Case: Shinano Camera Corporation
- Home
- /
- Newsroom
- /
- case
- /
- GD.findi MS
- /
- Shinano Camera Corporation
Virtualizing production lines to shorten manufacturing lead times.
Optimize work-in-process inventory by implementing complex factors such as changeover and human resources.
Shinano Camera Co. is a company based in Matsumoto City, Nagano Prefecture, Japan, that is entrusted with high-density board mounting and electronic device assembly. The company has been in business for 45 years, and its 120 employees produce products for various electronics manufacturers daily. The area we tested this time was the assembly process of electronic devices by workers, including soldering, assembly, inspection, and packaging.
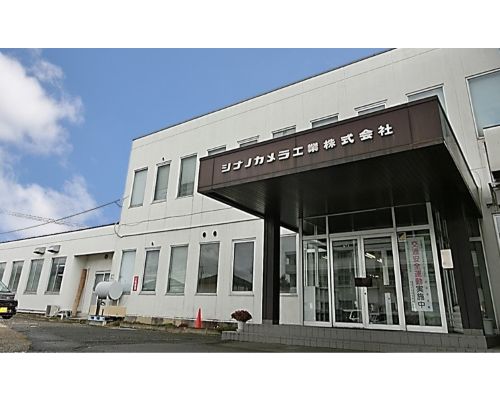
Introduction of GD.findi to its production line
The company’s production line had a large amount of in process inventory before and after each assembly process.
The Production Engineering Department assumed that reducing the work-in-process inventory between these processes would shorten the lead time, improve the cash flow, and increase the ability to receive extra orders.
In addition, the benefits of reducing work-in-process inventory were clear from the perspective of identifying problems in the production process and monitoring progress.
However, in order to change a production method that had been in place for a long time, it was necessary to overturn the preconceived notions of the production department, and theoretical data was needed to gain the agreement of all stakeholders.
In addition, even if we were to try out improvement measures on the actual production line, it would be unavoidable that changeover works and worker shortages would occur at the trial stage when the appropriate method has not yet been established, so it was considered risky to verify the improvement plan using the factory site.
Therefore, by using GD.findi, which allows virtual inspection, we assumed several patterns of improvement proposals that could be expected to be more effective, and tried to verify how much lead-time reduction could be expected by reducing in-process inventory and what level of in-process inventory would be appropriate in the simulation.
Benefits of implementing GD.findi
Specifically, first, conditions such as changeover, worker working hours, and work capacity were converted into parameters and entered (modeled) using the GD.findi GUI. Next, the number of work-in-process inventory in the target process was varied from 100 to 1, and simulations were conducted each time to establish guidelines on how varying the work-in-process inventory would affect the lead time and equipment utilization rate. We were then able to use the results to discuss logical and quantitative process improvements with the shop floor. In addition, the modeling and simulation took only about 10 days, so we found that it could be practically used for kaizen activities on the shop floor.
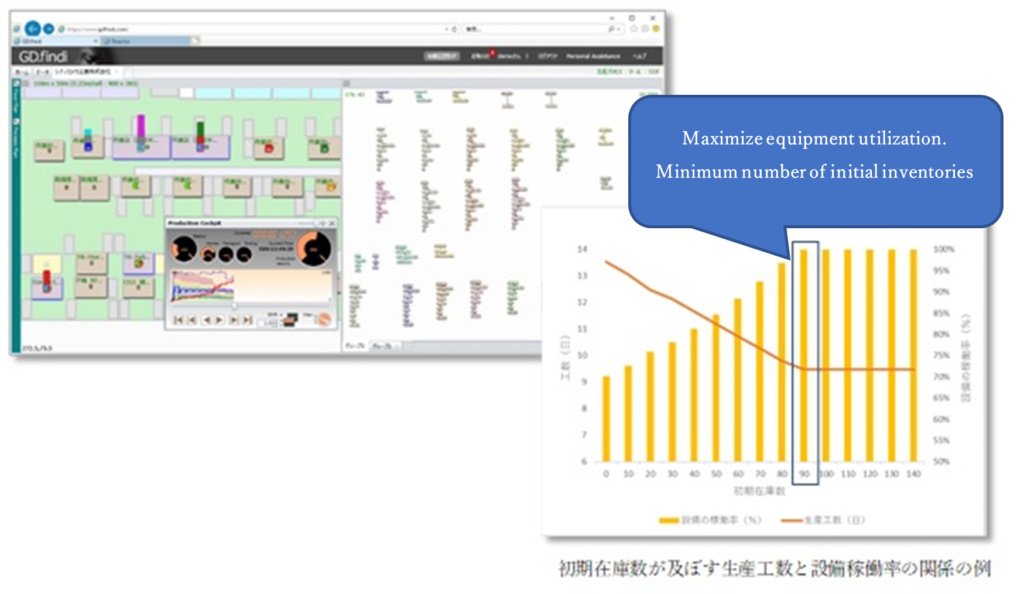
Customer Voice
“When we were introduced to GD.findi, we immediately understood that it would be effective in solving our problems. However, since we had never used a simulator before, we were concerned about the actual operation, such as data input and interpretation of the results.This was the first time I tried using a simulation, and I thought it was a software that could be used on the production floor, since it could be simulated simply by entering parameters through the GUI. In addition, we were able to achieve results in a short period of time because of the support based on Lexer’s know-how. In addition to the improvement activities, the quantitative simulation results obtained from GD.findi were useful as evidence to explain the theoretical return on investment when applying for subsidies for equipment installation.In the future, we will continue to optimize the entire plant.” said Mr. Kamiyama, the Head of Production Engineer department.
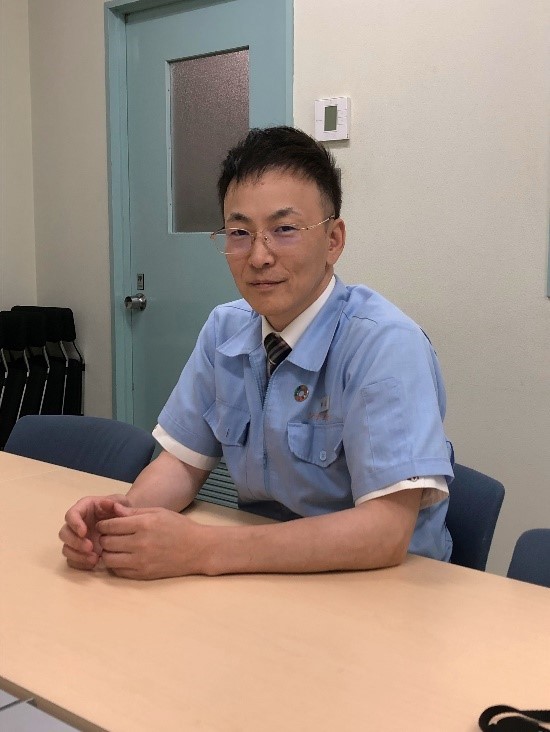