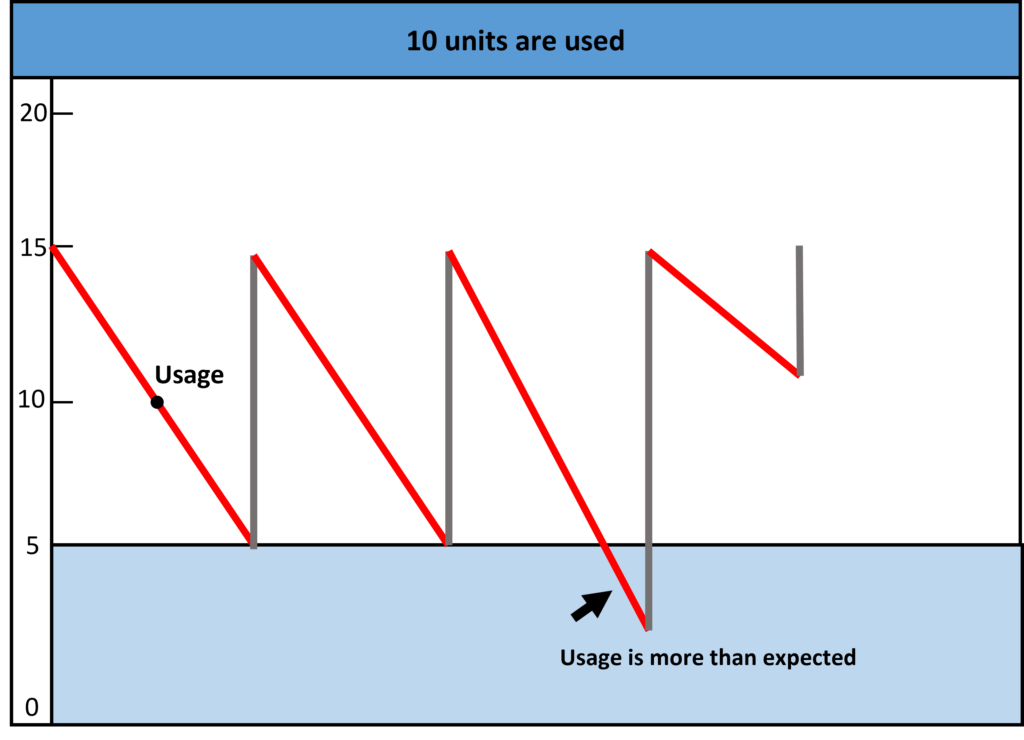
When looking at the issues that need to be resolve in inventory management, we should focus on finding a control system that can correspond with the change of time instead of paying too much attention to operational efficiency. Below is a list of issues manufacturers face when finding an inventory control system.
- Don’t know how to set up a standard inventory
- Achieve proper control of inventory to respond to market fluctuations (reduce excess inventory)
- Make inventory management something that anyone can implement
- Threatened by the large amount of inventory I inherited from previous generation.
So how should we seek solutions to the various problems associated with inventory management?
2. An approach to problem-solving in inventory management
The reason behind the difficulty in setting standard inventory is that it has become rather difficult for “human intuition and experience” to predict changes in product inventory between variations in production volume of each process due to the inability to follow the production plan and the shipping plan set by the demand side. In the past, when there were only a few varieties of products, or when the ordering system and specifications of a particular customer were known, production managers who were familiar with the field would detect these variations and hold the appropriate amount of inventory. However, product types have increased, the number of users has increased, and the demand for shipment requests from customers has changed in various ways. In this situation, the only way to avoid the risk of shortages is to keep more inventory on the safety side, and therefore inventory has the tendency to increase.
Additionally, since inventory control is an issue that catches everyone’s eyes, it is easy for managers, who do not understand the situation at the production site, to point out that the inventory is excessively high. But even if it is the minimum required inventory, it is difficult to explain quantitatively why this level of inventory is necessary here.
The only approach to solving this problem is to foresee inventory changes. What we would like to propose here is a virtual experiment using a simulation. If you can’t figure out what the appropriate standard inventory is, i.e., how to minimize the risk of overstocking and shortages, and how to run the inventory efficiently… An effective way is to “Try” using simulations.
Incidentally, there is also a way to reduce inventory by using “withdrawal Kanban,” but it is limited to the internal control range of the organization, and if Kanban is used when there are many product types, it will not indicate the appropriate Kanban selection, which increases inventory.
Assuming that each process in the manufacturing swings in response to the production plan and shipping plan swings based on the demand hypothesis, we can confirm where shortages and overstocks occur. And repeat the experiment. By using simulations, we can take a big step toward achieving optimal inventory management. In other words, designing the actions that your company should take with plans that assume variation is the key to solving the fundamental problem.
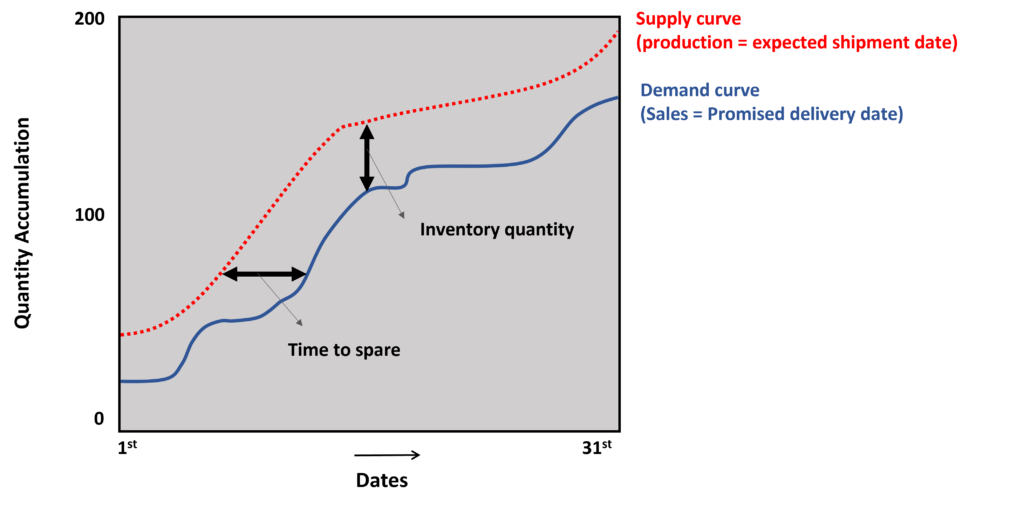
3. "Visualizing" in-process inventory in GD.findi
Inventory changes are determined by the relationship between the production plan, shipping plan, and the production flow in each process, and there is a cause and effects between “inventory shortage leads to high risk of waiting and short supply” and ” excessive inventory leads to loss of cash flow”. It means that the amount of inventory should be maintained at an optimal level, neither too little nor too much. To determine safety stock and proper inventory as the optimal amount of inventory, it is necessary to monitor changes in the inventory situation under various circumstances.
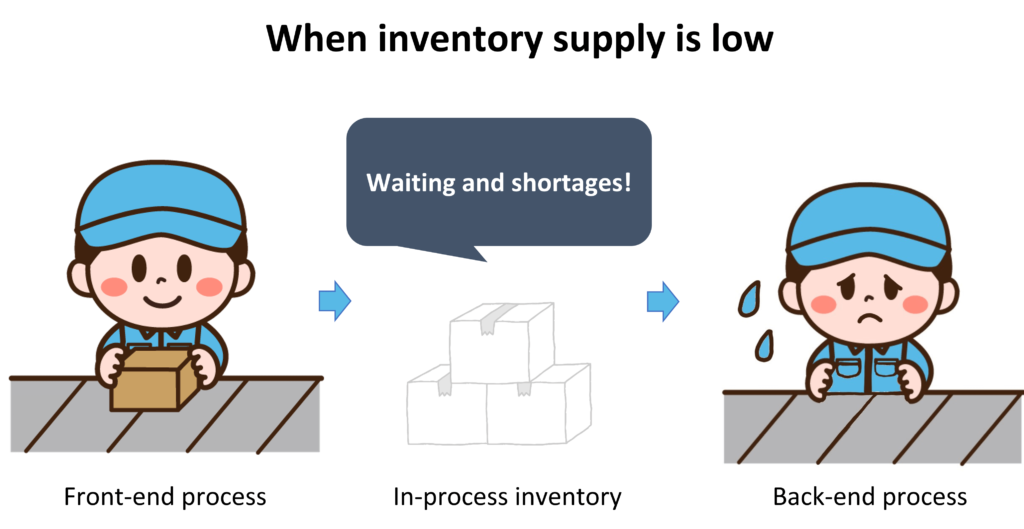
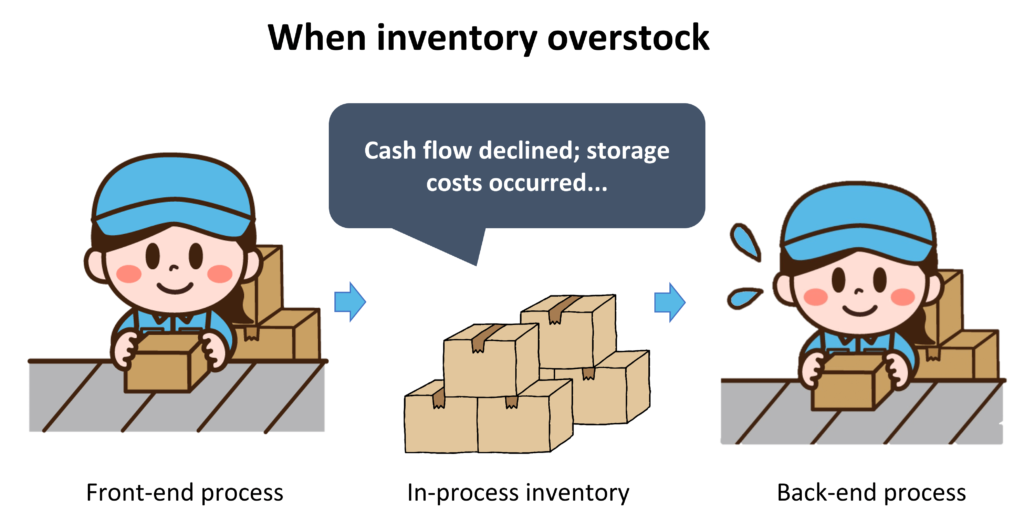
GD.findi can simulate not only production activities but also production plans, allowing us to “visualize” changes in the inventory status. We can see the transition of in-process inventory (work in progress) that is generated during the production process.
For example, consider a production line that is responsible for multiple productions, with a simple diagram of front-end process => back-end process. Let’s assume that a batch production plan for multiple products has been set up in the front-end process. The inventory buildup depends on the production plan, which is more difficult to predict because there are multiple products to be produced. Since inventory variation is determined by the relationship with the production plan in the back-end process, it is difficult to calculate such dynamic factors using a static tool like EXCEL. Furthermore, production does not always proceed according to the production plan but generally moves in a delayed direction, so it is necessary to incorporate these changes into the prediction of inventory variation.
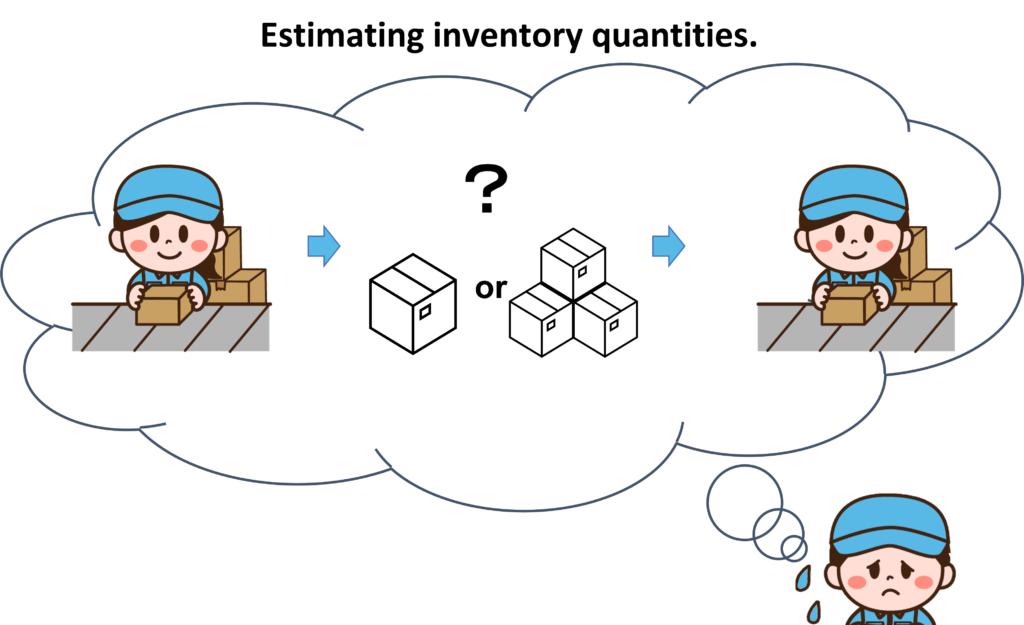
In GD.findi, you can set the “inventory” for each station, in-process inventory, and buffer at the initial point of running the simulation. By running the simulation with a certain amount of initial inventory, you can directly “observe” the transitions in the amount of inventory due to changes in the operating conditions of the front-end and back-end processes. By “observing” in simulation, it is possible to determine the minimum amount of inventory that will not cause waiting in the back-end process.
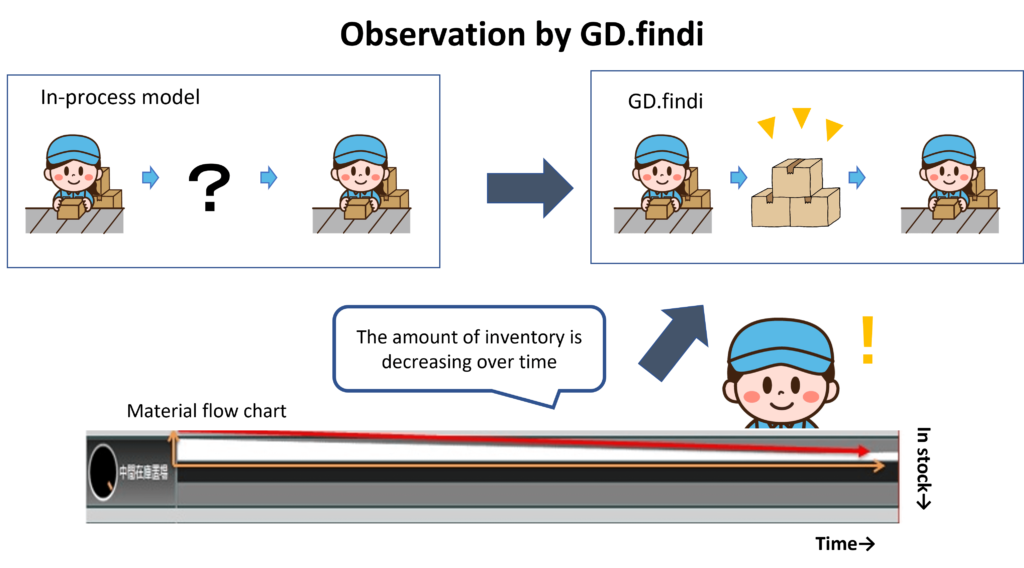
4. Verification of transition in in-process inventory
Assume a line where the processing capacity of the back-end process is lower than that of the front-end process, as shown in the figure below. If the front-end and back-end processes are to operate at full capacity, in-process inventory will face a short in supply and the back-end process will have to wait.
To cope with this situation, it is important to reduce the operating hours of the front-end process and increase the operating hours of the back-end process. The key point here is to find out how much in-process inventory needs to be carried in the front-end process operation.

For such cases, the “output log file” feature in GD.findi can output the simulation results as data to “observe” transition in inventory levels.
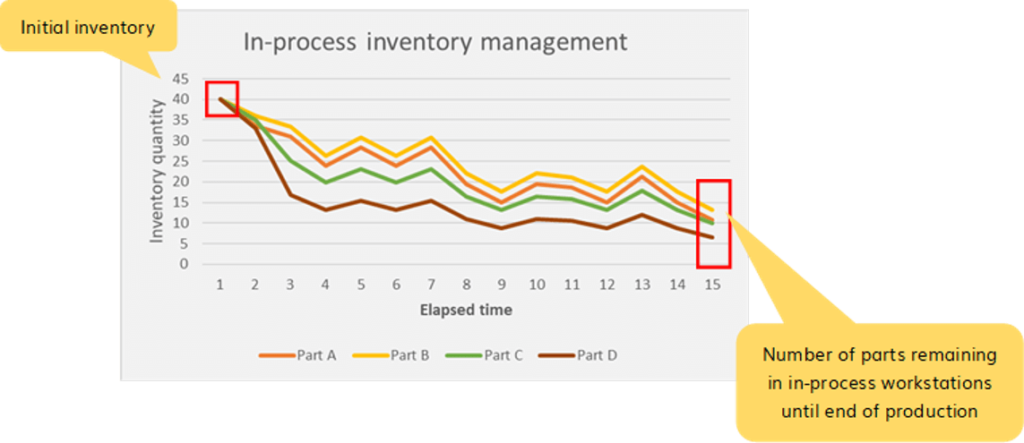
For example, as shown in the graph above, if we visualize the change in the number of inventories by parts and verify the change of in-process inventory, we can see that each part remains in the storage area at the end of production. Also, simulate the case where the initial inventory of Part A is reduced from 40 to 30 units.
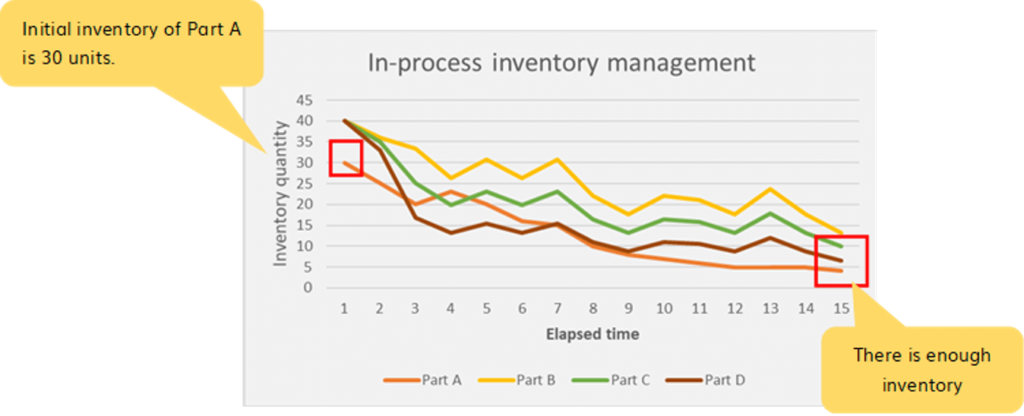
The transition graph shows that part A remains at the end of production. If the initial inventory of Part A is reduced from 30 to 20, there is now a shortage of the part before the production finish.
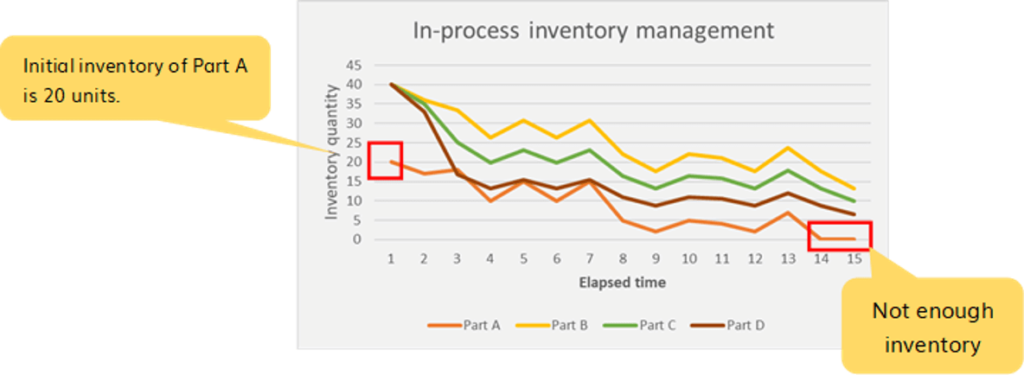
Based on the above “observation,” we can see that the amount of Part A needed to be in stock is 21 to 29 pieces to avoid shortages and overstocking, as well as to avoid waiting until the end of production.
By conducting such “observations” through simulations, focusing on the number of all parts in stock, it is possible to avoid waiting in the back-end process and identify the number of parts at the end of production.
Thus, we can “observe” the transition of the amount of in-process inventory by using the “initial inventory” feature, “production plan for each process,” and “output log file” in GD.findi. Although we did not explain it here, we can also reflect on the effects of parts loss due to production defects.
Please contact us if you are interested in our service.