- GD.findiが解決できる課題
- 製品紹介生産活動の現場とサイバー空間をつなぐ 生産シミュレーション
GD.find MS
Modeling & Simulation
ライン設計を強力に支援する完全ノーコード生産シミュレータ - よくあるご質問
- 事例
- ウェビナー
- お役立ち情報
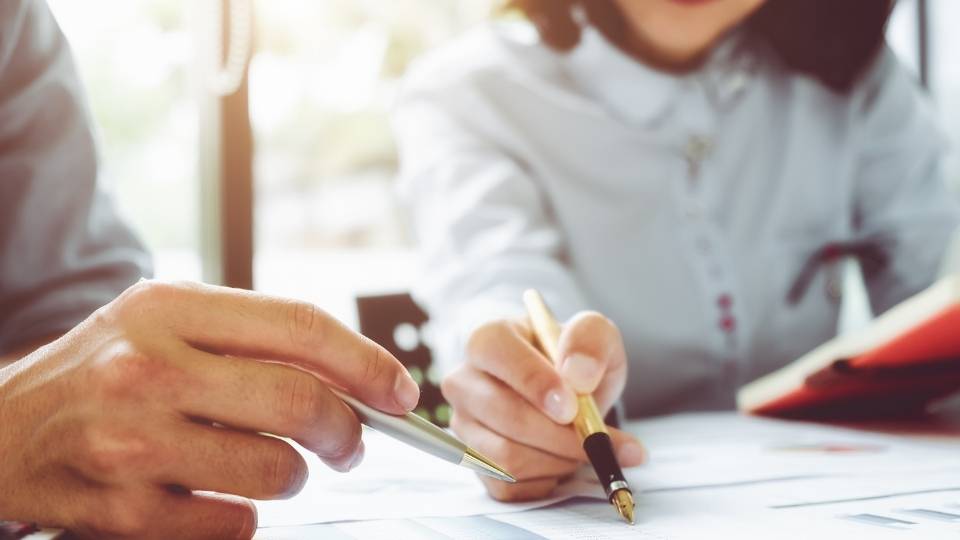
生産計画とは?
生産計画とは、「何を(製品)」「いつ(時期)」「どれくらい(数量)」生産するかを計画することを指します。また、日本産業規格(JIS)では「生産量と生産時期に関する計画」と定義しています。生産計画には、生産にどのような材料や部品が必要で、どのような設備を使うか、どのような生産工程で行うかが含まれます。製造準備から出荷に至るまでのすべての日程を対象とします。
生産計画の目的
需要を満たす
需要の変動を予測し、必要な製品を必要な量だけ、必要な時期に生産することで、需要と共有のバランスを取ります。
生産効率UP
生産設備や人員配置などを最適化し、生産ラインの稼働時間を最大限に活用する。作業工程を合理化し、無駄な動きや待ち時間をなくすことで生産効率を向上させることができます。
在庫を最適化する
過剰在庫や在庫不足をなくし、在庫コストを削減することができます。
コスト削減
必要な人員や原材料、設備などの資源を効率的に活用し、コストを最小限に抑えながら生産活動を行います。
生産計画は、製造業にとって非常に重要な活動です。 上記の目的を達成することで、企業の競争力を強化し顧客満足度向上が期待できます。
生産計画の種類
生産計画は、期間の長さの観点から以下の3つに分けられます。
長期生産計画
長期生産計画は6ヶ月~1年、または数年単位におよぶ長期的な生産計画です。企業の経営戦略に基づいて将来的に必要となる生産量や資源を予測し、具体的な計画を策定するものです。また製品ラインの追加や設備の更新などの大規模な投資や、海外進出、研究開発計画などを含む戦略的な決定も含まれます。経営戦略と密接に連携し、企業の長期的な成長と持続可能性を支える土台となります。
中期生産計画
中期生産計画は長期生産計画に基づいてより具体的な計画に落とし込みます。期間は1ヶ月~6ヶ月程度です。各工程の作業時間や作業順序を計画する生産スケジュールや作業指示を決定するために、現場のシフトを考慮した人員配置、必要な原材料を適切な量とタイミングで調達するための資材調達スケジュール、生産量や生産ペースなどを策定します。
短期生産計画
短期生産計画は、中期生産計画に基づいて、工場や現場レベルで1週間から1ヶ月程度の短期的な生産スケジュールや作業指示を策定します。毎日もしくは毎週見直され、生産進捗状況をモニタリングし必要に応じて計画を調整、日々の需要や設備・人員などのリソースの変動、トラブル発生時の対応など状況に応じて柔軟に対応できるような備えが必要になります。
3つの生産計画はそれぞれ異なる役割をもちながら互いに連携して一貫した生産体制を実現します。
生産計画の立て方
生産計画の立て方について以下のステップに沿って解説します。
ステップ1:需要予測の確認
需要予測は生産計画の出発点であり計画全体の精度を大きく左右します。代表的な手法とその特徴をご紹介します。
過去の販売データ分析
過去の販売データに基づいて、将来の需要を予測する方法です。平均法や移動平均法、指数平滑法など、様々な統計手法を用いてデータ間の関係や影響を調査します。そこから季節性やトレンドを把握していきます。過去の傾向が将来も続くという仮定に基づいているため、市場環境の変化などに弱いという欠点があります。
市場調査
顧客へのアンケート調査や市場調査会社による調査などを通じて、将来の需要を予測する方法です。消費者の嗜好やニーズを直接把握できる、競合他社製品の情報を得られる、というメリットがありますが、調査の費用や時間がかかるというデメリットがあります。
顧客からの受注量予測
過去の顧客からの受注量を分析し需要のトレンドや季節変動などを把握する事が出来ます。合わせて顧客属性を分析する事でニーズや購買行動を理解する事が出来ます。
経済指標の分析
GDP成長率や失業率などの経済指標に基づいて、将来の需要を予測する方法です。消費行動に影響を与える景気動向と需要の関係性を分析することで、ある程度の予測が可能になります。
機械学習
過去の販売データや市場調査データなどを機械学習モデルに入力し、将来の需要を予測する方法です。過去のデータから複雑なパターンを学習し、高精度な予測が可能になります。しかし、モデルの構築や運用に専門知識が必要となるというデメリットがあります。
受注量予測は、あくまで不確実性を伴う事を認識し、単独で行うのでなく他の需要予測手法と組み合わせることでより精度の高い予測が可能になります。
ステップ2:生産能力の確認
需要を満たすために必要な製品を計画通りに生産できるかどうかを判断するためには生産能力を正しく把握することが必要になります。生産能力の確認は以下の方法で行う事が出来ます。
生産設備の確認
保有する生産設備の種類や数量、生産速度、稼働時間などを個別に確認します。そこから各設備の稼働率、故障やメンテナンスの頻度を確認して生産能力を把握します。
人員の確認
作業人員の数、スキル、労働時間などを把握し生産能力における人的リソースを理解します。また労働時間やシフトパターン、残業の可能性なども確認します。また必要に応じて、労働環境改善や教育訓練プロクラムを実施します。
サプライチェーンの確認
原材料や部品の供給元、製造工場、物流センターなどのサプライヤーの供給能力を確認します。必要に応じてリードタイムを短縮するための対策を講じます。
生産シミュレーションの実施
生産設備や生産工程を元に生産シミュレーションを行い、生産能力を評価します。これにより、さまざまなシナリオや変更点に対する影響を評価し、生産能力の最適化策を検討することが可能となります。
ボトルネックの特定
生産プロセスにおいてボトルネックとなる工程や設備を特定します。ボトルネックとなる部分が生産全体の能力を制限している可能性があるため、ボトルネックの特定と解消が必要になります。
生産実績データの分析
過去の生産実績データから稼働率、生産速度、生産効率などを把握し、実際の生産能力を評価します。
生産能力を正確に確認するには定期的な見直しが必要になります。市場環境の変化や設備の老朽化による能力低下、供給遅延等のサプライチェーン内のリスクなど様々な要因による影響が出るため注意が必要です。
ステップ3:生産量の最適化
需要予測と生産能力確認に基づいて最適な生産量、つまりは需要を満たしながら生産コストを最小化するような生産量を決定します。過去の生産実績や経験に基づいて最適な生産量を決める事も少なくありません。その際は生産需要変動や生産トラブルなどの経験からこういった場合に備えて在庫を確保しておく安全在庫も考慮します。他には生産シミュレーションを使って様々な生産量シナリオをシミュレーションし、それぞれのシナリオにおける利益、在庫レベル、生産コストなどを比較分析、最適な生産量を算出する方法や、ソフトウェアを使用して生産量、在庫量、生産コストなどを考慮した最適な生産量を算出する方法などがあります。
ステップ4:生産スケジュールの作成
最後に生産計画を具体的な生産スケジュールに落とし込みます。製品ごとのリードタイム、リソース(人員、設備、原材料)とその割り当て、作業手順、納期や生産順序や優先度などを考慮した上で生産スケジュールを作成します。多くの企業では生産スケジュールをExcelで作成しています。使い慣れたツールであり導入コストを抑えられる、テンプレートが多数あるなどのメリットが挙げられます。また一方でデータの入力や修正が手動であるため時間がかかる、業務が属人化する、データ管理が面倒などの理由から生産スケジューラソフトを導入する企業も増えています。
生産計画の実施と評価
実施:生産スケジュールの管理
生産計画を実際に実行し計画通りに進めるために重要なのが、生産スケジュールの管理です。注意するポイントを以下に挙げていきます。
情報共有
生産スケジュールは、関係者全員が共有し、常に最新の状態を把握できるようにする必要があります。そのため、社内ネットワークや生産管理システムなどを活用して、計画情報を共有する仕組みを構築する必要があります。またサプライヤーなどの関係者とも定期的に情報共有を行い必要時には調整します。
進捗状況のチェック
実際の生産が生産スケジュール通りに進捗しているか、実際の生産実績を記録して定期的にチェックする必要があります。進捗状況が遅れている場合は、遅延の原因を特定して対策を講じる必要があります。
生産スケジュールの修正
予期せぬトラブルや顧客からの要望などによりスケジュールを変更する必要が出てくることがあります。必要に応じて生産スケジュールを調整し、生産ラインやリソースの利用を最適化する必要が出てくるため、迅速かつ柔軟にスケジュールを修正できる体制を構築する必要があります。
評価:生産計画の改善
生産計画は定期的に評価し、常に改善していく必要があります。より精度の高い生産計画を作成するためのポイントを以下に挙げます。
生産実績の分析
実際の生産実績を分析することで、計画と実績の差異を明らかにすることができます。差異の原因を分析し、計画に反映することで、より精度の高い計画を作成することができます。実際の生産実績を分析することで、予定と実績の差異を明らかにします。生産量、生産時間、品質、コストなどの指標を評価し、生産効率改善の方向性を把握します。
フィードバックの収集
生産ラインの作業者や管理者などの関係者からフィードバックを収集します。そこで挙げられた意見や提案を活用し、改善のポイントを特定します。また顧客からのフィードバックがあればそれを分析することで製品に対する顧客のニーズを把握し、より顧客満足度の高い生産計画を作成することができます。
継続的な改善
継続的に行う改善活動を通して、定期的に生産計画や生産プロセスを評価し、改善の成果を確認します。そして必要に応じて生産計画を修正していきます。
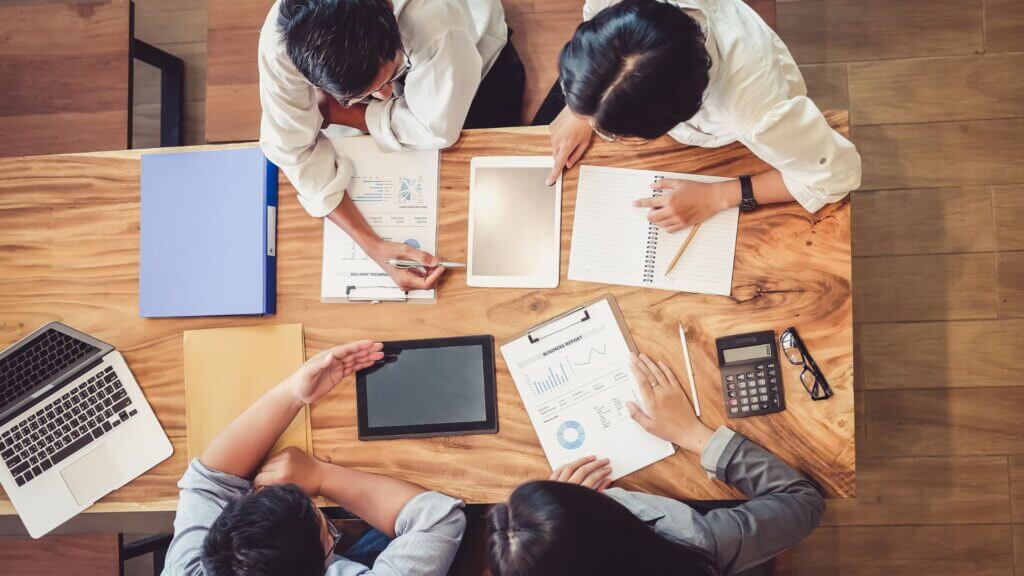
生産計画の課題と解決策
生産産計画を立案・実行・評価する過程においては様々な課題が発生します。ここでは3つの代表的な課題とそれぞれの解決策について解説します
課題1:需要予測の精度が低い
需要予測の精度が低くなる主な原因は下記が挙げられます。
・データ不足
過去の販売実績、市場調査データ、顧客からの受注データなどの需要予測に必要となるデータが不足している場合、精度の高い需要予測を行うことはできません。
・予測方法が適していない
前項で挙げたように需要予測には様々な方法があります。しかし、どの方法にも長所と短所があるため、状況に合っていない方法を誤って選択したり、適切なパラメータを設定しなかったりすると、精度の低い需要予測となる可能性があります。
・外部要因の考慮不足
経済情勢、競合他社の動向、天候など、様々な外部要因を考慮せずに需要予測を行うと、実際の需要と大きく乖離してしまう可能性があります。
・組織体制の不備
需要予測は、マーケティング部門、営業部門、生産部門など、様々な部門が連携して行う必要があります。しかし、部門間の連携がうまく取れていない場合、必要なデータが共有されなかったり、意思決定が遅れたりして、精度の低い需要予測となる可能性があります。
需要予測の精度が低いと不要な在庫を抱えてしまい在庫コストの増加や資金繰りの悪化につながってしまったり、逆に在庫不足が発生し、顧客への納期遅れや機会損失につながります。
解決策:需要予測の改善
需要予測の精度を向上させるためには、以下のような方法があります。
データ収集・分析の強化
過去の販売データ、市場動向データ、顧客データなどより豊富なデータを活用し、より精密な予測モデルを構築します。時系列分析や回帰分析などの統計手法を適用して、需要のパターンや関連要因をより詳細に把握します。
外部要因の考慮
需要に影響を与える天候データ、経済指標、競合他社の動向などを取り込み、外部環境の変化による需要への影響をより正確に評価します。
テクノロジーの活用
AIや機械学習を用いた需要予測手法は、過去のデータから需要パターンを自動的に学習し、高精度な予測を行うことができます。大規模やデータ解析や複雑なパターンの検出が可能になります。
これらの対策を講じることで、より精度の高い需要予測を行うことができ、生産計画の精度を高めることができます。
課題2:生産能力が十分でない
生産能力不足の主な原因は下記が挙げられます。
・設備不足や設備の老朽化:生産に必要な設備が足りない、また設備が老朽化により生産効率が低下したり故障が多発したりする。
・人員不足:生産に必要な作業員が不足している。
・資材不足;生産に必要な資材が不足している。
・生産プロセスの非効率性:設備稼働率が低い、熟練作業員がおらず作業に十分なスキルがまだ身についていない、移動距離が長い、不良品が多いなどにより生産効率が低い。
このような原因により生産計画に対しての生産能力が十分でないと、納期遅延による顧客満足度の低下や売上損失、残業や設備の過負荷によるコスト増大や従業員のモチベーション低下などの問題が発生します。
解決策:生産能力の拡大
生産能力を拡大するには、以下のような方法があります。
設備投資
新しい設備を導入したり古い設備を更新したりすることで生産能力を拡大します。
人員増強やスキルの習得
作業員を増員する、作業効率を向上させるための教育・訓練を実施したりすることで生産能力を拡大します。
生産プロセスの改善
レイアウトを見直す、作業方法や手順を標準化する、品質管理方法を見直すなどにより生産プロセスを改善して効率を上げることで生産能力を拡大します。
アウトソーシング
一部の工程を外部の生産パートナーに外注することで、生産能力を補います。
生産能力を拡大する際には、投資対効果、リードタイム、品質管理などを考慮する必要があります。
課題3:生産スケジュールの乱れ
生産スケジュールが乱れてしまう一般的な原因を下記に挙げます。
需要変動への対応不足
顧客からの急な受注増加や製品仕様の変更などにより需要が変動した場合に、生産スケジュールの調整が対応できず乱れが発生します。
設備故障
生産設備の予期せぬ故障やメンテナンスが必要になった場合、生産ラインの停止や遅延が生じる可能性があります。
部門間の連携不足
生産計画についての業務フローが整理されておらず、販売部門と生産部門の連携が不十分な事により、生産能力を超える受注を獲得してしまったり、無理な納期を設定してしまう場合があります。
生産スケジュール立案の属人化
生産能力負荷見積や計画割付の優先順位などの、ベテラン作業者の頭の中にある情報に頼っており生産スケジュール立案のロジックやノウハウを標準化できていないため業務が属人化してしまいます。それによりベテラン担当者から変わると引継ぎがうまくいかず、これまでの精密なスケジュールを作成できずに生産現場は日々の計画変更に追われてしまい生産スケジュールが乱れます。
生産スケジュールが乱れると、納期遅延やコスト増大、品質低下等の問題が発生します。
解決策:生産スケジュールの見直し
生産スケジュールの乱れを防ぐためには、定期的に生産スケジュールを見直す必要があります。見直しを行う際のポイントをご紹介します。
情報共有
生産部門、資材部門、品質管理部門などの関係者とリアルタイムな情報共有を行う事で生産スケジュールの進捗状況や問題点を早く把握する事ができます。
柔軟性を持たせる
予期せぬトラブルが発生した場合に備えて、生産スケジュールを柔軟に調整できるような、バッファの設定やリソースの優先順位付けルールなどの仕組みを導入しておきます。
ツールの活用
生産スケジューラなどのソフトウェアを活用して、ガントチャートやPERT図などで関係者に可視化した上で情報を共有できたり、データ分析によりスケジュール管理を効率化したり、全体の状況把握を容易にすることが期待できます。
継続的な改善
生産スケジュールの見直しを含む継続的な改善活動を実施します。定期的なレビューや反省を通じて、問題点や改善の余地を見つけ出し、生産スケジュールの精度を向上させます。
生産スケジュールの見直しは、机上の作業ではなく、現場の声を聞きながら進めること、また継続的に行う事が重要です。
まとめ
本記事では生産計画の基本情報から計画の立て方、よくある課題とその解決方法についてご紹介しました。生産計画は、製造業において、経営戦略を実現するための重要な活動です。生産計画を適切に運用、管理する事で顧客満足度の向上、利益の最大化、業務の効率化を実現することができます。
記事発行日: 2024年4月26日