- GD.findiが解決できる課題
- 製品紹介生産活動の現場とサイバー空間をつなぐ 生産シミュレーション
GD.find MS
Modeling & Simulation
ライン設計を強力に支援する完全ノーコード生産シミュレータ - よくあるご質問
- 事例
- ウェビナー
- お役立ち情報
工程管理で重要視されている「FMEA」とは?
意味から具体的なステップまで解説
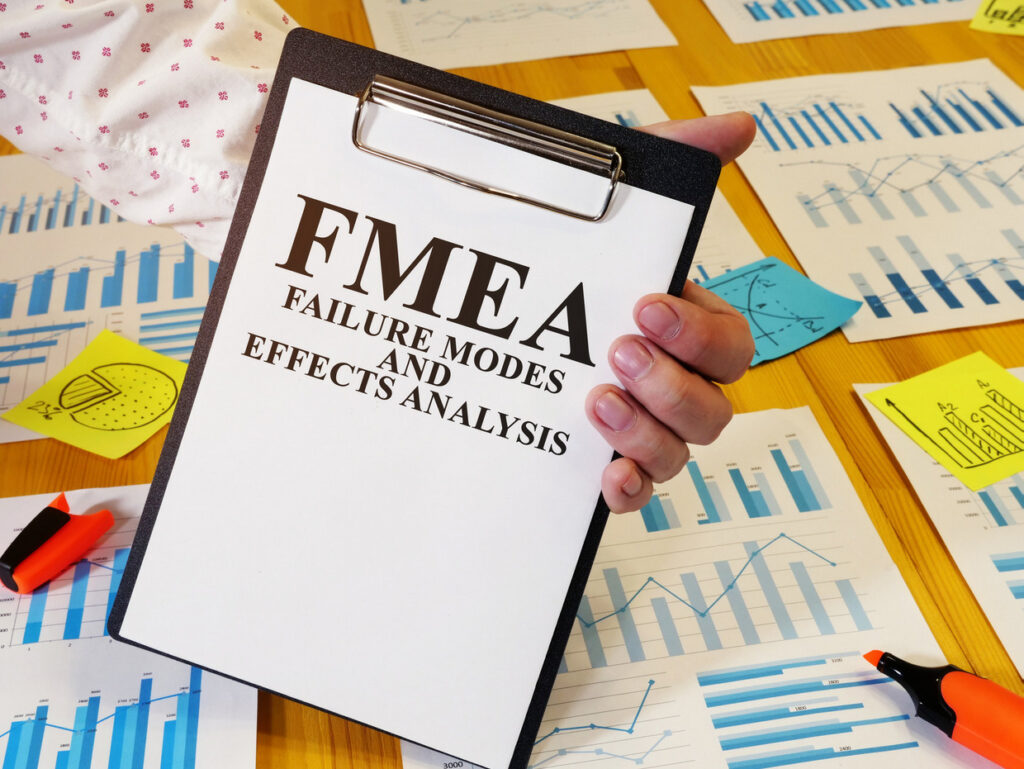
多くの分野でのイノベーションにより、これまでになく簡単に新しい製品やプロセスを作成できるようになりました。ただし、イノベーションの成功は私たちに生産性の向上(そしてより多くの自由時間)を与えてくれますが、それらがもたらすリスクが適切に管理されていない場合、そのメリットを打ち消す可能性があります。イノベーション段階でリスクを管理するのに役立つ主な手法の1つが、FMEAとも呼ばれるものになります。
FMEAとは、製品や製造プロセスに潜在的に潜んでいるリスクを設計段階で想定し、それぞれの影響度を鑑みて、予防措置をとることで品質を向上させる手法です。
この記事ではFMEAの概要から具体的な実施方法までわかりやすく解説します。重要性を認識頂き、適切な工程管理を実現し、リスクを最小限にする参考としてください。
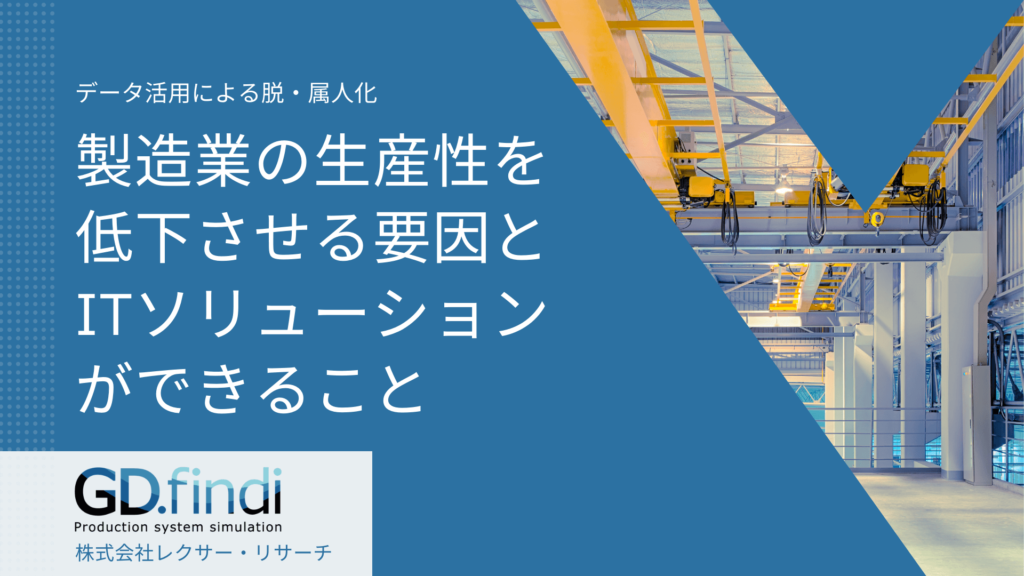
【無料 e-book】
製造業の生産性を低下させる要因とITソリューションができること
製造業の生産性を低下させる要因とITソリューションができること
本e-bookでは、日本の製造業の課題とその原因を再確認しながら、課題解決のために導入したいITについて解説します。
FMEAとは
FMEAとは「Failure Mode and Effects Analysis」の略で、日本語に訳すと「故障モード影響解析」となります。製品や製造プロセスで発生する可能性がある、様々なリスク(故障モード)を設計段階で洗い出し、取り除くことで、リスクを排除する手法のことです。事故等が起きてしまってから再発防止に努めることももちろん大事ですが、事前に事故が起きる可能性を一つでも潰していくことで、被害を未然に防ぐことが出来るのです。
実際にFMEAを考える際は、対象業務ごとに細分化されることがあります(設計段階では設計FMEA、作業段階では作業FMEAなど)。その中で、製造工程において適用する場合を、工程FMEAと呼びます。実際の製品の製造工程に潜在する様々なリスク(故障モード)を洗い出し、トラブルを予防します。
FMEAは、生産プロセスまたは製品の潜在的な故障モードとそれらが顧客に与える影響を特定する体系的な方法です。その目的は、人命の損失、手足、または物的損害につながる可能性のある操作上の障害を防ぐことです。
故障モードが発生する可能性のあるすべてのオペレーションと、故障モードが安全性または製品品質に及ぼす可能性を特定することです。 FMEAは、飛行乗務員の訓練、風力タービン設計での負荷計算、高速道路のレイアウトなど、他の非日常的な状況にも適用されています。
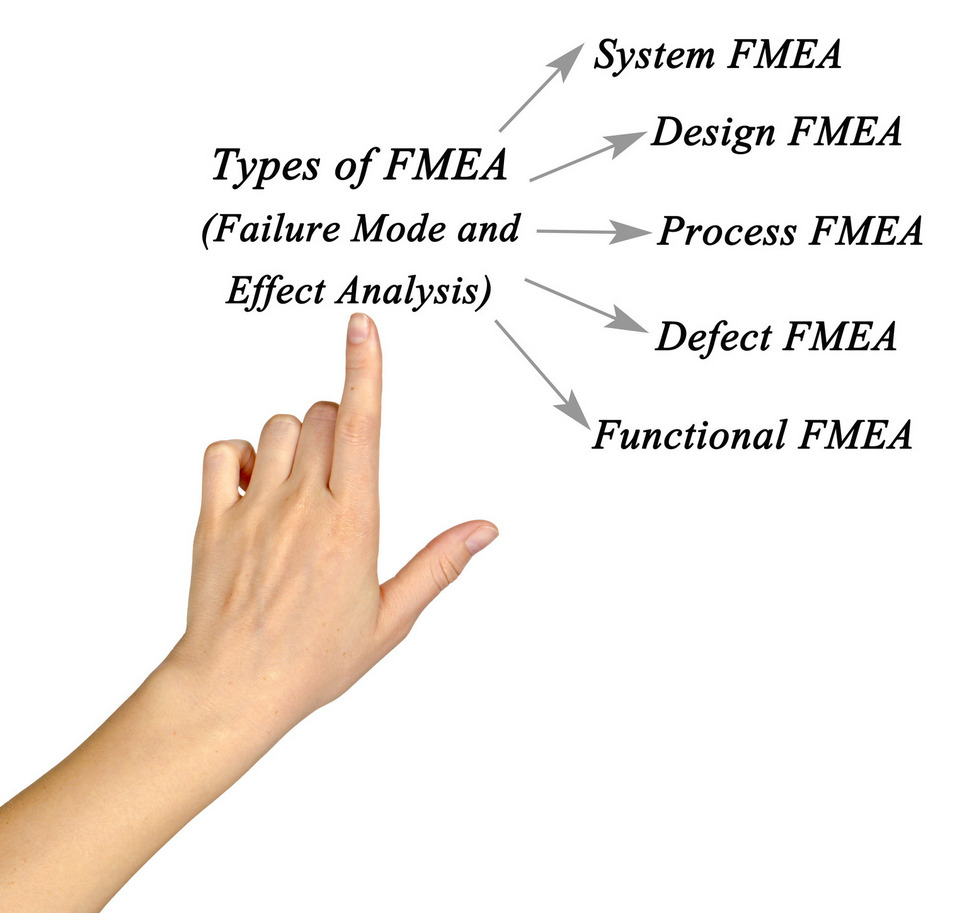
FMEAとリスク分析の違い
多くの人がFMEAをあらゆる種類のリスク分析の総称として使用していますが、リスク分析とFMEAには違いがあります。リスク分析は、危険を特定し、安全対策または手順を適用することによってそれらを管理する継続的なプロセスです。 FMEAはさらに、問題が発生する前に何が問題になる可能性があるかを特定し、問題が発生する前に設計段階でリスクを排除しようとします。
実際に、従業員の操作ミスによる廃棄品の発生を例に考えてみます。
なぜ廃棄品が発生したのか、操作ミスはなぜ起きたのか、防ぐための手立ては何があったのかなど、既に何か問題が起きた後に、詳細を掘り下げていく事で、事故の根本原因を特定し、再発防止に繋げていくのが、リスク分析になります。
一方で、この製造ラインにおいて、操作ミスが発生すると廃棄品が発生する可能性を事前に考慮して、操作ミスを防ぐための機能を追加する、等の予防策を実施するのがFMEAです。
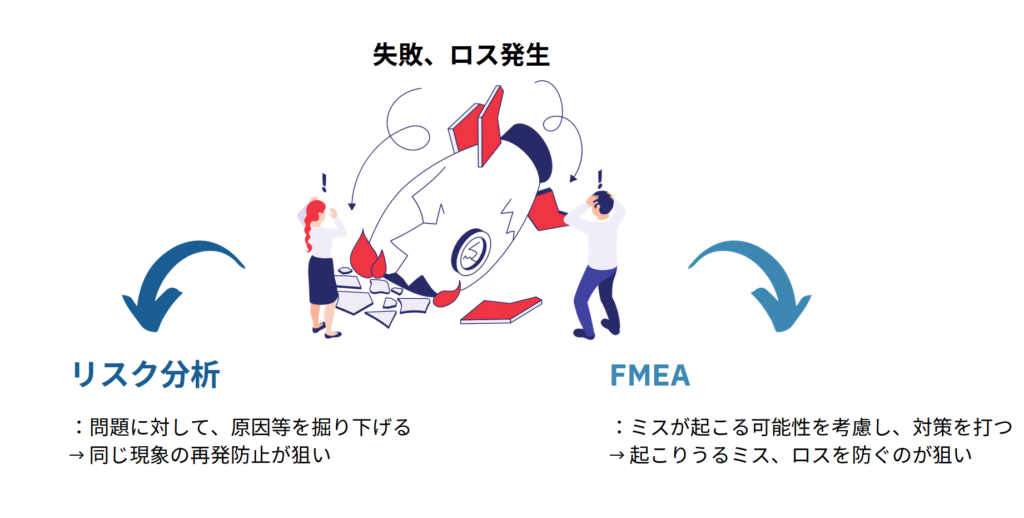
FMEAを実施することで、事前に事故の可能性を減らすことが出来ますが、全てを事前に予想して対策をとるのは、不可能です。
そのため実際にオペレーションを実施する中で、リスク分析は当然必要になります。しかし、何もリスクを事前に検討していない場合に比べて、FMEAを実施しておくことで、リスク分析が必要になる場面を減らせることが出来ます。
故障と障害の違い
新しい製品やプロセスを設計する際に、FMEAを実施しようとすると常にどこにでも失敗の可能性があると思うかもしれません。「故障モード」という用語の定義は、“製品またはプロセスが顧客の要件または期待を満たさないことにつながる、またはその原因となる可能性のある一連の条件(またはイベント)”です。
この「故障モード」という単語には、大きく2つの意味が内包されています。それが、故障と障害です。故障とは、事故、怪我、損傷、紛失などの望ましくない結果をもたらす出来事です。障害は、潜在的な障害(正しく機能しておらず、気付かなかったもの)または明白な障害(失敗して検出されたもの)のいずれかを指します。
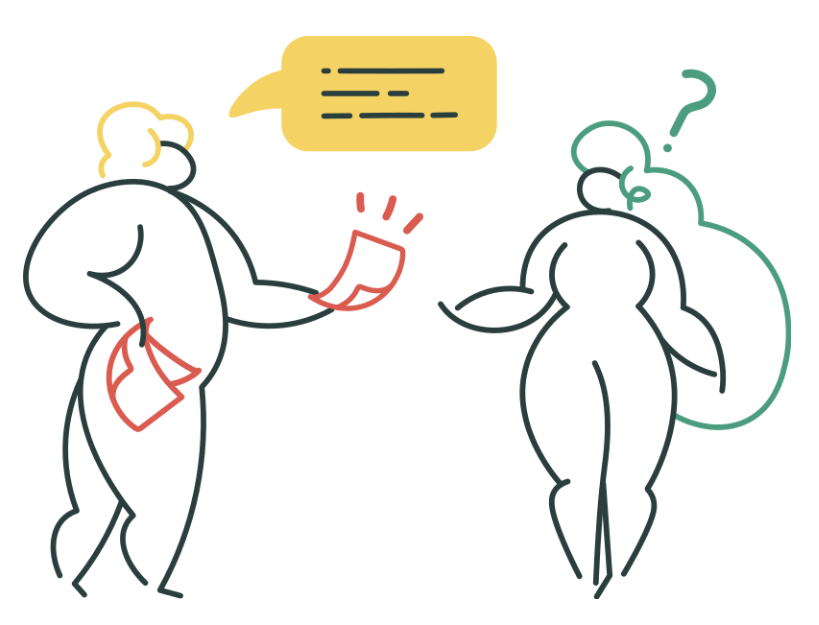
FMEA はどのように実施するのか?
次に、FMEAを実施する際の具体的なステップを見ていきましょう。
1. まず、製品またはプロセスで発生する可能性のあるすべての障害モードを特定します。
2. 次に、各障害モードの影響(結果)を特定します。
3. 最後に、影響を分析し、
4. 障害が発生するリスクを排除または削減するために何を行う必要があるかを決定します。
このタスクは、ブレーンストーミング、フローチャート、ランキングなど、さまざまな方法で実行できます。
FMEA において考慮する必要があること
また、FMEAを作成するときは、次のそれぞれを考慮する必要があります。
1. 製造プロセス
製造プロセスには多くの機械が含まれ、障害が複数発生することを意味します。製造ラインの複雑な相互依存性と相互作用があるプロセスを特定するために、丁寧な分析を行う必要があります。
2. 内部検査
故障は環境要因だけでなく、生産システム自体の故障によっても引き起こされます。これが、製造プロセス内の潜在的な欠陥や危険を特定し、それに応じて製品を設計することが重要である理由です。
3. 外部検査
失敗する可能性のあるもう1つの領域は、顧客が製品を初めて使用するときです。
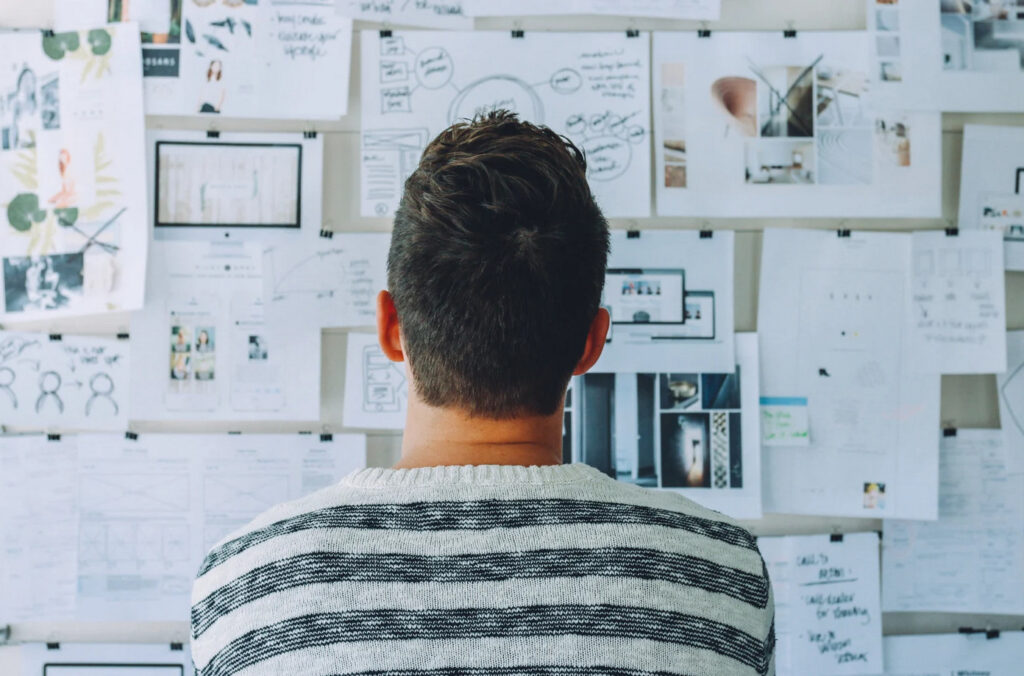
FMEA において重要なポイント
FMEAを実施する際に覚えておくべき最も重要なことは、これらの手順を成功させるには、調査中の製品や製造プロセスを完全に理解する必要があるということです。調査している製品またはプロセスに対する知識・理解だけでなく、それらを操作する人々の両方についての完全な理解が必要です。なぜなら、オペレーターのスキルレベルを含むヒューマンエラー要因は、障害の結果にさらに2次的に影響を与える可能性があるためです。
FMEAを正しく適用し、それから最大の利益を得ることができるようにするには、プロセスまたは製品のオペレーターは、最初に、どの障害モードがレビュー中のアプリケーションに影響を与えるかを判断する必要があります。これには、発生する可能性のあるすべての考えられる障害モードを理解する必要があります。これを完全に行うには、コンポーネントや相互関係など、調査中のプロセスを完全に理解する必要があります。
まとめ
FMEAとは、製品や製造プロセスで発生する可能性があるあらゆるリスクを事前に洗い出し、そのリスクによる影響を特定し、影響が大きいリスクに対して予防策を立てる事です。
既に発生した不具合に対して、再発防止を検討するようなリスク分析ではなく、将来のリスクについて対策を講じる手法です。この手法を実践するためには、対象となる製品や製造プロセスに対する深い理解だけでなく、実際に作業を行う従業員への理解も必要になります。
製品・製造プロセス自体の欠陥による危険に加えて、ヒューマンエラーによって引き起こされる事態についても、事前に洗い出すことが必要になるためです。

【無料 e-book】まずはできるところから!
製造業が生き残るためのIT活用
本e-bookでは、製造業におけるデジタル化の影響をとらまえながら、With/After コロナで製造業が勝ち抜くためのアプローチについてご紹介いたします。
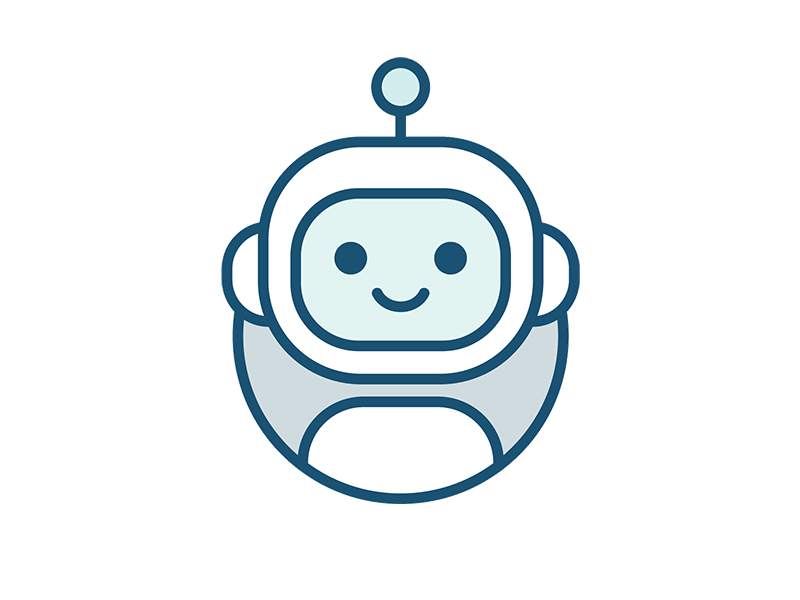
著者情報
山上 玲奈(株式会社レクサー・リサーチ マーケティング担当)